Press release
New Ultem* Composites, Foam and Fiber from SABIC Innovative Plastics. Redefine Extreme Performance for Major Customer Growth Opportunities
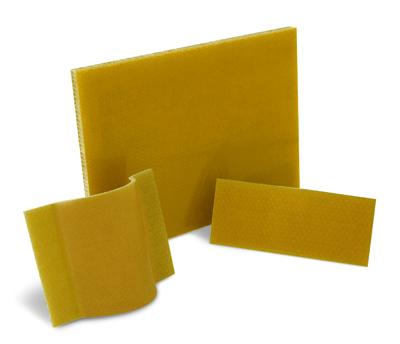
Tubus Bauer Honeycomb for Aircraft Interiors and Exteriors Made with SABIC Innovative Plastics’ Ultem* Composites
Target markets and applications for the new Ultem technologies include flame retardant fabrics, ultra-lightweight aircraft interiors, state-of-the art radomes and communications equipment, and other high-end products where outstanding levels of performance are required.
“These new Ultem forms are unique, ultra-tough, super-performance materials designed to meet the important and ever-changing needs of our customers,” said Kim Choate, global product director for Ultem Resins, SABIC Innovative Plastics. “They offer virtually unmatched performance and value, and illustrate how we are reengineering our premier technologies to give our customers new game-changing solutions that enable a wide range of new business opportunities. It’s an incredibly exciting time in the history of polymer science – for us and our customers.”
Ultem Composites Reduce Weight and Cost
Composites are increasingly replacing metal to achieve weight reduction without sacrificing performance. And more rigorous demands are driving the need for higher temperature and impact performance, particularly in aerospace, electronics and ballistics applications. In aircraft manufacturing, for example, reinforced thermoplastic composites provide a more affordable, simpler and better-performing alternative to metal and thermosets.
By attaching fabric made with Ultem fiber and other materials to an Ultem foam or honeycomb core, unique composites can be created for the design flexibility, low-cost manufacturing, and long-term performance needed to address specific application requirements. For example, TenCate Advanced Composites – a leading manufacturer of advanced fiber reinforced composites for semi-structural and interior aircraft applications – has developed CETEX composite skins based on Ultem composites and woven glass (or carbon) fiber.
For TenCate’s CETEX System 3 composites, the CETEX skins are attached to the tubular honeycomb core – provided by Tubus Bauer – and can be thermoformed and cut into shapes for structural aircraft exterior and interior components. Tubus Bauer is a German manufacturer of semi-structural and interior aircraft applications.
Ultem composite-based materials also provide exceptional flame-smoke-toxicity (FST) performance, low-moisture uptake, thermoformability, and strength retention enabling the composite systems to deliver light-weight performance to eliminate the use of aluminum and thermosets that require long cure cycles. Their inherent low moisture uptake eliminates the need for edge filling and sealing required for many other thermoplastic composite systems.
Ultem Fibers Offer Great Aesthetics with Enhanced Safety
Textiles for aviation and other transportation interiors must meet extremely stringent and toughening safety requirements, including the highest level of FST performance. Now, with Ultem resin-based fibers, manufacturers of textiles and nonwovens can leverage a familiar and proven material (Ultem resin) in a wide range of applications from carpet to fabrics for seating and vertical wall coverings.
In addition to transportation applications, Ultem fiber meets the safety and performance requirements for home furnishings, including mattresses, specialty high-temperature filtration media, and protective clothing for military, emergency response and sports applications. On display in the SABIC booth is a fire suit with an outer shell made of 95 percent Ultem fiber, and an aircraft tapestry also made from this material.
Ultem fiber delivers inherent FST performance without the use of halogens or other flame retardant additives, as well as resistance to extremely high temperatures, chemicals and ultraviolet (UV) light. In addition, the material brings a unique capability to the high-performance fiber market in that it can be dyed using a typical polyester dying process to produce a vast array of colors. Using melt spinning, the material can be produced as monofilaments, multifilaments or staple fibers.
Ultem Foam Combines Strength and Extreme Light Weight
To reduce fuel costs, aircraft manufacturers continue to look for potential weight savings through material replacement in interior and exterior components. The use of Ultem foam can deliver impressive weight savings, coupled with the hallmark, best-in-class FST and high-temperature performance of Ultem resin. Ultem foam is up to 20-times lighter than Ultem resin. This thermoformable, rigid foam with a uniform cell structure is ideal as the structural core in multi-layer systems. Ultem foam meets Ohio State University (OSU) performance levels below 50/50, and offers low moisture absorption, excellent energy absorption and low dielectric loss. It is also transparent to radar.
The Ultem foam product family includes grades with three different densities: 60 kg/m3 (3.8 lb/ft3); 80 kg/m3 (5lb/ft3); and 110 kg/m3 (6.9 lb/ft3). All three grades are manufactured as foam boards by SABIC Innovative Plastics. The boards are suitable for a number of composite manufacturing processes including machining, vacuum bagging, compression molding, and thermoforming.
Ultem foam is compatible with metals and thermoset laminate materials, potentially eliminating adhesives and other secondary operations that are common to the aircraft industry.
Applications include aircraft radomes and interior components such as galleys and dado panels.
For additional information on SABIC Innovative Plastics’ new Ultem technologies, please go to www.sabic-ip.com.
About SABIC Innovative Plastics
SABIC Innovative Plastics is a leading, global supplier of engineering thermoplastics with a 75-year history of breakthrough solutions that solve its customers’ most pressing challenges. Today, SABIC Innovative Plastics is a multi-billion-dollar company with operations in more than 25 countries and over 9,500 employees worldwide. The company continues to lead the plastics industry with customer collaboration and continued investments in new polymer technologies, global application development, process technologies, and environmentally responsible solutions that serve diverse markets such as automotive, electronics, building & construction, transportation, and healthcare. The company’s extensive product portfolio includes thermoplastic resins, coatings, specialty compounds, film, and sheet. SABIC Innovative Plastics (www.sabic-ip.com) is a wholly owned subsidiary of Saudi Basic Industries Corporation (SABIC), one of the world’s top five petrochemicals manufacturers.
# # #
* Trademarks of SABIC Innovative Plastics IP BV.
Kevin Noels
Marketing Solutions, Bergen op Zoom,
The Netherlands
Tel: +31 164 317 011
E-Mail: knoels@marketingsolutions.be
This release was published on openPR.
Permanent link to this press release:
Copy
Please set a link in the press area of your homepage to this press release on openPR. openPR disclaims liability for any content contained in this release.
You can edit or delete your press release New Ultem* Composites, Foam and Fiber from SABIC Innovative Plastics. Redefine Extreme Performance for Major Customer Growth Opportunities here
News-ID: 86688 • Views: …
More Releases from SABIC Innovative Plastics
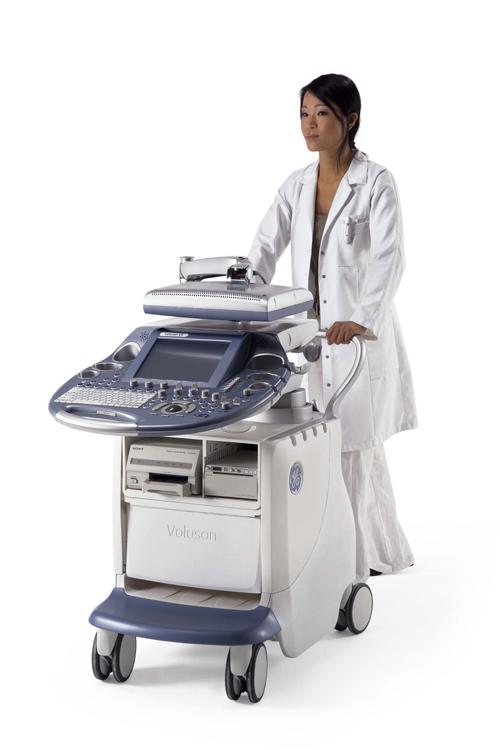
SABIC Launches Portfolio of Antimicrobial Compounds at MD&M West to Help Custome …
According to a 2011 report by the World Health Organization, in 2002 in the United States alone approximately 99,000 deaths were linked to healthcare associated infections (HCAIs).1 Here at MD&M West (booth #1701), SABIC’s Innovative Plastics business today introduced powerful new tools to help medical device manufacturers reduce HCAIs among patients and clinicians. SABIC’s nine new antimicrobial compounds featuring silver technology have been tested for log reduction values – the…
SABIC’s 3D-Formed LEXAN™ Sheet Increases Visibility, Safety, Comfort and Per …
Operators of logging equipment require exceptional visibility and protection against debris or large objects that may enter their cabin and cause serious injury in forest environments, such as tree limbs and other machinery parts. So when Rottne Industry AB needed a high-performance glazing material for the windshields and windows of its harvesters and forwarders, it turned to
SABIC’s Innovative Plastics business for support. Working with SABIC and its distributer, Vink…
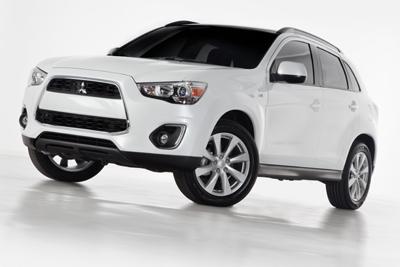
Mitsubishi Motors Corporation Selects SABIC NORYL GTX™ Resin for 2013 Outlande …
SABIC’s Innovative Plastics business today announced that Mitsubishi Motors Corporation (MMC) has chosen SABIC’s next-generation NORYL GTX™ 989 resin for the front fenders of its 2013 Outlander Sport crossover. The vehicle’s fenders are the first to be produced using 2-cavity injection molding with NORYL GTX resin, allowing MMC to cut cycle times in half and reduce tooling costs. Other major benefits of the SABIC material include weight savings vs. steel…
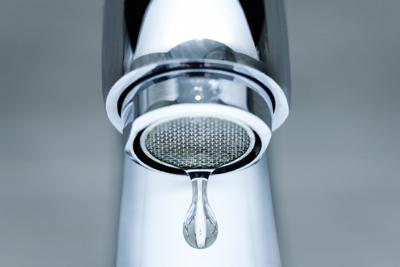
SABIC Makes a Splash at Fakuma with New NORYL™ Resin, Meeting Tightening Globa …
Here at the Fakuma trade fair, booth #B5-5506, SABIC’s Innovative Plastics business today announced a new NORYL™ resin that not only complies with current European and global sustainability regulations governing materials used in potable water systems, but also with new, tougher regulations slated to go into effect in 2016. Developed at SABIC’s Fluid Engineering Center of Excellence in the Netherlands, NORYL FE1630PW resin is a 30-percent glass-reinforced polyphenylene ether (PPE)…
More Releases for Ultem
SABIC’s new Ultem™ film UTF120 offers solutions for professional-grade diele …
Capacitors are ubiquitous in electrical products, and have many uses in electronic applications and electrical systems. To address the growing need for lightweight, compact, high energy density capacitors able to store large amounts of electrical energy for long periods of time without significant current leakage and loss of charge even at high temperatures, SABIC is launching a new polyetherimide (PEI) film - ULTEM™ film UTF120.
ULTEM™ film UTF120 is a high…
SABIC’s Tough, Lightweight Ultem* Resin Solution Replaces Metal in Intermestic …
BERGEN OP ZOOM, The Netherlands – March 21, 2012 – SABIC’s Innovative Plastics business’ world-class expertise and technology were further evidenced today with the company’s announcement that Intermestic Inc., a specialty retailer of eyewear and accessories, has chosen tough, lightweight Ultem* polyetherimide (PEI) resin for the frames of its new line of Zoff SMART eyeglasses. The tailored, aerospace-grade Ultem resin material solution helps meet Japanese consumer demands for fresh, new…
SABIC Innovative Plastics’ Tough Ultem* HU1004 Resin Validated as Top Material …
BERGEN OP ZOOM, The Netherlands – July 6, 2011 – SABIC Innovative Plastics today announced third-party test results that validate the multiple sterilization capabilities of its remarkably tough Ultem* HU1004 polyetherimide (PEI) resin. This high-performance resin – previously utilized for other techniques and now tested for use with the STERRAD® NX® low-temperature hydrogen peroxide gas plasma sterilization – gives healthcare providers the flexibility to choose any major method for sterilizing…
SABIC Innovative Plastics Wins Aviation Week Suppliers’ Innovation Challenge A …
BERGEN OP ZOOM, The Netherlands – January 12, 2011 – SABIC Innovative Plastics has won an award in Aviation Week’s first annual Suppliers’ Innovation Challenge competition, recognizing new and recent technology developments by tiered suppliers in the aerospace and defense industry. The company’s lightweight, rigid Ultem* polyetherimide (PEI) foam, used as the structural core in multi-layer systems for aviation interior components, won the Composites category. According to Aviation Week, winners…
SABIC Innovative Plastics’ Ultem* Resin Composite Gives Crane Stellar Performa …
BERGEN OP ZOOM, The Netherlands – September 21, 2010 — At the Aircraft Interiors Expo Americas, Sept. 14-16, 2010, SABIC Innovative Plastics have launched a new breakthrough technology for semi-structural aircraft interior parts featuring its high-flying Ultem* polyetherimide (PEI) resin. New Ultem composite aerospace board (CAB) sheets, co-developed and manufactured with Crane & Co., the global leader in specialty paper, provide a superior alternative to thermoset aramid fiber-reinforced honeycomb composites.…
ABIC Innovative Plastics' Ultem for New Composite Aerospace Board
BERGEN OP ZOOM, The Netherlands – September 21, 2010 — At the Aircraft Interiors Expo Americas, Sept. 14-16, 2010, SABIC Innovative Plastics have launched a new breakthrough technology for semi-structural aircraft interior parts featuring its high-flying Ultem* polyetherimide (PEI) resin. New Ultem composite aerospace board (CAB) sheets, co-developed and manufactured with Crane & Co., the global leader in specialty paper, provide a superior alternative to thermoset aramid fiber-reinforced honeycomb composites.…