Press release
The maintenance assessment: a stepping stone for improvement
Maintenance assessments (sometimes called “audit” although we prefer the term “assessment”) represent a growing part of our business in China. This article will explore the principles, practice and benefits of such assessments.1. Why an assessment?
Experience conducting maintenance assessments for over 30 years worldwide has shown that poor maintenance can drag down plant profits by up to 40%. According to benchmarks, even the world’s very best plants can still deliver up to 11% more in bottom line profits.
Yet, maintenance improvement is often not about cutting budgets, but about improving effectiveness, reducing losses and preventing risks: indeed, our studies show that you can save more than 10 times more money by acting on indirect costs and losses, i.e. the impact of maintenance on the business. But: where and how? This is the question we can answer.
The Chinese market, in which our team has been active for over 20 years, presents its specificities. Its modern-time industrial development has long prioritized new construction, capacity expansion, rather than maintenance: the entire supply chain, including design institutes, contractors, equipment suppliers, service companies, the education system etc. was aligned accordingly. In the past few years, official studies have shown that most industrial accidents, safety and environmental problems were caused by technical management mistakes at either working level or top management. Similarly, authorities have identified higher lifecycle cost, in particular due to fast aging (early replacement) or equipment, in public facilities. This has prompted the Chinese government to increase regulatory pressure, a phenomenon that all companies operating in China have observed, and to generally promote a more risk-based approach to technical management.
Based on a unique experience combining both industrial maintenance expertise and consulting project in the past 20 years in China, Siveco China has developed a proven maintenance assessment methodology: an approach that has delivered results for many facility owners and operators in China.
The assessments are designed to answer such questions as:
- Where and what are you risks, losses and excess costs?
- How to get more ROI from your existing systems without new investment?
- Identify maintenance improvements and how to deliver them!
The assessment is designed to address the company’s strategy and top concerns, in line with ISO 55000 Asset Management standard, while adopting a very open wide-angle approach to ensure unknown issues can be identifies.
2. The Siveco China assessment
Principles
Our assessments are always tailor-made to each customer’s specific case. We can however distinguish three types of assessments:
- Maintenance organization assessment – focus on the organization and its processes
- Maintenance system assessment – focus on your systems and their utilization
- Condition assessment – focus on the equipment itself and its condition
Often our assessments combine components from all three types above to answer the key questions:
1. Where do you stand?
- What is your situation now?
- Are you on top of your industrial risks?
- What are you getting for each RMB you spend on maintenance?
2. What could you gain?
- What direct costs could easily be cut?
- What would performance improvements deliver to the bottom line?
- What risks can be prevented, controlled or mitigated?
3. How can you achieve your goals?
- We provide prioritized action plans
- A guide for implementing the action plans
- Based on a knowledge-base of best maintenance management practice
Our working approach
Siveco China assessments always involve active cooperation between the customer’s and Siveco China teams, based on the following working principles:
- A dedicated expert on your project
- An on-site action focused on your main requirements, driven by a Siveco China project manager, assisted by maintenance engineers
- A partnership approach of our work: we recommend efficient, long-term solutions, and prepare your teams in a self-working organization
Confidentiality and independence: Siveco China will sign Non-Disclosure Agreements as required by customer, managed under our ISO 9001:2015 quality system.
Safety is non-negotiable: all Siveco China employees will wear the necessary personal protection equipment when working on site.
Note that all Siveco China projects are offered on a fixed price basis for the scope defined in an agreement.
Methodology
The Siveco China assessments are based on a standard assessment methodology that we have used in many projects across China, and on the professional expertise of our team members, always capable to adapt and improvise if needed.
Whenever applicable, European and IEC standards are used (alternatively, customer can request specific standards to be applied), chiefly the ISO 55000 Asset Management standard (also known as the GB/T 33172-2016 series in China).
Assessments always comprise three main phases as shown in the figure:
For the assessment, standards of interest include:
- ISO 55000 Asset Management – Management Systems, as a risk-based framework for maintenance.
- EN 13460: Maintenance – Documents for maintenance.
- EN 15341: Maintenance – Maintenance key performance indicators, as offering a user-friendly collection of standard performance measures.
- CEN/TR 15628: Qualification of maintenance personnel, for HR/skills management aspects.
- ISO 14224 Collection and exchange of reliability and maintenance data for equipment, addressing data needed to manage maintenance and offering strong support for the design of a maintenance system.
Deliverables
The main deliverables for the assessment are:
- Detailed assessment report (completed Excel document and analysis report, which would include, depending on the scope of assessment, pictures, work processes maps, etc.)
- Recommendation report with related action plan. Recommendation report could include ROI estimates (if financial data was made available to Siveco China) or other improvement metrics.
- Optionally, the above data and action plans in advanced electronic format (for example to be managed in a CMMS) with possible follow-up services by Siveco China.
The report with our recommendations will be presented to the management team at the end of the project, after which discussions will take place. A final conclusion report will be drafted at the end of the session.
3. The supporting tools and resources
Benchmarking
Benchmarking with international standards and other companies plays an important role in all Siveco China assessments.
Our growing customers’ database in China and abroad allows us to benchmark your operations to other plants in similar or different industries. We also run multisite assessments with internal benchmarking between your own sites.
A strong basis for our maintenance benchmarking in China has been the annual “Maintenance in China” survey that Siveco China has run in association with the Sino-European School of Technology of Shanghai University and the European Chambers of Commerce since 2006, covering over 1,500 multinationals in the country.
IT tools
Owing to Siveco China’s strong background in using technology to support maintenance improvement, IT tools play an important part in supporting assessment services, depending on the scope and size of the assessments.
The three main IT tools used by Siveco China to manage all its projects are:
- 8Manage: for project management
- bluehoney: for project activity time and cost reporting
- Ding Talk: for travel approvals and internal chat communication
In addition, detailed methodology guidelines for each types of assessment is pre-established, serving as a guide for Siveco China’s engineers during the assessment itself, in Excel and/or document formats, centralized in Siveco China’s cloud server.
Finally, when conducting site assessments, Siveco China engineers are equipped with bluebee® Surveyor: a unique tool to capture information from the field, record asset conditions, or even to build a complete facility or plant database by simply walking around and taking pictures. Follow-up actions (job request, preventive job) are automatically created and updated into Siveco China’s central server database. Depending on the scope of contract, Siveco China can then deliver a complete technical database, including photos, remedial actions to be taken, etc. in CMMS format (by remote access or installed at the customer’s site).
All our management systems are web based or mobile based, allowing access from anywhere.
The Siveco China back-office
Assessments are conducted by true maintenance experts appointed on the project, under the responsibility of a dedicated project manager:
- Our team members have worked previously as maintenance managers, preventive maintenance engineers, CMMS leaders in facilities, manufacturing and infrastructure projects.
- The Siveco China team comprises both local experts and foreign experts with experience of world-class maintenance.
- Our CMMS experts have working knowledge of various systems (CMMS, ERP, SCADA) available in the Chinese market.
In addition, during the entire project, the assessment team will have access to Siveco China Shanghai’s back-office resources, which includes:
- Back-office teams and the Siveco China network of experts on specific technologies (e.g. vibration analysis or corrosion), specific facilities or equipment (e.g. HVAC specialists) or methodologies (e.g. IEC standards).
- Centralized IT tools including benchmarking database and CMMS.
4. The assessment and its benefits in practice
In practice, for the typical assessment, two Siveco China engineers will come to your site for approximately one week. For a CMMS/EAM assessment, one engineer will focus on maintenance management, the other on the utilization of the system itself. For a more organizational assessment or a facility condition assessment, the assessment will involve specific industrial skills as required. Onsite work will be concluded by a presentation workshop, followed by report preparation time, before the final deliverables are handed over to the client.
Siveco China has experience conducting assessments in all three target segments: Facility Management (property owners and FM suppliers), Industry (factories in various industry, process or discrete manufacturing) and Infrastructures. Nowadays, in addition to independent assessments, all our projects include a start-up assessment and our “enhanced maintenance contracts” also utilize our assessment practice. The accumulated experience of our team (some of our team members have been active in this field since 1997) is unparalleled in China.
A case study of a CMMS assessment was presented in a past newsletter.
Some of the concrete benefits observed in previous assessments include:
Maintenance organization assessment at a large process plant
The overall conclusion of the assessment showed that the company should focus on improving performance instead of further cost cutting: analysis of financial figures and comparison with benchmarks show that the plant has extra capacity to fund this effort, i.e. it can easily afford the additional cost. This would result in downtime reduction with easily measurable returns: a detailed technical study estimated returns at 1 million RMB within one year on the main machines alone.
CMMS assessment (SAP PM and various other systems) at a chemical plant
The in-depth assessment showed that the company underutilizes its SAP infrastructure but has built a practical way to work around it, using various additional systems and well-defined management procedures. Overall the maintenance system is working rather well compared to similar companies in China, whether using SAP or other CMMS tools. This is to the credit of the company’s strong maintenance team members and management.
Weaknesses in analysis and decision support started to affect the capability of the maintenance division to improve its performance, while production put increasing demands on reliability.
Siveco China recommended implementing small improvements in SAP Work Orders and to develop better reports (probably using the SAP Business Warehouse tool already in place in other departments). A third-party mobile solution would certainly enhance the inspection process, allowing a full feedback loop to manage preventive maintenance improvement. The costs/benefits of the various options were analysed.
CMMS assessment (Maximo) at automotive plant
The assessment found that the maintenance organization focuses its efforts on basic preventive maintenance: inspection, greasing, etc… as it lacks the necessary tools to eliminate failure through technical analysis. As the maintenance team is understaffed and busy with production-related tasks, and without proper support from the CMMS, they do not have the time to manually process long lists of WO feedbacks, although they do have the technical knowledge to understand their machines and find solutions.
This situation finally leads them to insure themselves against breakdown risk by adding more inspections (i.e. more workload). This is consistent with the pure “workstation approach” of the current failure analysis tool: the inspection plan is based on workstation.
The systems proved to be one of the bottlenecks and no solution was proposed by the IT vendor other that providing resources to develop reports. These problems reflect implementation- rather than software-related weaknesses, resulting in low ROI on the CMMS investment.
Siveco China recommended a complete course of action, based on improving technical feedback, with standard pick-lists for downtime, causes, actions etc. The equipment structures should be reorganised to accommodate such reporting (currently not possible). IEC 81346 or ISO 14224 standards were proposed as the basis for this change.
Facility condition assessment at a major retailer
A full facility assessment was conducted in one of the buildings, covering the building itself and all systems (HVAC, water, fire-fighting, lifts, etc). The study also included a review of the FM suppliers’ contracts, the quality of their work and the paper-based reporting systems. Siveco China delivered a full assessment report in two formats: office documents (word file with pictures, Excel list of recommended actions, updated maintenance plan in Ms Project format) and in database format, easily up-loadable into a CMMS. For each problem detected, a diagnosis was proposed, together with corrective and future preventive actions, allowing the retailer not only to take immediate measures, but also to prevent reoccurrence of problems. A management solution was proposed in order for the customer to better manage its facilities in the long term.
Siveco China Head Office
Unit J, 20th floor, Zao Fong Universe Building
No.1800 Zhong Shan Road (W)
Shanghai 200235 - PR China
About Siveco China
Siveco China (www.sivecochina.com), founded in 2004, is a pioneer in the development of Smart Technologies for the Operation & Maintenance of infrastructures and industrial plants, with a focus on mobile solutions "for the worker of tomorrow".
Long before the terms "smart" and "4.0" were coined, Siveco has been helping clients optimize the lifecycle of their assets and ensure regulatory compliance using IT. Based on a long experience of "maintenance with Chinese characteristics", the company has designed a unique approach combining expert maintenance consulting and technological innovation. Smart O&M solutions developed in Siveco's R&D center in Shanghai cover Asset Management, Maintenance 4.0, Risk Prevention and HSE, utilizing Mobility, IoT, BIM, AR and AI technologies.
Siveco China has over 900 customer sites all over Greater China and on the Belt & Road, including ABB, Baosteel Metal, Beijing Environment, Capital Water, Carrefour China, CEPSA, CNEEC, CNOOC, COSCO, Fushun Mining, Engie, Everbright, GE, New World Development, Saint-Gobain, Shell, Suez NWS, Yingde Gases, Zhongshan Water etc. The company boasts a growing export business, working alongside Asian EPC companies and with international clients in Southeast Asia, the Middle-East and Africa.
Siveco China has won numerous awards, most recently the prestigious Brilliant 40 Years prize by the China Electric Power Equipment Management Association, Top Ten Enterprise for Asset Informatization Service by the and the China Association of Machinery Equipment Maintenance and Renovation (CAMER) and Best Industrial Software 2017 by Control Engineering China. Previous awards include CHaINA Supply Chain Excellence Award 2013 and Engineers' Choice Awards by Plant360 in three categories in 2015.
Siveco is ISO 9001-certified by Bureau Veritas for its entire scope of business. The company is headquartered in Shanghai, where it also operates its R&D center, and has offices in Hong Kong. Siveco China is a subsidiary of Siveco Group, a European pioneer in computerized maintenance management systems (CMMS).
Siveco China publishes the "Smart Operation & Maintenance - for the worker of tomorrow" newsletter dedicated to maintenance management, bilingual English and Chinese, available to subscribers and online.
Contact
Tel (China mainland): 4006 300 213
Tel (overseas): +86 21 64403226
E-mail : info@sivecochina.com
This release was published on openPR.
Permanent link to this press release:
Copy
Please set a link in the press area of your homepage to this press release on openPR. openPR disclaims liability for any content contained in this release.
You can edit or delete your press release The maintenance assessment: a stepping stone for improvement here
News-ID: 2309270 • Views: …
More Releases from Siveco China
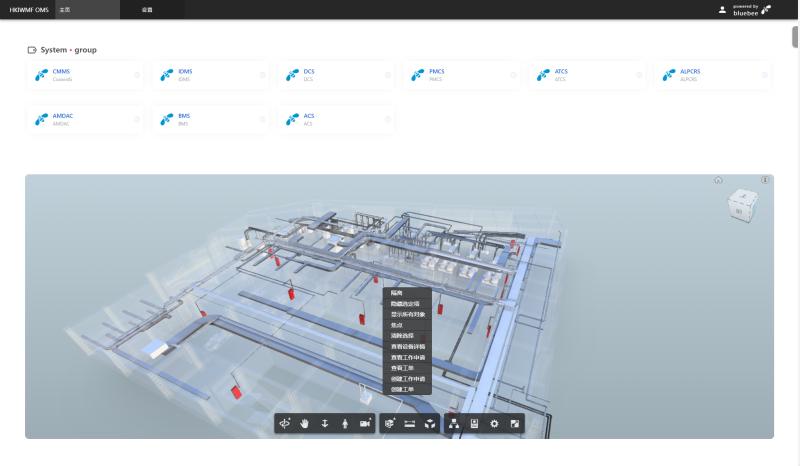
ESG & decarbonization in operations: the digital gap
(This article was previously published in the December 2022 issue of APUEA magazine.)
ESG (Environmental, Social, and Governance) is a framework that helps stakeholders understand how a company is managing risks and opportunities related to environmental, social, and governance criteria. Looking at ESG from a plant management's perspective: Environmental includes energy, water and waste. Social covers safety, first and foremost. Governance consists in complying with regulations and best practices, as well…
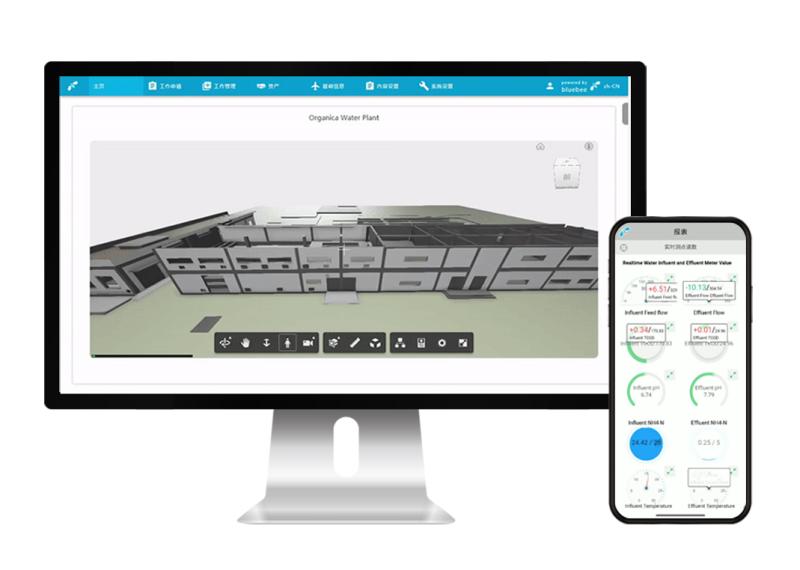
The Future of Operation & Maintenance
Media hype has led us to believe that technology would soon revolutionize maintenance. Dreams of flying robots, video game-like smart glasses, flashing digital twins, often hold the sad promise of getting rid of maintenance people altogether. The reality remains that the more automated, the more sophisticated the systems, the more demands are put on maintenance people and their skills. The problem is compounded when this glorious technology did not address…
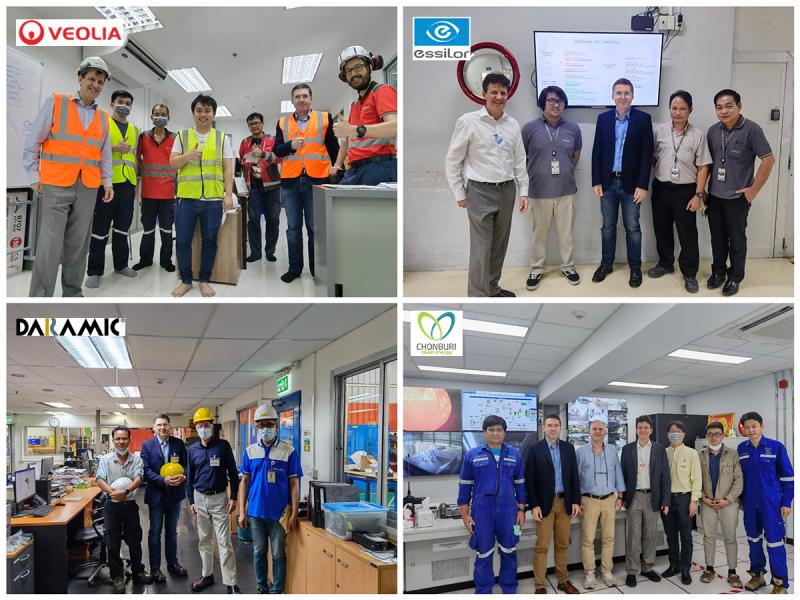
On the Belt & Road with clients and partners in Thailand
Thailand is a priority for Siveco China's development in Southeast Asia owing to the country's well-developed industry and growing infrastructure development. During October, our Managing Director visited local clients and partners.
Please enjoy our postcards from Thailand!
Several new partnerships and projects were also launched during this period - more on this later!
Siveco China is active all over Asia with projects not only in Thailand, but also in Brunei, India, Indonesia,…
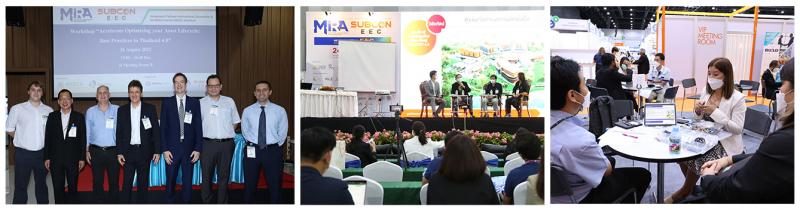
Feedback on "Accelerate Optimizing your Asset Lifecycle: Best Practices in Thail …
Siveco China organized a team of high-profile speakers at MIRA SUBCON EEC, Thailand's Leading Industrial Solutions Event, held on August 26 in Pattaya. The session was hosted by the Asia Pacific Urban Energy Association (APUEA). Under the theme "Accelerate Optimizing your Asset Lifecycle: Best Practices in Thailand 4.0", the workshop aimed at sharing practical experience for the local market.
After an introduction by APUEA's Executive Director Peter Lundberg, the event…
More Releases for CMMS
SuperCMMS launches free CMMS for SME's.
BOSTON - Sept. 25, 2024 - SuperCMMS is excited to announce the launch of its innovative Computerized Maintenance Management System (CMMS), designed to simplify maintenance management for businesses across various industries. With a user-friendly interface and completely free access, SuperCMMS empowers organizations to efficiently manage work orders, streamline operations, and enhance productivity without the burden of software costs. SuperCMMS caters to a diverse range of sectors, including manufacturing, retail, fleet…
Global Equipment Maintenance Systems Market Optimizing Asset Performance and Rel …
Infinity Business Insights shared report on "Equipment Maintenance Systems Market" which provides in-depth analysis of parent market trends, macro-economic indicators and governing factors along with market attractiveness as per segments. This report will help the viewer in Better Decision Making.
The Market for Equipment Maintenance Systems is anticipated to increase at a CAGR of 8.5% between 2022 and 2030, reaching a value of USD 30.7 billion by that time. This rise…
Computerized Maintenance Management System (CMMS) Market Industry Analysis And S …
New York, According to a new market research report published by Global Insight Services Computerized Maintenance Management System (CMMS) Market is expected to reach US$ XX bn by 2031. Report includes in-depth segmentation and market size data by categories, product types, applications, and geographies. Report also includes comprehensive analysis of key issues, trends and drivers, restraints and challenges, competitive landscape, as well as recent events such as M&A activities in…
Computerized Maintenance Management System (CMMS) Software in Healthcare Market …
Computerized Maintenance Management System (CMMS) Software in Healthcare Market Size, Status and Forecast 2019-2024 Report present the worldwide analysis with in depth study of Top players, region, type and application and its future scope.
The report mainly studies the size, recent trends and development status of the Computerized Maintenance Management System (CMMS) Software in Healthcare market, as well as investment opportunities, government policy, market dynamics (drivers, restraints, opportunities), supply chain and…
Work Order Management Tools Market Emerging Trends || Leading Players are eMaint …
A detailed research study on the Work Order Management Tools Market was recently published by DataIntelo. The report puts together a concise analysis of the growth factors influencing the current business scenario across various regions. Significant information pertaining to the industry analysis size, share, application, and statistics are summed in the report in order to present an ensemble prediction. Additionally, this report encompasses an accurate competitive analysis of major market…
Increase Employee Retention with CMMS Software
A growing number of organizations use CMMS software to streamline maintenance tasks and extend the life of equipment. Some of the more easily quantifiable benefits that CMMS software brings to an organization include higher production volumes, increased staff productivity, and lower maintenance costs. However, maintenance software also offers numerous “soft” benefits, one of which is boosting employee retention.
Employees are one of an organization’s most valuable assets, which is why…