Press release
Ultrasonic Flaw Detection Technology for Welded Steel Pipe
Introduction of ultrasonic flaw detection technology for welded steel pipe.1, ultrasonic testing
Ultrasonic testing is one of the non-destructive testing methods, non-destructive testing is not under the premise of damage to the workpiece macroscopical defects or measure the characteristics of various technical methods collectively. Dyed steel pipe conventional non-destructive testing methods are:
Ultrasonic Testing (Radar); Radiographic Testing (abbreviated RT); Magnetic particle testing (abbreviated MT); Penetrant testing Penetrant Testing (abbreviated PT); Eddy Current testing (abbreviated ET);
2, ultrasonic flaw detector
The use of ultrasonic testing methods to detect the instrument called ultrasonic flaw detector. The principle is that when the ultrasonic wave propagates in the tested material, the acoustic characteristics of the material and the change of the internal structure have a certain influence on the propagation of the ultrasonic wave. Through the detection of the degree and condition of the ultrasonic wave, the technique of understanding the material performance and structural change Called ultrasonic testing. Ultrasonic testing methods are usually penetrating, pulse reflection, tandem and other ultrasonic testing is the use of ultrasound can penetrate the depth of metal materials, and from one section into another section, the reflection of the characteristics of the interface edge to check Part of the defect of the method, when the ultrasonic beam from the surface of the parts from the probe to the inside of the metal, encountered defects and parts of the bottom of the surface were reflected waves, the formation of pulse waveform on the screen, according to the pulse waveform to determine the defect location and size.
Non - destructive testing of internal defects of materials using thick - walled steel tubes. Now widely used is to observe the sound pulse in the material reflection of the ultrasonic pulse reflection method, in addition to observation through the material after the incident sound amplitude changes in the penetration method. Commonly used frequency between 0.5 ~ 5MHz.
Commonly used test instrument for the A-type display pulse reflection ultrasonic flaw detector. According to the presence or absence of the reflected signal on the oscilloscope screen, the time interval of the reflected signal and the incident signal, the height of the reflected signal can determine the presence or absence of the reflecting surface, its position and relative size.
Ultrasound in the media when there are a variety of wave propagation, the most commonly used in the test for the longitudinal wave, shear wave, surface wave and plate wave. It can detect the defects such as inclusions, cracks, shrinkage, white spots and delamination in the parts of metal ingot, billet, plate, large forging and shape, which can be used to detect the defects in the pipe. And the surface cracks can be detected on the surface of a simple surface defects; with the plate wave can be detected in the thin plate of the sheet; defect.
Ultrasound is propagated in the material, and the strength is attenuated due to absorption and scattering. Therefore, it is possible to measure the attenuation of the alloy material in a furnace such as a vacuum furnace. It is possible to know the uniformity of the material.
Pulse reflection type ultrasonic method compared with other non-destructive testing methods
The main advantages are:
① penetrating ability, detection depth of up to several meters;
② high sensitivity, can be found with about a few tenths of a diameter of the air gap reflectivity equivalent of the reflector;
③ in determining the internal reflector of the bit direction, size, shape and nature of the more accurate;
④ only from one side of the object to be tested;
⑤ can immediately provide defect test results;
⑥ safe operation, equipment, light.
The main drawbacks are:
① be operated by experienced people with caution;
② rough, irregular shape, small, thin or non-homogeneous material difficult to check.
Hunan Great Steel Pipe Co.,Ltd: http://www.great-pipe.com/
Address: Hunan Steel Industrial Zone,No.9 Xiangfu Road, Yuhua District, Changsha, Hunan, China
Postcode:410116
Tel:0086-731-88678502
Fax:0086-731-88678508
E-mail: info@great-pipe.com
welded steel pipe, spiral welded steel pipe: http://www.great-pipe.com/product.html
Hunan Great Steel Pipe Co.,Ltd is a world-class production and service provider of submerged arc straight seam welded pipe as the first subsidiary of Shinestar Group. Hunan Great Steel Pipe Co.,Ltd pays more attention to in the pipeline engineering research areas as a pioneer of China Petroleum Pipeline & Gas Pipeline Science Research Institute, Such as: the use of oil and gas pipelines, pipe welding technology innovation, high-end plumbing materials research and development, as well as special tools technological innovation pipeline construction, pipeline corrosion protection science and technology research, science and technology research pipeline non-destructive testing, pipeline quality assessment, and research pipeline standards and so on. In the future, we will try to use new technology to create new business value and to contribute to research and product development for the pipeline.
Hunan Steel Industrial Zone,No.9 Xiangfu Road, Yuhua District, Changsha, Hunan, China
This release was published on openPR.
Permanent link to this press release:
Copy
Please set a link in the press area of your homepage to this press release on openPR. openPR disclaims liability for any content contained in this release.
You can edit or delete your press release Ultrasonic Flaw Detection Technology for Welded Steel Pipe here
News-ID: 521727 • Views: …
More Releases from Hunan Great Steel Pipe Co.,Ltd
HUNAN GREAT STEEL PIPE CO., LTD
Quality products as competitiveness of Hunan Great Steel Pipe Co.,Ltd. Our main products include: carbon steel seamless pipe, carbon steel welded pipe, stainless steel pipe, pipe fittings, which is variety types and full range specifications, moreover, strictly in accordance with international standards, like: ISO certification, CE certification. At the same time, we are able to offer value-added steel services, including: hot dip galvanized, anti-corrosion treatment, pipe cutting, or other customized…
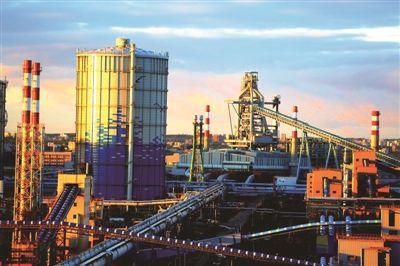
Common Causes of 304 Stainless Steel Pipe Corrosion
1 Chemical corrosion
1.1 Surface contamination: attached to the surface of the oil, dust and acid, alkali, salt and other under certain conditions into the corrosive medium, react chemically with some elements of stainless steel pipe, chemical corrosion and rust.
1.2 Surface scratches: various scratch destruction of the passive film, reduced ability to make stainless steel protection, prone to chemical reaction medium, chemical corrosion and rust.
1.3 Cleaning: Cleaning is not clean after…
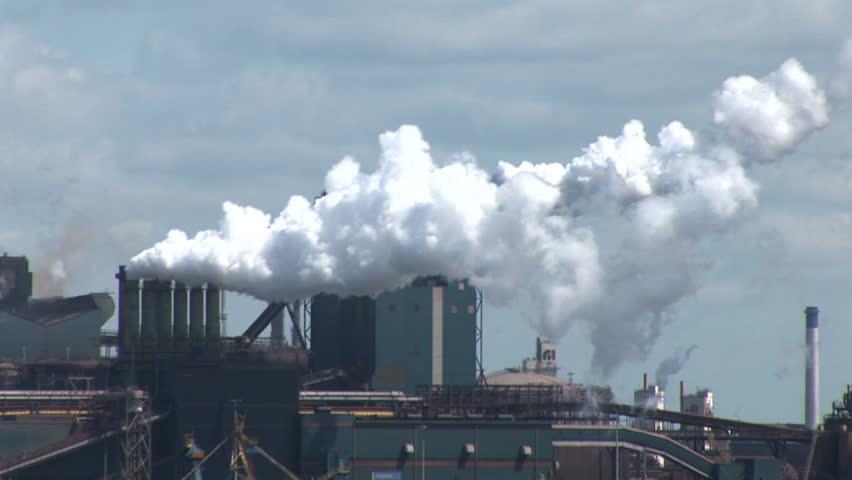
How to Detect High Quality Coating Steel Pipe
Coating steel pipe is now a very high rate of a pipe, we racked our brains, in order to allow you to pick a better coating steel pipe to provide you with a test method.
1.Impact test
In addition to the appropriate room temperature range, but also in accordance with the relevant national standards, the impact of its operation, in order to see the changes in the coating.
2. Visual inspection
This is the…

How to Strengthen the Stability of SSAW Steel Pipe
1) Small and medium-sized steel, wire rod, steel, medium diameter steel pipe, wire and wire rope, etc., can be stored in a well-ventilated shed, but must be under the pad.
2) Some small steel, thin steel, steel, silicon steel, small diameter or thin-walled steel pipe, all kinds of cold-rolled, cold-drawn steel and high prices, easy to corrode the metal products can be stored.
3) Storage of SSAW steel pipe(Spirally Submerged Arc Welded…
More Releases for Ultrasonic
Ultrasonic Cleaning Market Report 2024 - Ultrasonic Cleaning Market Demand And S …
"The Business Research Company recently released a comprehensive report on the Global Ultrasonic Cleaning Market Size and Trends Analysis with Forecast 2024-2033. This latest market research report offers a wealth of valuable insights and data, including global market size, regional shares, and competitor market share. Additionally, it covers current trends, future opportunities, and essential data for success in the industry.
Ready to Dive into Something Exciting? Get Your Free Exclusive Sample…
Ultrasonic Gas Leak Detectors and Ultrasonic Gas Detector Machine Services | SM …
SM INSTRUMENTS provides ultrasonic gas leak detectors and ultrasonic gas detector machine services. They are Korea's leading provider of ultrasonic equipment and services, and their ultrasonic gas leak detectors are some of the most reliable and accurate on the market.
SM Instruments Ultrasonic Gas Leak Detectors
SM Instruments ultrasonic gas leak detectors use ultrasonic technology to detect gas leaks. Ultrasonic waves are sound waves that are above the range of human hearing.…
Ultrasonic Oxygen Sensor Market, Ultrasonic Oxygen Sensor Market Size, Ultrasoni …
Fairfield Market Research offers a complete understanding of the Global Ultrasonic Oxygen Sensor Market in its latest research report. The report includes an unbiased analysis of the market dynamics. The report covers growth prospects, market development potential, product profitability, supply and demand curves and predictions, and government policies. The report has been put together using reliable tools to assess the primary and secondary data. The data is represented in the…
Lithium Battery Ultrasonic Welding Machine Market Booming Worldwide( Forecast Pe …
The global Lithium Battery Ultrasonic Welding Machine market is carefully researched in the report while largely concentrating on top players and their business tactics, geographical expansion, market segments, competitive landscape, manufacturing, and pricing and cost structures. Each section of the research study is specially prepared to explore key aspects of the global Lithium Battery Ultrasonic Welding Machine market. For instance, the market dynamics section digs deep into the drivers, restraints,…
Ultrasonic Water Meter Market Ultrasonic Water Meter Market
The proposed Ultrasonic Water Meter Market report will encompass all the qualitative & quantitative aspects including the market size, market estimates, growth rates & forecasts & hence will give you a holistic view of the market. The study also includes detailed analysis of market drivers, restraints, technological advancements & competitive landscape along with various micro & macro factors influencing the market dynamics.
The Ultrasonic Water Meter Market sample report…
Global Ultrasonic Welder Market 2017 - Rinco, Maxwide Ultrasonic, Kormax System
The report entitled Global Ultrasonic Welder Market 2017 presents key insights into the global Ultrasonic Welder market along with the latest up-to-date industry details and forthcoming Ultrasonic Welder industry trends, which will assist the readers to focus on product specification and end users driving the overall market revenue and profitability.
Report Keynotes:
The main motive of the report on "Global Ultrasonic Welder Market 2017" is to study comprehensive details of the market…