Press release
Factory Setup: Manufacturing Plant Setup Strategy
The Establishment of Factory Setup This is the whole setting up of the factory for the purpose of producing goods. The factory setup involves the site selection, designing of layout of the factory, and equipment purchase. The factory setup also involves the licenses required, safety and environmental conditions, and employee hiring. Lastly, it deals with the infrastructure of the factory, which includes power supply, water pipes, and waste disposal method. After that, the supply chain management systems and inventory systems are established to ensure efficient production. The factory setup is important for a business in its attempt to scale its operations and provide the necessary service to the market.Factory Setup Strategy:
A successful factory setup strategy is designed to make the most of resources, minimise costs, and be scalable. This typically begins with a feasibility study to assess the demand in the market, the competition, and the suitability of the location. Decisions are then made on the basis of supplier proximity, transportation infrastructure, and labour skills. An effective layout plan and state-of-the-art investment are essential for the smooth operation of the factory. Sourcing the right materials is essential and recruitment also needs to be completed. The factory will be regularly audited and the environmental and safety issues will be addressed. Then, an appropriate audit will be completed. It is also important to have a continuous improvement plan and to be able to scale up the factory.
Factory Setup Location and Planning:
Selecting the right location and meticulous planning are crucial steps in setting up a successful factory. The location directly impacts operational efficiency, logistics, costs, and market access. Here's a breakdown of key factors to consider:
1. Proximity to Suppliers and Raw Materials
Choosing a location close to key suppliers and raw materials reduces transportation costs and ensures timely deliveries. This helps minimize inventory holding costs and lowers overall production expenses. A strategic location near suppliers also enables smoother supply chain management and mitigates risks related to material shortages.
2. Transportation and Infrastructure
Accessibility to major transportation networks like highways, ports, or railways is vital for reducing logistics costs. A location with well-developed infrastructure such as reliable roadways, telecommunications, and utilities will facilitate smooth operations. Reliable infrastructure minimizes the risk of disruptions and delays in production and distribution.
3. Labor Availability
A plant ought to be situated in an area where skilled and cost-effective labor is available. Educational institutions or vocational training centers near the site can provide a pool of trained workers. It is also essential that the labor laws and costs in the region are in line with the needs of the plant to maintain operational efficiency and control expenses.
4. Regulatory Compliance and Government Incentives
It is critical to understand laws of local government such as taxes, labor laws, environmental standards. In some places, a tax break, a subsidy, or another incentive is offered for the construction of a factory, which can significantly reduce the cost of the beginning and operation of the business. It is important to know this to get maximum profit.
5. Environmental and Safety Factors
It is fundamental to consider the environmental impact and safety of the chosen location. It is of integral importance to have pollution control waste management systems and respect local environmental regulations to ensure sustainability in the long term. To maintain an appropriate working environment that prevents accidents and that complies with health and safety regulations is also crucial.
6. Future Growth Potential
The selection of a location that allows for growth is critical. The scale of the factory arrangement must be able to grow based on the need for production. The availability of land and the ability to access new markets will secure the factory's success in the event of increased demand.
Infrastructure and Equipment of Factory Setup:
The infrastructure and equipment are the backbone of any manufacturing facility, directly influencing production efficiency, product quality, and overall operations. Proper planning and investment in these areas are essential for a successful factory setup.
1. Infrastructure Planning
Factory infrastructure comprises of the physical buildings, utilities and systems that are essential for a productive working environment. A factory layout should be designed in such a way that optimizes space, workflow and safety. Key considerations include:
• Building Design: Hence the building design should have enough space for machinery, assembly lines, storage areas and employee work stations. Future expansion plans should also be factored in.
• Utilities: The water, electricity, gas and waste management systems are indispensable for the uninterrupted work of the factory. Backup power sources like generators should be foreseen for the uninterrupted work of the factory during the power failure.
• Safety Systems: The given infrastructure must be equipped with fire prevention systems, emergency exits, ventilation, and hazard control measures; it will allow creating a safe working environment.
• Logistics and Storage: Ample storage for raw materials and finished products, as well as easy access for transportation, should be part of the infrastructure.
2. Equipment Procurement and Installation
Key parameters that are essential include the choice of machinery and equipment. The level of current production capacity depends on them. The equipment of the factory should be selected on the basis of the manufactured product and the production processes. Key equipment includes:
• Machinery: The type and the number of the machines depend on the production volume and complexity. Among these are the assembly lines automated systems, conveyors, packaging machines.
• Material Handling Equipment: Forklifts, cranes and conveyors provide the efficient movement of materials across the factory floor.
• Quality Control Tools: Quality assurance equipment, such as testing machines sensors, and measuring instruments are used to ensure the quality of products.
• IT and Automation Systems: Adopting ERP, production observation tools and mechanization software could result in the streamlining of operations, lesser mistakes and better efficiency.
3. Maintenance and Upkeep
A proactive maintenance strategy is crucial to ensure equipment longevity and prevent unplanned downtime. Routine checks, calibration, and servicing should be scheduled regularly to keep equipment running at optimal levels.
4. Technological Integration
Within modern factories, smart technologies including IoT devices are integrated. Robotics and AI-driven systems are also included. These technologies make manufacturing more efficient. IoT devices are also used for predictive maintenance.
Operations and Logistics of Factory Setup:
The smooth functioning of a factory majorly relies on operations and logistics. They ensure that production workflows are managed effectively and the supply chain is optimized. A well-coordinated effort guarantees that costs are managed, deliveries are made on time, and the quality of the output is controlled.
1. Production Planning and Workflow Optimization
A factory's operations should be designed to minimize downtime and maximize efficiency. This includes:
• Implementing Lean Manufacturing techniques to eliminate waste and improve productivity.
• Organizing workflow layouts that ensure a seamless transition of raw materials to finished products.
• Establishing quality control checkpoints to detect and prevent defects at each stage of production.
2. Supply Chain and Inventory Management
Efficient logistics ensure that raw materials arrive on time and finished goods reach customers without delays. This involves:
• Supplier Coordination: Establishing relationships with reliable suppliers for timely material availability.
• Inventory Optimization: Using Just-in-Time (JIT) or automated inventory tracking to minimize holding costs.
• Warehousing and Distribution: Proper storage facilities to handle stock efficiently, ensuring quick dispatch.
3. Transportation and Distribution
• An effective transportation strategy reduces costs and ensures timely deliveries. Key aspects include:
• Selecting strategic factory locations near major transport hubs (ports, highways, or rail networks).
• Using logistics software to plan optimal routes and manage fleet operations.
• Partnering with third-party logistics (3PL) providers for efficient distribution.
4. Workforce and Operational Efficiency
Training employees to handle machinery, follow safety guidelines, and use digital tools enhances operational efficiency. Using automation and real-time monitoring helps track production metrics and improve output.
read more about Factory Setup - https://www.imarcgroup.com/services/factory-setup
Contact Us
IMARC Group
C-130, Sector 2, Noida, Uttar Pradesh 201301, India
Email: Sales@imarcgroup.com
Tel No:(D) +91 120 433 0800
Americas:- +1 631 791 1145 | Asia: +91-120-433-0800, UK - +44-753-714-6104
IMARC Group is a leading market research company dedicated to providing data-driven insights and expert consulting services to support businesses in achieving their strategic objectives across diverse industries.
This release was published on openPR.
Permanent link to this press release:
Copy
Please set a link in the press area of your homepage to this press release on openPR. openPR disclaims liability for any content contained in this release.
You can edit or delete your press release Factory Setup: Manufacturing Plant Setup Strategy here
News-ID: 3971926 • Views: …
More Releases from IMARC Group
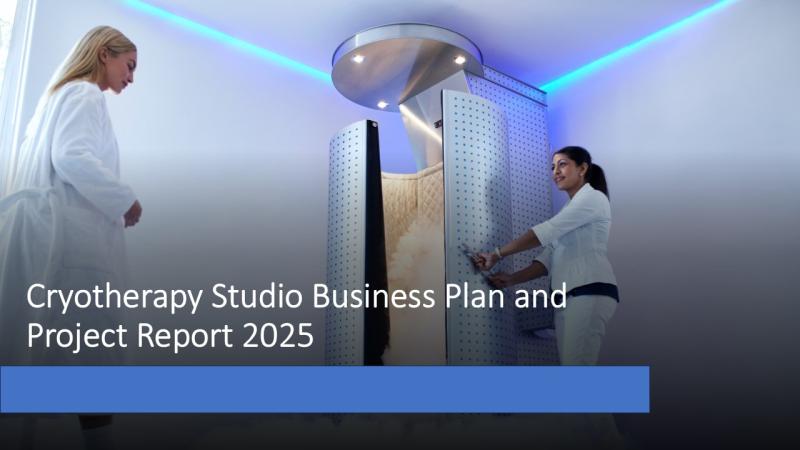
Cryotherapy Studio Industry Forecast 2025: Profit Potential for Investment
IMARC Group's "Cryotherapy Studio Business Plan and Project Report 2025" offers a comprehensive framework for establishing a successful cryotherapy studio business. This in-depth report covers critical aspects such as market trends, investment opportunities, revenue models, and financial forecasts, making it an essential tool for entrepreneurs, consultants, and investors. Whether assessing a new venture's feasibility or optimizing an existing business, the report provides a deep dive into all components necessary for…
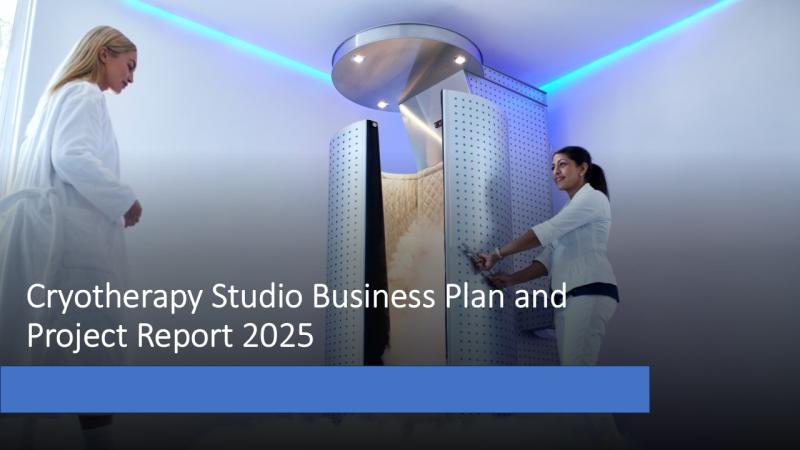
Cryotherapy Studio Industry Forecast 2025: Profit Potential for Investment
IMARC Group's "Cryotherapy Studio Business Plan and Project Report 2025" offers a comprehensive framework for establishing a successful cryotherapy studio business. This in-depth report covers critical aspects such as market trends, investment opportunities, revenue models, and financial forecasts, making it an essential tool for entrepreneurs, consultants, and investors. Whether assessing a new venture's feasibility or optimizing an existing business, the report provides a deep dive into all components necessary for…
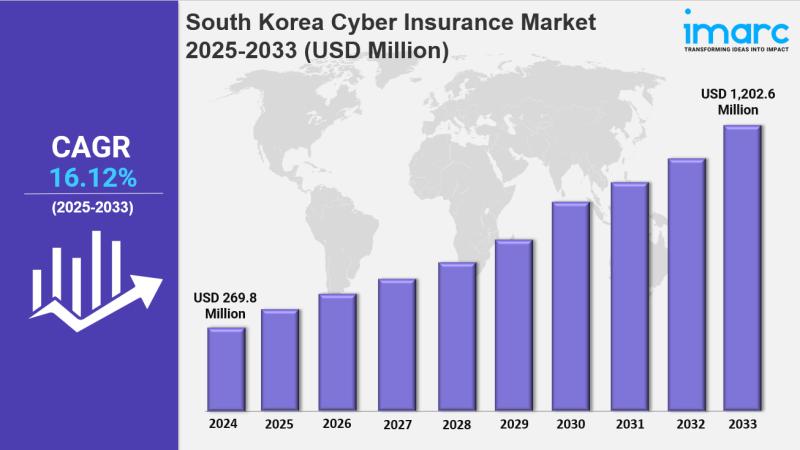
South Korea Cyber Insurance Market Size is Projected To Exhibit Growth Rate 16.1 …
IMARC Group has recently released a new research study titled "South Korea Cyber Insurance Market Size, Share, Trends and Forecast by Component, Insurance Type, Organization Size, End Use Industry, and Region, 2025-2033", offers a detailed analysis of the market drivers, segmentation, growth opportunities, trends and competitive landscape to understand the current and future market scenarios.
South Korea Cyber Insurance Market Overview
The South Korea cyber insurance market size reached USD 269.8 Million…

Psychedelic Therapy Clinic Business Model: Income, Expenses & Profitability
IMARC Group's "Psychedelic Therapy Clinic Business Plan and Project Report 2025" offers a comprehensive framework for establishing a successful psychedelic Therapy clinic business. This in-depth report covers critical aspects such as market trends, investment opportunities, revenue models, and financial forecasts, making it an essential tool for entrepreneurs, consultants, and investors. Whether assessing a new venture's feasibility or optimizing an existing business, the report provides a deep dive into all components…
More Releases for Factory
Prominent Smart Factory Market Trend for 2025: Advanced Technologies Reshape The …
Which drivers are expected to have the greatest impact on the over the smart factory market's growth?
The escalation in need for industrial robots is anticipated to spur the expansion of the smart factory market. Industrial robots are mechanical devices programmed to autonomously carry out production-related tasks in industrial settings. A smart factory emphasizes on resource optimization and industrial automation, employing instruments like information and smart sensor technologies, robotics, the Internet…
Factory Automation Sensor Market Report 2024 - Factory Automation Sensor Market …
"The Business Research Company recently released a comprehensive report on the Global Factory Automation Sensor Market Size and Trends Analysis with Forecast 2024-2033. This latest market research report offers a wealth of valuable insights and data, including global market size, regional shares, and competitor market share. Additionally, it covers current trends, future opportunities, and essential data for success in the industry.
According to The Business Research Company's, The factory automation sensor…
Smart Factory Services – Successful conversion to a smart factory
Weinstadt, May 06, 2024 - The system manufacturer KELCH GmbH has developed a modular overall concept to support individual companies in setting up and expanding their smart factory. Our so-called Smart Factory Services are tailored to the needs of machining companies and consist of modules that can be flexibly combined. This offers manufacturing companies the option of only obtaining the solutions that they actually need – whether to improve processes…
Factory Automation Market Future Assessment 2021-2027 : ABB Ltd., Mitsubishi Ele …
Allied Market Research published an exclusive report, titled, “Factory Automation Market by Control and Safety System (Distributed Control System (DCS), Supervisory Control and Data Acquisition System (SCADA), Manufacturing Execution System (MES), Safety Instrumented System (SIS), Programmable Logic Controllers (PLC), and Human Machine Interface (HMI)), Component (Sensor, Controllers, Switches & Relays, Industrial Robots, Drives, and Others), and Industry Vertical (Automotive Manufacturing, Food & Beverage, Oil & Gas Processing, Mining, and Others)…
Dark Tea Revolutionary Trends (2020-2026) by Industry Statistics| Liming Tea Fac …
"The new report has been added by qyresearch.com to provide detailed insight into the global Dark Tea market. The study will help to get a better understanding about the Dark Tea industry competitors, a channel for the distribution, Dark Tea growth potential, potentially disruptive trends, Dark Tea industry product innovations, market size value/volume (regional/country level, Dark Tea industry segments), market share of top players/products.
Due to the pandemic, we have included…
Fermented Tea Market to witness remarkable growth By 2026| Menghai Tea Factory, …
"The new report has been added by qyresearch.com to provide detailed insight into the global Fermented Tea market. The study will help to get a better understanding about the Fermented Tea industry competitors, a channel for the distribution, Fermented Tea growth potential, potentially disruptive trends, Fermented Tea industry product innovations, market size value/volume (regional/country level, Fermented Tea industry segments), market share of top players/products.
Due to the pandemic, we have included…