Press release
How much a forklift truck battery costs per hour. Making the right financial decisions in uncertain times.
MONTGOMMERYVILLE, PA, November 16th 2020: It’s been a hard year to predict. The figures that are going to be used to forecast 2021 and the years that follow are going to take some time to navigate! But the world keeps on turning, and that means everyone will have to take a slightly more realistic approach when creating a roadmap for the future.Planning and coordinating the energy requirements needed to keep an operation running smoothly is no exception. The increase in logistical demand from e-commerce sales doesn’t look like it’s going to slow down over the years to come, the pandemic has brought the way people shop into sharp relief.
With a plethora of choices available on how to store energy, one of the most important factors to consider in uncertainty, is cost. With the sales line having peaks and valleys over the past few months, having a clear understanding of the true cost of purchasing, charging and using batteries is one clear path we can take to make the right decision.
So, we have decided to look at how much a battery costs per hour. We’ve used the data generated by the products Philadelphia Scientific manufactures to maximize the performance of lead-acid batteries, alongside the facts and figures given from lithium ion suppliers in our calculations.
The new generation of lithium batteries are being offered now with a guarantee of 10,000 working hours. We’ve taken that as a base point and calculated this in comparison to an equivalent lead-acid battery.
So, if a lead-acid battery for an order picker costs $4000 and with a 10,000-hour guarantee, that works out to a cost of $0.40/hour for storing that energy. If you add in the maintenance costs to keep them running as they should be, the total cost would average to $0.60/hour.
If the equivalent lithium battery costs $11,000 with the same 10,000-hour guarantee that equates to a cost of $1.10/hour cost. That gives you two options and two clear cost points:
1. Fully maintained flooded lead acid - $0.60/hour
2. Maintenance free lithum - $1.10/hour
Now that’s on a single battery. The increase on logistical demands has meant that more trucks and batteries are needed to keep everything running smoothly.
Taking a 20 lift truck site that runs an average of 2000 hours per year:
1. Fully maintained lead acid - $104,000.
2. Lithum-Ion - $220,000.
So, over a 5-year period running at 10,000 hours, the costs work out to be:
1. Fully maintained lead acid - $20,800/year.
2. Lithum-Ion - $44,000/year.
That’s a total cost difference of $116,000 just on purchase and running the batteries, it doesn’t include any of the additional charger & infrastructure costs needed. This data isn’t a secret. It’s available to anybody and everybody. We understand that different battery technologies are suited to different applications and there isn’t a one size fits all, especially in uncertain times.
As you can see there is a considerable difference in costs between Lithium-Ion and lead-acid batteries but that’s not the only factor to consider. Both options have their pros and cons. While Lithium-Ion maybe maintenance free it does involve following a strict charging regimen, lead-acid batteries need maintaining, equalization and handling on larger operations.
For the single forklift truck at the back of a store, Lithium-Ion would likely be perfect. Plug it in at the end of the day and it's ready to go at the start of the next. Simple. If the operation is a lot larger, running two or even three shifts, then it gets a little more complicated. Due to the way that Lithium-Ion batteries store and release energy, to get the best performance out of them, they need a consistent charging regimen to be followed. The trucks will need to plugged-in on breaks and lunches to maintain their charge, making sure that the voltage doesn’t drop and leave the truck stuck in an aisle. In larger operations, this means that there needs to be both space and the infrastructure available to charge the batteries regularly, the training to follow the charging regimen and the ability to meet the costs of the increased energy demand. There are a lot of separate components that need to be considered with a full Lithium-Ion operation, but it does eliminate the need for maintenance and handling.
A lead-acid battery in a single forklift truck at the back of the store, in all likelihood, isn’t going to last anywhere near as long as it should because maintenance is probably going to be pretty low down on the priority list. This can lead to the battery drying out, sulphating and in turn, not lasting anywhere near as long as it should. On larger operations, while lead-acid acid batteries need maintenance, there are tools and processes available to reduce maintenance time, leading to a total cost of less than $25 cost over the lifetime of a battery. It does require an area for battery changing, but in most cases, this is smaller than the space needed to charge a shift's worth of Lithium-Ion trucks. A truck using a lead-acid battery can also go from empty to full in under 4 minutes with a battery change, and the empty battery can be charged at more optimal times in the day so power is not being drawn at peak times. There are also products available that can split the chargers, effectively doubling the charger capacity without the need for additional infrastructure. Not only will this save a considerable amount of capital, but it also allows an operation to expand capacity quickly and easily.
As you can see there are pros and cons to both, ultimately this decision comes down to what is best for any given operation. So, if price is your beacon, then hopefully this data can help shine a light and help you make the right financial decisions.
If you’d like more information on what data our products can offer you visit https://www.phlsci.com
207 Progress Drive
Montgomeryville, PA 18936
USA
MEDIA CONTACT:
Andy Napoleon Hill
+447553 932 367
Andy.hill@phlsci.co.uk
Since 1983, Philadelphia Scientific has brought advanced technology solutions to the industrial battery industries around the world. The company specializes in the research, design, development, and manufacturing of industrial battery components and tools that maximize battery performance. For more information about Philadelphia Scientific, visit the company’s website at www.phlsci.com.
This release was published on openPR.
Permanent link to this press release:
Copy
Please set a link in the press area of your homepage to this press release on openPR. openPR disclaims liability for any content contained in this release.
You can edit or delete your press release How much a forklift truck battery costs per hour. Making the right financial decisions in uncertain times. here
News-ID: 2188115 • Views: …
More Releases from Philadelphia Scientific

Paving the way for proactive battery performance decisions
Philadelphia Scientific proudly announces the release of the eGO!gateway, a revolutionary cell-based data receiver designed to enhance battery management for industrial fleets. The eGO!gateway transmits real time data from the eGO! battery monitoring system directly to the online portal, empowering fleet managers with critical insights and alerts that can help prevent battery damage, extend battery life, and reduce downtime.
The eGO!gateway's advanced data capabilities make it possible to monitor a battery's…

The road to Net Zero
Philadelphia Scientific's journey to reduce environmental impact at Manufacturing UK Headquarters
Manchester, July 10, 2023 - Philadelphia Scientific, a leading global innovator in stored energy technologies, is continuing the road to reduce the carbon footprint of the UK Headquarters in Bolton in Greater Manchester. Duncan Jones, Managing Director states "All companies need to do their part to reduce their impact. The next stage of our journey is to…
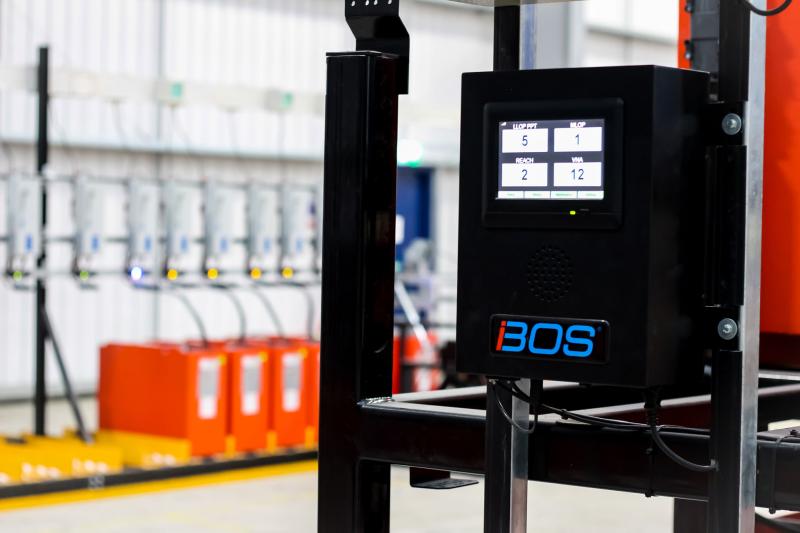
Maximize your battery room's performance with the latest iBOS Battery Management …
Philadelphia Scientific, the world's leading battery room data expert, is set to revolutionize battery room and fleet performance with the launch the latest evolution of its iBOS system, Battery Manager.
Visitors to this year's ProMat exhibition, which takes place March 20-23, at McCormick Place in Chicago, will be the first to witness the new module and Philadelphia Scientific is offering those attending the event the chance to get an up-close look…
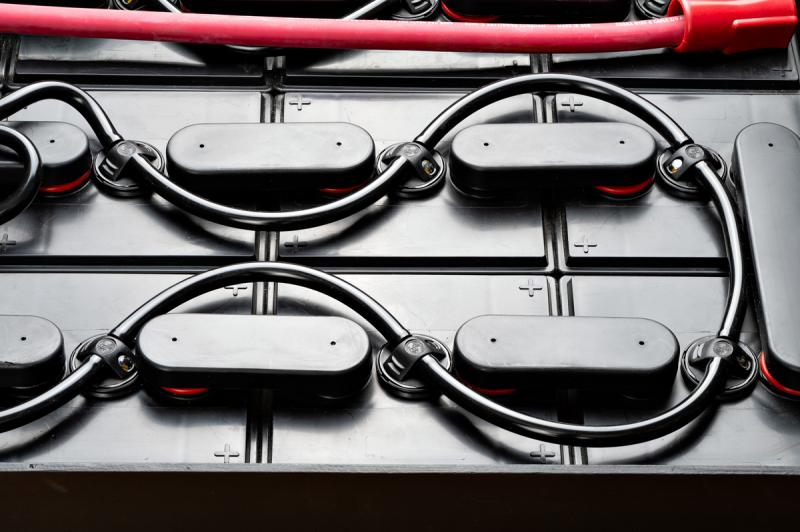
Making the Stealth Barbed Watering System even more cost effective
MONTGOMMERYVILLE, PA, January 12th 2021: Philadelphia Scientific announces a huge improvement to the Stealth Barbed Watering System.
As the most reliable and lowest profile float-based battery watering system available anywhere on the market today, you’d think that the stealth barbed watering system couldn’t get any better, right? Well, our expanding research and development team has brought forward improvements to the design of the valve and the system, making it, even more,…
More Releases for Fully
Fully Rugged Tablets Market
Fully Rugged Tablets Market Overview
Fully rugged tablets are engineered from the inside-out to work in extreme temperatures and other harsh conditions. They are designed to resist drops, shocks and vibrations while maintaining strength to be dust- and waterproof. A tablet has internally a solid state hard drive and no moving parts.
This report provides a deep insight into the global Fully Rugged Tablets market covering all its essential aspects. This ranges…
Fully-Refined Paraffin Wax Market
Fully-Refined Paraffin Wax Market
The global Fully-Refined Paraffin Wax market was valued at US$ million in 2022 and is anticipated to reach US$ million by 2029, witnessing a CAGR of % during the forecast period 2023-2029. The influence of COVID-19 and the Russia-Ukraine War were considered while estimating market sizes.
North American market for Fully-Refined Paraffin Wax is estimated to increase from $ million in 2023 to reach $ million by 2029,…
Fully automatic deep hole drilling
TBT loading system allows unmanned shifts
Along with other precision machined components, GLUMANN Maschinenbau in Chemnitz, Germany specialises in producing long rotating shaft type parts. Deep Hole Drilling plays an important role the production of these items and so in order to keep up with the growing volume demands from an engineering customer, the contract manufacturer (GLUMANN) decided to equip their new Deep Hole Drilling Machine from TBT with a fully…
Fully Automatic External Defibrillator Market
https://www.qandqmarketresearch.com/reports/7228183/fully-automatic-external-defibrillator-market-79
The global Fully Automatic External Defibrillator market is valued at xx million US$ in 2017 and will reach xx million US$ by the end of 2025, growing at a CAGR of xx% during 20182025. The objectives of this study are to define, segment, and project the size of the Fully Automatic External Defibrillator market based on company, product type, end user and key regions.
This report studies the global market size…
Detectamet Fully Detectable Pen Refill
Refilling your Detectamet pen housing is cost effective, kinder on the environment and now safer than ever. Through significant innovation and development, Detectamet are proud to introduce the latest evolution in refills, further minimising the risk of foreign body contamination.
Fully detectable casing & tip
EU & FDA Compliant – Food contact safe.
Cost effective and kinder to the environment.
Blue & black standard inks available with red & green to follow.
Will replace…
Fully Automated Luminaire Testing Procedures
Delphin Test & Measurement Systems for Test Automation
Every day we depend on luminaire products for indoor lighting, whether at work or at home. As with all electro-technical devices, consumer safety is particularly important. Even the latest LED technology requires high-level testing for safety and reliability. For this reason, manufacturers put their newly-developed lamps through a multitude of tests before bringing them to market.
Especially important here are the thermal tests…