Press release
CRP Technology celebrates 25 years of professional use of Laser Sintering
https://youtu.be/CKWkjHBeZ_IThe plurality may have only discovered Additive Manufacturing in the last decade, but CRP Technology has been familiar with its inner connections since 1996. At that time Roberto Cevolini (owner of Roberto Cevolini & Co. high precision CNC machining avantgarde service with roots in the high end automotive/racing world) decided to analyse the 3D printing processes with a clear idea in mind: be able to resolve in advance customers’ issues and offering them never-seen-before technological solutions.
So, Roberto Cevolini and his son Franco invested in a sinterstation for Selective Laser Sintering; at the time no one company in Italy had one, they were the first. In order to make their engineering contribution stronger, they founded CRP Technology, a subsidiary of Roberto Cevolini & C.
CRP Technology included a R&D department for material development.
Franco Cevolini, VP and CTO at CRP Technology, states: “Purchasing an industrial 3D printer wasn’t enough for us, we wanted to make a major and stronger contribution: we decided to create a family of 3D printing materials suitable to manufacture high performing parts and applications, which could meet the needs of our F1 customers.”
At the end of ‘90s it become evident that Selective Laser Sintering was an excellent technology with limitations imposed by “process-able” materials limited in scope to use for traditional non-functional prototyping. CRP Technology’s vocation for bold technological innovations developed something out of the ordinary: the Windform® range of composite materials for professional 3D printing.
In 1999 Windform®, the name born out of its primary purpose as a wind-tunnel material, represented the first hybrid polymer-metal composite (filled with Aluminium) to be used for functional prototyping. It proved excellent to satisfy almost all needs for wind-tunnel modelling and allowed aerodynamicists to have a new powerful tool available in order to make functional, fluid-aerodynamic, fitting and assembling tests. Moreover it proved excellent for direct “in-the racing-car” applications.
With Windform® officially born and launched, the way to transforming rapid prototyping into rapid manufacturing was paved.
Important progress has been made in the sector of additive technologies with the development of Windform® materials, such as outgas tests for use in space, patch testing for the medical sector, fashion and design and testing of non-conductivity, expanding the use of these in all areas in which a highly durable material is required, offering the opportunity of being processed with high precision CNC machining.
So far the Windform® family of comprises 12 materials distributed in two lines, adequate to fulfill the needs of the most advanced and demanding sectors, including aerospace and defense, avio, robotics, medical, motorsports and automotive.
Veronica Negrelli
Press Office Manager CRP Technology
via Cesare Della Chiesa, 140/C
41126 Modena
ITALY
CRP Technology (Modena, Italy) develops, manufactures and sells to OEMs its proprietary high performance composite materials Windform® for professional 3D Printing. It is also distinguished by its know-how in Powder Bed Fusion process. It offers part production for short- and low-run production, and prototyping services with Windform®. Its specific application fields including but are not limited to: automotive and motorsports, design, aerospace, UAVs, marine, entertainment, defense, and packaging.
This release was published on openPR.
Permanent link to this press release:
Copy
Please set a link in the press area of your homepage to this press release on openPR. openPR disclaims liability for any content contained in this release.
You can edit or delete your press release CRP Technology celebrates 25 years of professional use of Laser Sintering here
News-ID: 2341916 • Views: …
More Releases from CRP Technology

CRP Technology Introduces Vapor Smoothing to Boost Surface Quality and Performan …
The Italy-based company specializing in 3D printing services has expanded its suite of production and post-processing capabilities, offering clients a fully integrated process from additive production to final inspection. Vapor smoothing can be applied to stand-alone Windform parts or following manual finishing, further enhancing the already high-performance characteristics of Windform materials.
Modena, Italy, 25 November 2024 - CRP Technology, a leader in advanced 3D printing services, has introduced vapor smoothing into…
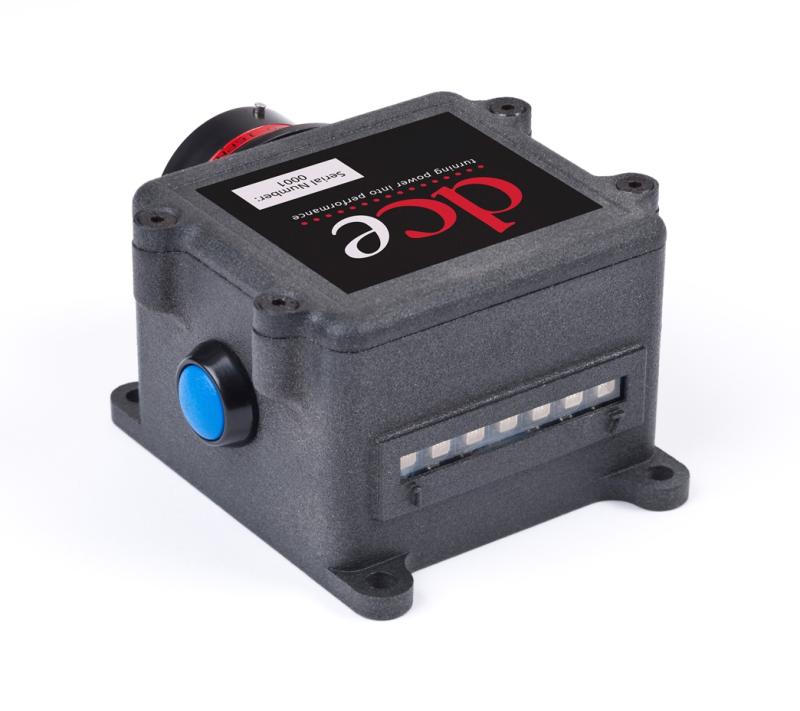
Excellent Electrical Insulation Performance for Windform Composites
3D printing service bureau CRP Technology's Glass fiber reinforced Windform thermoplastic composites were subjected to dielectric constant and dielectric strength tests, and the results were excellent, exhibiting a dielectric constant of approximately 4 and withstanding peak voltages of at least 2.5 kV/mm.
3D printing service bureau CRP Technology is pleased to inform that their Glass fiber reinforced Windform thermoplastic composites for Selective Laser Sintering, have demonstrated outstanding electrical insulation performance as…
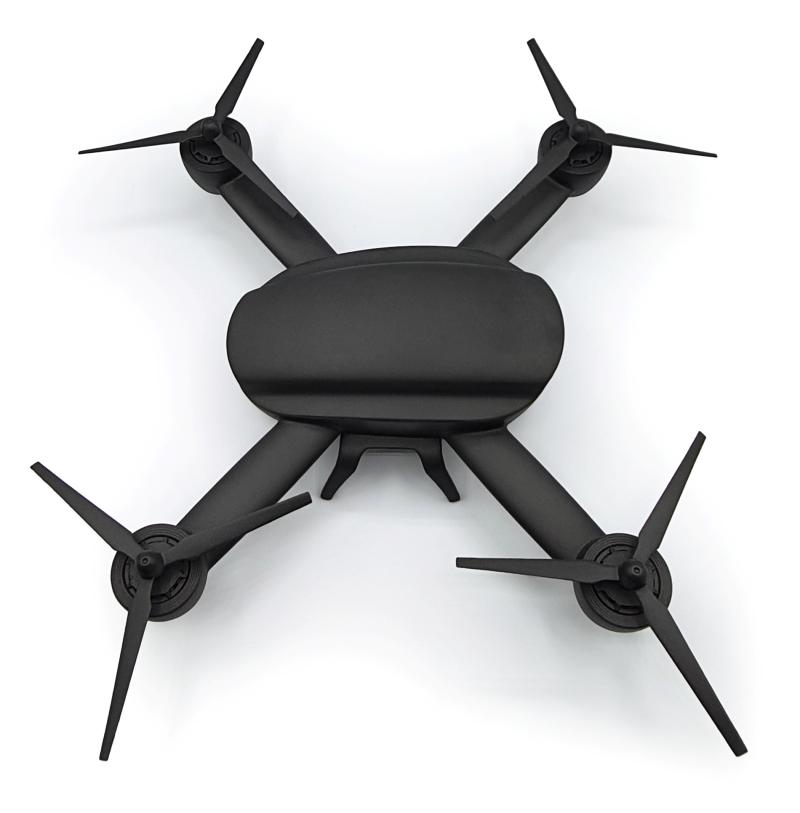
3D Printing Service Bureau CRP Technology Launches Windform SL, the Top-of-the-L …
CRP Technology, a pioneering company in the 3D printing industry and a leading 3D printing service bureau, introduces Windform SL, the twelfth material in the Windform TOP-LINE series, setting new standards in additive manufacturing. Windform SL, a polyamide-based composite reinforced with Carbon fibers, combines exceptional lightweight characteristics with a low density of 0.87 g/cc, making it an ultra-light and rigid material.
In the rapidly evolving field of Additive Manufacturing, the globally…
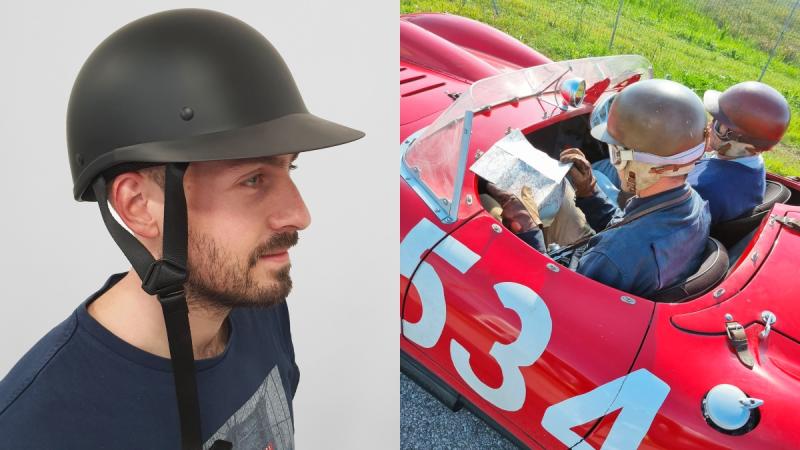
CRP Technology's Role in Industrial 3D Printing for Michael Mann's Film, "Ferrar …
Nestled in the soul of Modena, a city echoing with the thunderous symphony of engines and steeped in the storied tradition of automotive prowess, the eclectic and innovative filmmaker Michael Mann assumed the directorial helm to breathe life into the enthralling saga of Enzo Ferrari, the mastermind behind Ferrari cars.
Drawing inspiration from Brock Yates' seminal 1991 biography, "Enzo Ferrari: The Man and the Machine", Mann's new cinematic masterpiece, "Ferrari"…
More Releases for Windform®
Excellent Electrical Insulation Performance for Windform Composites
3D printing service bureau CRP Technology's Glass fiber reinforced Windform thermoplastic composites were subjected to dielectric constant and dielectric strength tests, and the results were excellent, exhibiting a dielectric constant of approximately 4 and withstanding peak voltages of at least 2.5 kV/mm.
3D printing service bureau CRP Technology is pleased to inform that their Glass fiber reinforced Windform thermoplastic composites for Selective Laser Sintering, have demonstrated outstanding electrical insulation performance as…
Windform RS and Windform LX 3.0 officially approved for space flight
Carbon fiber reinforced composite Windform RS and Glass fiber reinforced composite Windform LX 3.0 from CRP Technology's Windform TOP-LINE, passed ESA standard screening outgassing tests in accordance with ESA-TEC-PR-002015 (based on ECSS-Q-ST-70-02C): they are officially approved for the construction of applications to launch into Space.
Franco Cevolini, CEO and Technical Director of CRP Technology, says: "Passing the outgassing tests is a crucial factor for those who supply materials to the…
Windform® RS, the outstanding composite material with amazing mechanical proper …
CRP Technology launches a new polyamide-based Carbon fiber filled composite for production-grade PBF 3D printing: the top-of-the-range Windform® RS. Engineer Franco Cevolini, CEO and CTO, CRP Technology: "In the Additive Manufacturing world Windform® RS is unparalleled. We created a material that combines high tensile strength with high elongation at break and low density: Windform® RS is unique of its kind"
CRP Technology, a leading 3D printing company, announces the…
Successful use of Carbon-composite Windform® XT 2.0 and Laser Sintering in the …
US-based CRP USA manufactured three engineering models for Mini-Cubes. It is the first time that entire PocketQube functional prototypes flight-ready are manufactured using a Carbon-reinforced composite material - Windform® XT 2.0 - and Laser Sintering process
Recently Joseph Latrell, CEO of Mini-Cubes, LLC and his team started a project based on the engineering of a new 1P PocketQube flight-ready, named Discovery. The aim of the project is the creation of a…
CRP Technology launches Windform® P2, thermoplastic glass fiber filled material …
CRP Technology, a leading company in the creation of prototypes and final applications in professional 3D printing, launches Windform® P2 material.
Windform® P2 is a glass fiber reinforced thermoplastic polyamide material with excellent mechanical properties for High Speed Sintering process.
Engineer Franco Cevolini, CRP Technology CTO and VP, states: “Windform® P2 is the second polymer from P-LINE, the new Windform® range of materials for high speed production-grade 3D printing, introduced on the…
Isotropic material for 3D printing Windform® P1 shortlisted for TCT Awards 2019
Italian-based CRP Technology, 3D printing leader for the most advanced industrial sectors, gained new international success.
CRP Technology’s Windform® P1 has been shortlisted for the Materials Award – Polymers at the TCT Awards 2019, following some strong competition and an intensive review by TCT Expert Advisory board.
Windform® P1 is the inaugural new-born isotropic PA (polyamide) from the P-LINE family of materials for High speed production-grade 3d printing.
Franco Cevolini, VP and…