Press release
Vacuum supply with 70 per cent less energy consumption
Antipasti and delicatessen products have been the speciality of the Feinkost Dittmann delicatessen company for over one hundred years. At the production site in Taunusstein, Germany, various products are manufactured as preserves in glasses or as fresh products packed in plastic trays. Vacuum supply for the packaging machines has been performed by a central vacuum system by Busch for over a year [installation 12/2013]. It is considerably more economical than the vacuum technology used previously. The energy consumption alone was reduced by more than 70 per cent.The history of Feinkost Dittmann (Reichold Feinkost GmbH) goes back to 1901, when Carl Dittmann opened a delicatessen business in Wiesbaden, Germany. Today, Feinkost Dittmann is the German market leader for olives, antipasti, capers, garlic and anchovy specialities and the most popular delicatessen brand in the German trade market. The family-run business has its headquarters in Diez, Germany near Limburg an der Lahn. The German production plant is in Taunusstein near Wiesbaden, where a total of 320 employees produce different antipasti specialities made, for example, from olives, feta cheese, garlic, pepper or dried tomatoes and many other delicacies. In turn, these are sent to national and international retail store chains and discount stores under the company's various own brand names. The family business currently exports its diverse specialities to over 30 countries worldwide. Feinkost Dittmann also produces delicatessen products at its own facilities in Spain, Greece and Turkey.
Products in the so-called "fresh department" are packed in plastic trays in the production building in Taunusstein. During this process, air is sucked out of the packaging trays before a CO2N2 protective gas mixture is added to the package. Synthetic material foils are then used to give the packaging a gas tight seal before the packaging is closed with an additional plastic cover. This type of packaging guarantees that the oxygen content is under one per cent thanks to the evacuation of air and use of protective gas in the packaging. This dramatically increases the products' shelf life. The product presentation with transparent packaging is also ideal because foil does not lay directly on the product or even perhaps crush the product due to the negative pressure in the packaging.
In total, four packaging machines (tray sealers) are used for packing during two-shift operation. The vacuum required for this is generated by six oil-lubricated rotary vane vacuum pumps with 5.5 kilowatts of motor power each. They were originally installed directly on the packaging machines. For hygienic reasons and to reduce the thermal load in the production rooms, these vacuum pumps were later installed in a separate room above the production room and connected to the packaging machines using a pipe network. Andreas Lutz, the technical project manager in the production plant, was not very happy with this solution because the vacuum pumps still required high levels of maintenance. Also, fluctuations or failures in the vacuum network were first noticed if one of the packaging machines showed an error message and automatically shut down when the vacuum level was not reached quickly enough or was not reached at all. This led to repeated production downtimes on individual packaging lines.
In 2013, Andreas Lutz contacted the vacuum specialists from Busch. They were tasked with offering a more reliable and efficient solution. At the same time, continued use of the existing pipe network was to be integrated. In addition, the vacuum supply was to be designed in such a way that connection of further packaging machines would be possible if production capacity were to grow. Busch analysed the conditions on site and all technical parameters in detail and worked together closely with the project manager from Feinkost Dittmann and the in-house laboratory. The result of this analysis and comprehensive consultation was a central vacuum system with four Mink claw vacuum pumps.
These have the basic advantage that they do not require an operating fluid such as oil in the compression chamber. This makes all maintenance work that has to do with oil unnecessary; for example, oil checks, oil changes, oil filter changes and the costs for procuring and disposing of oil and filters. Mink claw vacuum pumps also use non-contact operation. This means that there are no parts in the compression chamber that come into mechanical contact and thus cause wear. This renders the exchange of wear parts and the associated working hours and costs unnecessary. The non-contact operation method of claw vacuum technology also enables a high degree of efficiency and thus requires less motor power than conventional vacuum pumps.
This central vacuum system was installed at the end of 2013. Three vacuum containers with a volume of 3,000 litres each are upstream from the Mink claw vacuum pumps. This ensures that sufficient vacuum levels are immediately available at the machines when they are needed.
Previously, all six rotary vane vacuum pumps were in operation an average of 15 hours per day. The Mink vacuum pumps in the new central system are controlled so that only those currently needed for the actual vacuum requirements are running.
Two of the vacuum pumps with standard motors are responsible for the so-called base load. The other two vacuum pumps are frequency controlled and ensure fine adjustment of the vacuum requirements by adjusting their speed. With this intelligent solution, the pumping speed of the central vacuum system adjusts itself precisely to the current requirements.
These controls drastically reduce the actual operating times of the individual vacuum pumps because, during normal operation, all four vacuum pumps never need to operate at full load. So Feinkost Dittmann's central vacuum system has sufficient power reserves to connect further packaging machines. There is a plan to additionally connect a vacuum filler for glass preserves, which would eliminate the need for the current decentralized liquid ring vacuum pump installation with 7.5 kilowatt drive and thus create further energy savings.
After more than two years of operation, project manager Andreas Lutz is extremely positive when he takes stock of the situation:
- Reduction of energy requirements by more than 70 per cent
- Drastic reduction of maintenance efforts
- Increased reliability
- No failures or breakdowns
Maintenance of the new central vacuum system is performed by service technicians from Busch. However, this is limited to annual measurements of the ultimate pressure and current consumption at each of the individual vacuum pumps as well as changing the upstream particle filters and an oil change in the gearbox.
Busch Vacuum Pumps and Systems is one of the largest manufacturers of vacuum pumps, blowers and compressors in the world.
With a lot of experience and top qualified personnel, we are forward-looking and strive to improve our products and ourselves. We are constantly at work developing innovative technologies that will define the vacuum world of the future.
Our manufacturing plants utilize the most modern manufacturing techniques, machinery and equipment under very strict quality controls, which surpass DIN EN ISO 9001 requirements.
As of 2016, Busch Vacuum Pumps and Systems employs more than 3000 people and features the largest selection of vacuum pumps for the industrial applications in the world. Due to its immense line of vacuum pumps, expertise and experience in the building of vacuum systems and the extensive service network, Busch is capable of providing ideal comprehensive solutions.
With 60 companies in 42 countries and sales agents in over 30 countries, we are strategically positioned throughout the world to provide our customers with the essentials for success.
Our goal always is to provide the customer with the highest possible return on investment. Personal consulting, choice of the optimum product and prompt service on site are key features of our comprehensive service that make the achievement of this goal reality. Our experience and know how in broadly diversified applications and product design furnish the basis.
Busch’s headquarter is located in Maulburg, Germany. Besides Busch Holding, the German manufacturing plant, Busch Produktions GmbH, the sales organization, Dr.-Ing. K. Busch GmbH and service company, Busch Dienste GmbH are headquartered here. In addition, Busch operates production plants in Switzerland, Great Britain, Czech Republic, Korea and the USA.
Uli Merkle
Head of Marketing Services
Telephone: +49 (0)7622 681-144
E-Mail: Uli.Merkle@busch.de
Website: www.buschvacuum.com
This release was published on openPR.
Permanent link to this press release:
Copy
Please set a link in the press area of your homepage to this press release on openPR. openPR disclaims liability for any content contained in this release.
You can edit or delete your press release Vacuum supply with 70 per cent less energy consumption here
News-ID: 469098 • Views: …
More Releases from Busch Dienste GmbH
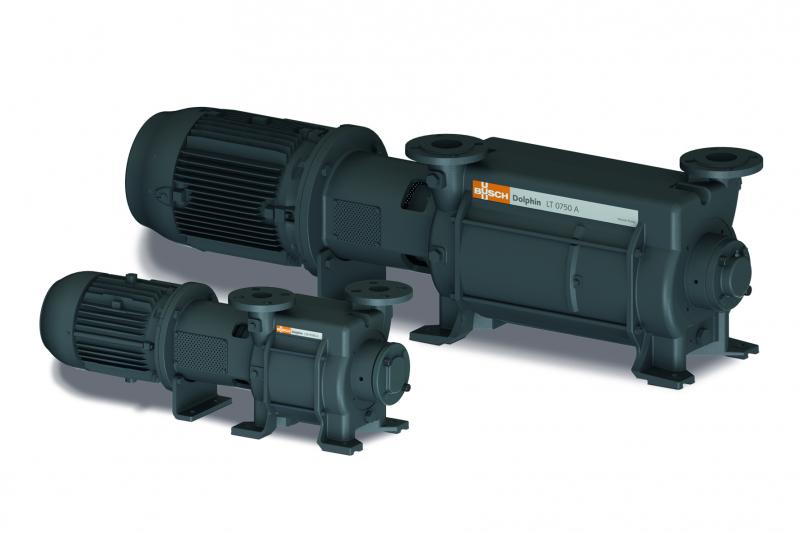
Liquid ring vacuum pumps – Classic vacuum technology and yet still state of th …
Vacuum technology has never stopped developing – not only in the recent past, but for decades it has continued to progress. Today, dry screw vacuum pumps are used in chemical processing technology and many other applications just as dry claw vacuum pumps have established themselves as standard vacuum generators in entire branches of industry. Oil-lubricated rotary vane vacuum pumps are also state of the art in many applications, not least…
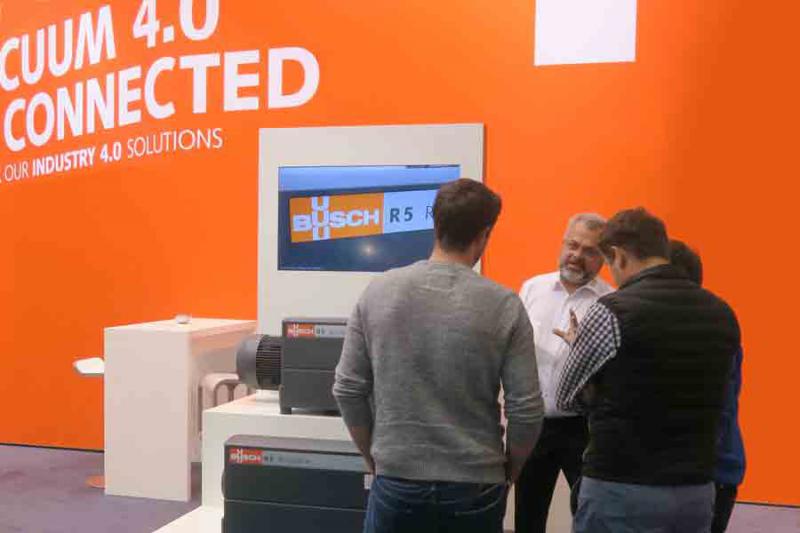
Proven vacuum technology fit for Industry 4.0
Busch Vacuum Pumps and Systems enjoyed a great deal of interest from an audience of experts at the IFFA in Frankfurt. The vacuum technology specialist showcased its latest products for the vacuum packaging of meat and sausage products and for meat processing.
Busch also premiered the new R 5 PLUS rotary vane vacuum pump, which is prepared for Industry 4.0. This innovative vacuum pump is based on proven rotary vane vacuum…
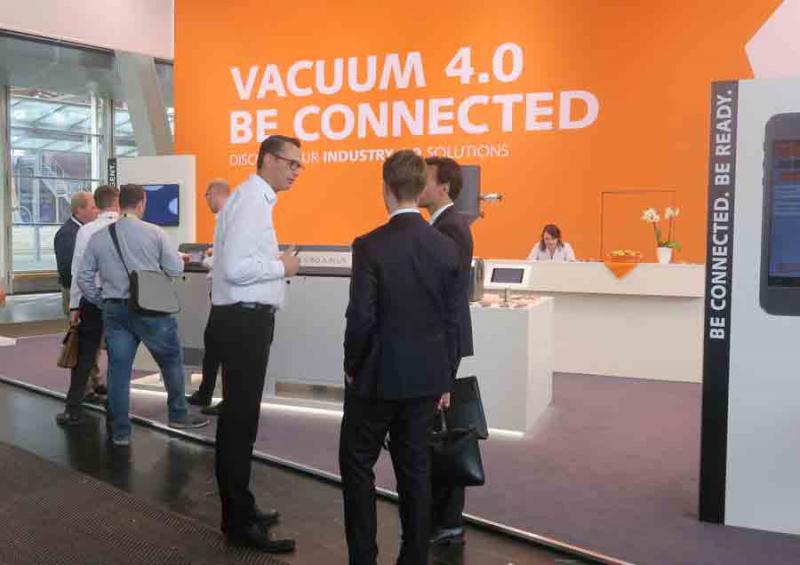
Busch solutions for Industry 4.0 at ComVac
The Busch Vacuum Pumps and Systems trade show appearance received a great response from visitors to ComVac, the leading international trade show for compressed air and vacuum technology, held in Hanover, Germany. The interested trade show crowds were able to discover the topic of Vacuum 4.0 and the best-fitting innovative vacuum solutions at Busch.
Numerous visitors took the opportunity to talk to the Busch vacuum experts. With Vacuum 4.0, Busch is…
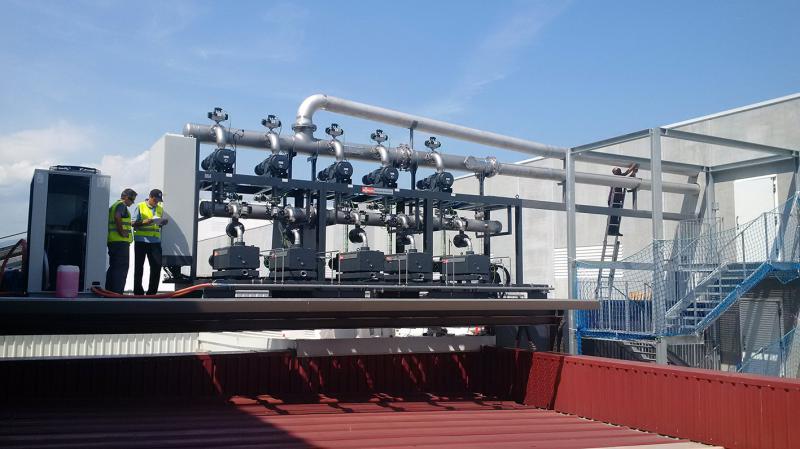
Dry vacuum systems for centralization of vacuum supply
The concept, design and realization of central vacuum supplies is one of Busch Vacuum Pumps and Systems' core competencies. Thousands of such vacuum systems are in operation worldwide. A wide range of operating principles for generating vacuum in the individual pump modules are applied. In addition to oil-lubricated R 5 rotary vane vacuum pumps, dry-compressing vacuum modules can be used, for example in vacuum systems with COBRA NX screw vacuum…
More Releases for German
Find the best conditions for your German mortgage with Your German Mortgage
During times of the Coronavirus, we are here to help you with finding the right financing for your property.
Special times call for special measures, that's why it's now more important to find a trustworthy and experienced mortgage broker than ever.
We got you covered from finding your property of dreams all the way to financing it.
To ensure that, we have experts in almost every German major city,…
German Maritime Security 2018, German Government Statement!
Despite all international and national efforts, piracy remains a serious peril for the international shipping industry.
Especially in Asia (i.e. Chittagong/Bangladesh or on the Strait of Malacca), but also in South America (e.g. Bay of Santos/Brazil or in the port of Callao/Peru) robbery or piracy there has recurred in the recent past. At the West African coast the number of incidents had raised even by 50% with 66 incidents this…
German Design Award 2015
German Design Council Awards a Special Mention to the LR 1000 Laboratory Reactor and Nominates the Tube Mill
Staufen, Germany, February 23, 2015 —
For the second time, a device produced by IKA® Werke has received the "Special mention for exceptional design quality" award from the German Design Council.
The company was presented with the award in the "Excellent Product Design — Industry" category as part of the German Design Award 2015…
German Local Trade Tax
All the companies in Germany are liable to pay not only corporate income tax, whose rate is nowadays about 15% of the annual profit of the company, but also trade tax (Gewerbesteuer), which is a tax of German characteristics.
Why would we say that trade tax is of German characteristics? Because it is different from the corporate income tax, which is charged by the German Federal Government and it is difficult…
Integral Launches German Bureau
Integral Launches German Bureau
Appoints Suchit Manchanda as the Head of Operations
January 4, 2010: Germany: Integral Fusion, a leading software services firm, has launched operations in Germany and announced the appointment of Suchit Manchanda as their Managing Director. The German bureau will be responsible for strategic business development in European Union organizations and client servicing. Suchit a world class MBA from Hochschule Nürnberg, Germany and a Masters in IT from Jamia…
ISPA – German Masters 2008
Magdeburg – Over the long weekend of the 4. Mai more than 1.000 Skat players filled the Mittelland hall in Barleben. The tournaments of the 30. German Mastery and the 27. open International German Single Mastership were held by the International Skat Players Association, ISPA Germany. Patrons of the Games were the 1st Barleber Skat sports club e.V. and the Skat club \"Burger Ihleskater\", whose good organization together with the…