Press release
New landmark with panoramic view

During the Kosovo war, the television tower on the Avala mountain near Belgrade was destroyed. PERI know-how and products are supporting the reconstruction of this famous landmark. (Photo: PERI GmbH)
The base of the tower has been designed as a gigantic tripod. The tower shaft is positioned about nine metres over the top ground surface in the middle of these inclined base supports. In its final state, an approx. 10-metre high all-round upstand beam carries the loads of this bottom shaft area while during the building phase, however, large loads had to be transferred via shoring into the ground. Starting from around the 100-metre level on the tower, a number of cantilevered platforms are arranged and concrete construction actually ends at a height of 135 metres. The antenna positioned on the top measures almost 70 metres. In spite of the height and complicated architecture of the tower, the formwork and scaffolding solution developed for this project is based mainly on system equipment taken from the extensive PERI product range. The combination of delicate structure and high loads required however specially adjusting to the building´s geometry. During the planning, for example, vertically-positioned construction joints had to be taken into consideration whereby the setting of stop ends in the area of the inclined walls, due to the use of self-compacting concrete, presented an additional degree of difficulty.
A huge base - optimally combined modular system
At the same time in each case, the three 30° inclined base legs were concreted in four cycles. On the reverse-angled side of the base supports, VARIO elements were continuously extended with the loads being transferred via raised formwork units made of VARIOKIT elements into sections that had been previously completed. The VARIO formwork on the tripod´s opposite side was supported with a construction which comprised of SRU steel walers, SLS heavy-duty spindles and RCS climbing rails. The formwork positioned to the side of the supports could be safely operated from PERI UP Rosett platforms and the elevation of the working platforms took place continuously in step with construction progress. A crane moved the large-sized formwork units in each case to the next concreting section. The flexible construction grid of the PERI UP modular scaffold allowed the load-optimized integration both in the inclined base supports as well as in the interlaced tubular steel construction which served as temporary bracing for the tripod.
The almost eleven metre high subsequent section covered the massive area from the underside of the shaft up to the top edge of the crown-shaped upstand beam. Up to the monolithic connection of the tripod and crown, the enormous loads of almost 330 tonnes were to be carried via the shoring under the shaft safely into the ground. For this purpose, different load towers were combined in order to safely accommodate the, in part, extremely high point loads. The PERI UP modular scaffold as well as MULTIPROP props which were connected together with MRK frames to form towers were used.
Mobile climbing devices – a particularly cost-effective solution
The accurate realization of the shaft above the massive upstand beam was done using the PERI RCS rail climbing system and the VARIO girder wall formwork system. In the lower area with changing shaft cross-section, a crane lifted the elements to the next concreting cycle in each case. For constructing the subsequent triangular standard cross-sections, the contractor used the hydraulically-driven RCS climbing device. In the process, the scaffold unit was connected during the entire climbing procedure to the building itself by means of climbing shoes so that formworking could always be safely carried out. The use of the mobile self-climbing devices and hydraulic pumps for climbing on the standard cross-sections minimized the costs for the self-climbing technology and thus represented a particularly cost-effective method of concrete construction.
An additional PERI solution for the Avala Tower was the planning, manufacture and delivery of special suspension units for the shoring and working scaffold on the shaft. As the walls with the smallest thickness of only 15 centimetres did not have sufficient bearing capacity for the load transfer, PERI engineers developed special fastening elements.
Brace frames suspended on the tower shaft
Precast elements formed the inclined external walls of the sub-construction both for the first platform at around a height of 102 metres as well as one positioned about twelve metres higher up. The supporting structure of the required working platforms was formed by horizontal PERI SB brace frames - here, too, special suspension units ensured the transfer of loads into the shaft. The inclined positioned precast walls were used as assembly support on the VARIOKIT units - consisting of SRU steel walers and SLS heavy-duty spindles - which were lying horizontally on the brace frames. After completion of the concrete construction, these working platforms were removed with the help of cable winches and transported to the ground. After shifting, the precast walls themselves were connected and braced via internal cast-in-place beams.
Currently, the slabs of a further five platforms are being constructed. Depending on the imposed load and support possibility, the levels are built with either PERI customised tables or MULTIFLEX slab formwork placed on PERI UP Rosett scaffold or PEP props. The PERI UP scaffolding will once again prove its versatility after completion of the structural work: when all platforms have been constructed, a suspended scaffold is assembled from the system modules which allows the installation of a glass facade on the viewing platform.
Crane reaches its limit – PERI UP goes higher
An almost 70-metre long antenna forms the tower pinnacle which, after completion of the concrete construction, is placed on top of the shaft at a height of 136.91 metres. Due to static reasons, the crane cannot be extended up to the tip of the antenna, and can only be partly used for the assembly. Using a special PERI UP Rosett scaffold construction, the individual parts of the antenna can also be safely installed beyond this point. However, fitting the final part is not possible even using this variant, and this will be undertaken by a helicopter.
Contractors:
Ratko Mitrovic Dedinje d.o.o., Belgrade, Serbia
Field Service:
PERI Belgrade, Serbia;
PERI Frankfurt (Country Group Support for Eastern Europe) and
PERI Weissenhorn, Germany
PERI Systems In Use
- MULTIFLEX Girder Slab Formwork
- MULTIPROP System
- PERI UP Rosett
- RCS Rail Climbing System
- SB Brace Frame
- Table Modules
- VARIO GT 24 Girder Wall Formwork
- VARIOKIT
PERI was founded in 1969 and is today one of the leading providers of formwork and scaffolding systems. Along with the headquarters in Weißenhorn, Germany, the company has 46 international subsidiaries and 100 stock yards around the world. The company has over 5400 employees of which 850 are engineers. 2008 revenues was 1,220 million Euros.
PERI GmbH
Editorial Office
P.O. Box 1264
89259 Weissenhorn
Germany
Phone: +49 (0) 7309.950-1180
Fax: +49 (0) 7309.951-1180
E-Mail: redaktion@peri.de
Web: www.peri.de
Re-prints are free of charge quoting "Source: PERI GmbH". Please send a copy to the PERI Editorial Office.
This release was published on openPR.
Permanent link to this press release:
Copy
Please set a link in the press area of your homepage to this press release on openPR. openPR disclaims liability for any content contained in this release.
You can edit or delete your press release New landmark with panoramic view here
News-ID: 75041 • Views: …
More Releases from PERI GmbH - Formwork, Scaffolding, Engineering
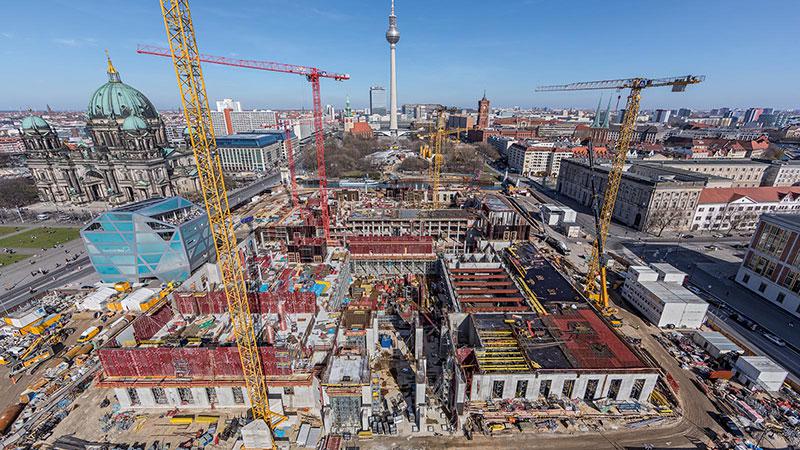
Formwork and scaffolding from one source for Berlin´s City Palace
Sep 1, 2015 - "Humboldt Forum" City Palace, Berlin
For the reconstruction of Berlin´s City Palace, PERI supplied cost-effective formwork and scaffolding solutions from one source. In addition to providing large quantities of wall, column and slab formwork with fast shuttering and moving times as well as flexibly used scaffolding materials, the on-site support provided by the PERI engineers ensured that all requirements could be fulfilled along with maintaining the tight…
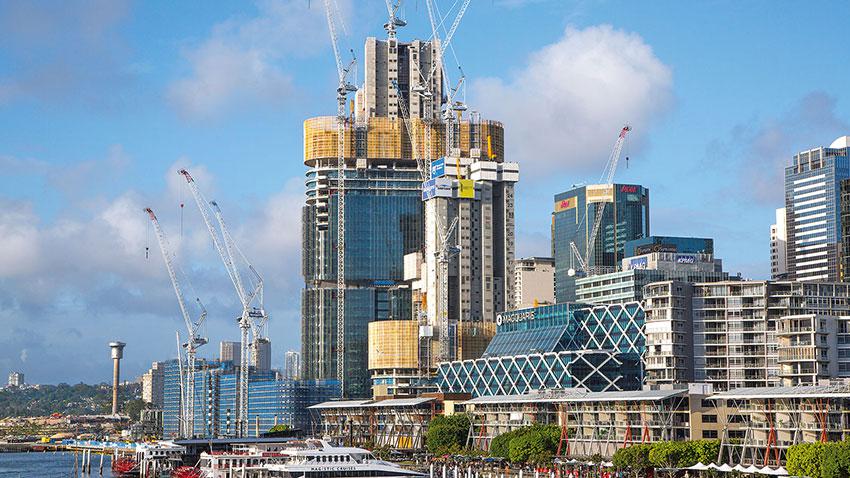
Construction time optimisation through comprehensive working safety and crane-in …
Aug 3, 2015 - International Towers Sydney ITS, Barangaroo South, Sydney, Australia
The new LPS climbing protection panel from PERI provides comprehensive working safety and saves valuable crane time thanks to the mobile climbing hydraulics. This has accelerated construction progress on the International Towers Sydney complex on Australia's east coast.
With the ambitious Barangaroo Redevelopment Project, Sydney's city centre is being redefined in a westward direction. On the 22-hectare former container port…
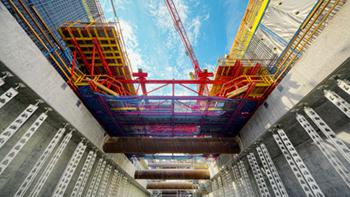
System-based project solution saves time and money
July 1, 2014 - Capitol Hill Station, Seattle, USA
The formwork and scaffolding solution provided for the construction of the new subway station in Seattle was the result of competent engineering and a project-specific construction kit system. In addition to the widest possible use of rentable PERI system components, the optimized construction method in particular ensured significant time and cost savings.
The length of Seattle´s metropolitan railway system (Light Rail) is currently…
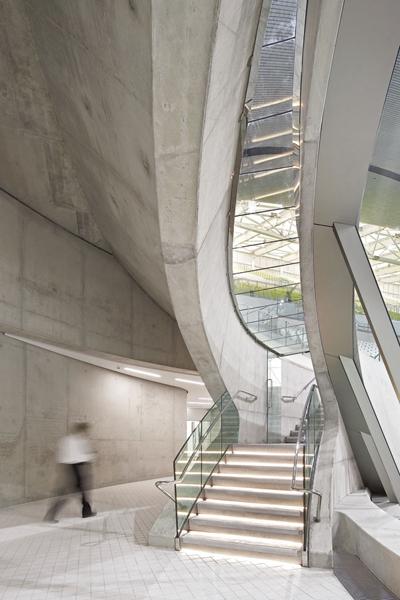
Formwork in every shape and dimension – even faster with the new CNC system
June 16, 2014 - Visions of architects take shape with PERI
Planned, formed, concreted – it is actually hard to believe that this procedure could ever function trouble-free in some cases of present-day abstract concrete structures. In its pursuit of uniqueness, architecture is becoming more and more ambitious. Parallel to this, the requirements of construction companies are likewise increasing. PERI, however, is keeping pace with this trend: with individual formwork solutions,…