Press release
Guyson RXS1400 Automated Blast System for High Productivity Metal Finishing
Guyson International, the UK’s foremost industrial finishing equipment manufacturer, has recently added the Guyson Multiblast® RXS1400 automated blast system to its portfolio of Rotating indeXing Spindle systems. Ideally suited for the complete surface treatment of components that can be blast finished or shot-peened whilst rotating about one axis. Guyson's largest standard indexing system can handle components with a maximum component size of 400 mm height x 400 mm diameter and a weight of 25 kg. The blast system is perfect for medium to high volumes of automotive transmissions, aerospace and land-based turbine components, railway, wind and construction equipment and substrate materials in metal, composite or exotic alloys.The Guyson Multiblast RXS1400 machine is a six spindle rotating indexing blast system that can process multiple parts simultaneously; having two blast stations, making it extremely suitable for high volume manufacturing. The six work spindles are equally spaced around the perimeter of the rotary indexing table and arranged so that at all times two of the spindles are outside the blast machine during the blasting operation for loading and unloading. Due to the rapid table indexing of the RXS1400, the load/unload environment is generally protected with a light-guard failsafe safety device.
Guyson International's Sales Manager, Ian Rayner, states that “The RXS1400 blast system is a great new addition to our already extensive range of automated blast solutions, which also includes the smaller RXS400 and 900 options, RSB rotary table machines, T40 & T50 tumble basket and in-line tunnel blast machines. This new equipment can be specified as either suction fed or pressure fed with the choice being directed by the application and throughput requirements.“
Parts are loaded onto the left-hand spindle and enter the blast chamber via pneumatic sliding doors. These open and close automatically, to allow components to enter and exit the machine; and are interfaced with the table indexing mechanism. The doors also create a seal during the blast operation to prevent media and noise from escaping to the work environment.
Inside the blast chamber, the dual blast station design can feature fixed or vertically traversing guns to provide optimum blast coverage and reduced TAKT times compared to manual blasting. The two rotating spindles present the components, in sequence, in front of the blast nozzles at each of the two blast stations. This ensures uniform coverage for a superior, repeatable, controlled finish required by industries such as Aerospace, Automotive and Medical.
After blasting, components enter a post-blast airwash chamber where compressed air is directed at them to remove any residual dust or blast media and are ready for the next stage of production.
Blasting can be either suction or pressure fed – as on all Guyson automated blast equipment. If pressure fed, with high component volumes, blasting is delivered through a pressure pot, often a twin-chamber pot (300 litres), allowing for a continuous flow for prolonged blast periods. Blast media being fed from the base of the pressure pot into the cabinet via a heavy-duty hose to the blast nozzles. High/low media-level sensors monitor the level of blast media within the pressure pot and a media reservoir above the pot keeps the pressure pot replenished with media when required without interruption.
After blasting, the used blast media is extracted via a Guyson cyclone reclamator which separates the re-usable blast media from dust, blast debris and undersized media. In some applications, when using a dense metallic blast media, the cyclone reclamator is replaced by an auger screw and bucket elevator.
Options also exist for media conditioning and monitoring, which include vibrating sieve media size control, media roundness classifiers, and electronic shot flow control. These are often essential for applications with demanding quality standards such as the Aerospace shot peening standard AMS 2432. The extraction system is completed with a selection of cartridge dust collection units matched to the machine and media volumes.
The entire blast system is controlled via a PLC/ ‘Graphic Operator Terminal’ (GOT), with a full-colour display screen, which facilitates repeatable blast settings to be simply stored and retrieved in quick access menu systems.
The prospective user of Guyson automated blast systems is encouraged to submit sample components for free feasibility testing to the company’s extensive ‘Component Finishing Centre’ at Skipton, England.
Guyson International Limited
Snaygill Industrial Estate, Keighley Road,
SKIPTON, North Yorkshire, England BD23 2QR
Guyson International Limited is a privately owned family company with a worldwide reputation for excellence in the design and manufacture of blast finishing, spray wash and ultrasonic cleaning equipment. Formed over eighty years ago, the company is registered to ISO 9001: 2015 and ISO 45001:2018, and its head office is located at Skipton, North Yorkshire, in the north of England. Guyson has four international subsidiary companies: Guyson Corporation of the USA, located in Saratoga Springs, New York State; Guyson SA, situated near Paris, France; Guyson Sdn Bhd in Penang, Malaysia; and Guyson CN, in Wuxi, Jiangsu Province, China.
This release was published on openPR.
Permanent link to this press release:
Copy
Please set a link in the press area of your homepage to this press release on openPR. openPR disclaims liability for any content contained in this release.
You can edit or delete your press release Guyson RXS1400 Automated Blast System for High Productivity Metal Finishing here
News-ID: 2521959 • Views: …
More Releases from Guyson International Ltd
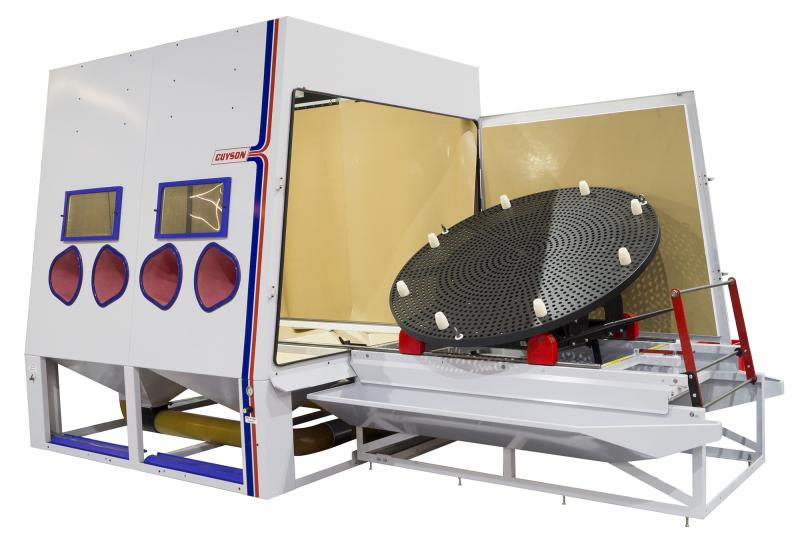
Extra-Large Blast Machine for Blast Etching Aerospace Rings
Guyson International, the UK's foremost industrial finishing equipment manufacturer, has installed a Guyson Euroblast® 2-metre PF (Pressure Fed) blast system into a division of a leading European aerospace company. The extra-large blast cabinet is used to deliver a uniform etched key surface on a range of machined circular aluminium rings prior to bonding.
After blast trails performed at the company's Skipton demonstration centre, a Euroblast 2-metre PF blast system (2.1…
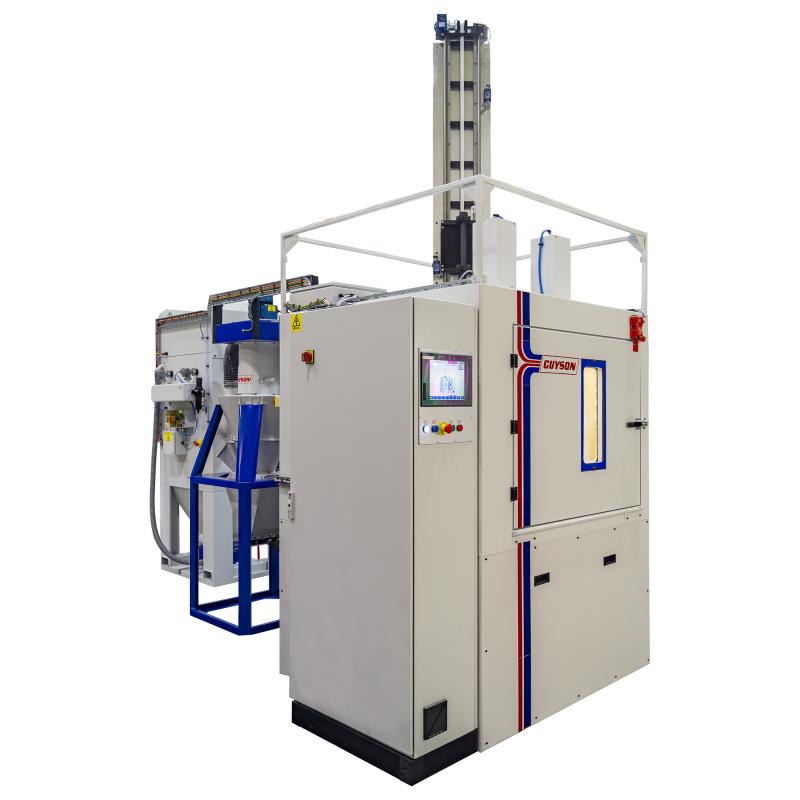
Guyson Twin Spindle Blast Machine for Etching Tubular Components
Guyson International, the UK's leading manufacturer of industrial finishing equipment, has recently manufactured and installed into a UK manufacturing company an automated Multiblast RSB twin spindle blast system for externally blast etching various sizes of tubular components. This new blast system incorporates two rotating blast stations with matching top clamps, to hold the product securely, whilst two vertically traversing blast guns produce a uniform blast etch finish over the length…
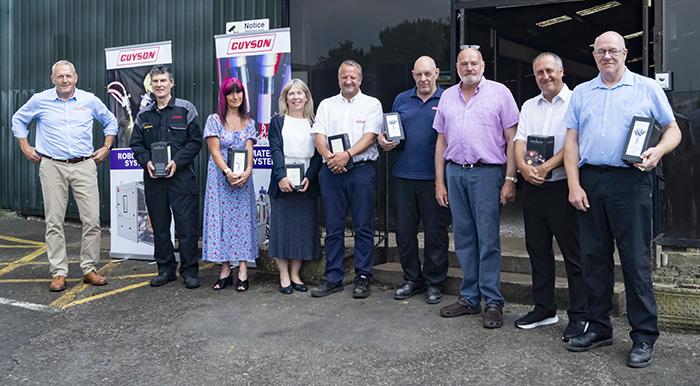
Guyson Staff Clock-Up 180 Years!
At Guyson International's Skipton headquarters, Monday 15th August saw rain, much needed, and celebrations, much deserved. Employees from the company's blast and wash division gathered outside to congratulate seven employees who were awarded long service awards. And between them amassed a total of 180 years of service at Guyson, with one, Keith Miller celebrating 50 years of service.
In typical unpredictable UK weather, after so many days of bright hot sunshine,…
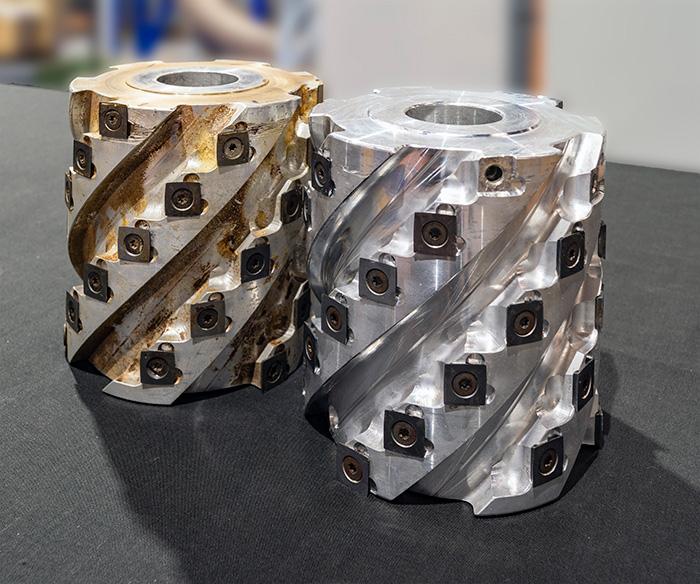
Guyson Equipment Cleans and Maintains Planing and Woodcutting Tools
Guyson International, one of the UK's leading manufacturers of industrial finishing equipment, recently delivered a KS450 ultrasonic cleaning tank and a Formula 1200 benchtop bead blast cabinet to RHW (R H Wilson (Lakes) Ltd.) of Kirkby Stephen, a leading timber importer and supplier, for cleaning and maintaining their wood cutting and planing tools.
The problem was how best to clean 'helical planer blocks' to remove a build-up of pitch, sap, resin…