Press release
Advanced production process and composite materials meet sustainable mobility: shuttle Olli 2.0 uses some Windform parts 3D-printed by CRP Technology
For Local Motors’ autonomous electric vehicle Olli 2.0, Italy-based CRP Technology manufactured two applications using Windform composite materials. As additions to the original Olli 2.0 model, the 3D printed parts have supported the individual approval for a project in EuropeThe ground mobility company Local Motors’ autonomous electric vehicle Olli 2.0 includes some 3D printed parts manufactured by CRP Technology in Windform composite materials.
The Modena-based company, which has been involved in professional 3D printing with Windform composite materials since 1996, was contacted by the EMEA management of Local Motors to build some parts mandatory in order to obtain individual approval for Europe.
Carlo Iacovini, General Manager EMEA, Local Motors, states, “Olli is operating in campuses, stadiums, industrial districts and local communities around the world. To approve deployments in Europe, it needed some additional components, not required in US market.”
Among them, there were the windshield wipers and parts.
Challenge
“To add the wipers – Iacovini says - we opted for the retrofit technique, or re-adaptation process, through an integration on the 2.0 model. We started from the original project, and we adapted it to our needs. These phases (retrofit and integration) were carried out in Italy, based on the original design produced by the Engineering Team in Chandler.”
It’s been a demanding job, since Olli 2.0 ’s unique design is characterized by a tall rectangular pod with wide-set headlights and expansive windows nestled between a frame.
“That’s exactly the reason why - adds Iacovini - the wipers arm could not be positioned from above, but from the below side of the front window. Thus, the Local Motors’ Engineering Department designed a new front bumper with brackets for fixing both the wipers starter motor and the front wiper washer reservoir.”
During the wipers assembly phase, the Local Motors Engineering Team noticed that the motor protruded from the modified front bumper: “To avoid the issue we therefore thought - comments Iacovini - to add two coordinated covers, with the purpose of concealing the protruding part (the first cover) and protecting the pressure system of the washer reservoir from external agents (the second cover).”
The Local Motors team designed the motor cover from scratch.
“For the wipers washer reservoir flap valve - Iacovini specifies – we modified and adapted the design of the flap valve of the charging socket on Olli 2.0’s rear bumper. In this way we maintained homogeneity from the design point of view, and we positioned the water flap valve symmetrically to the charging one.”
Once identified the parts to manufacture - the motor cover and the washer reservoir flap valve of the wipers system - Local Motors turned to CRP Technology: “We wanted to collaborate - states Iacovini - with an European firm, therefore we contacted CRP Technology, a company I have known for a long time and with which I have collaborated on relevant projects.
Relying on CRP was the winning choice: the uniqueness of Windform materials in terms of quality and strength allow achieving optimal results in a short time.”
After a careful study of the projects, CRP Technology experts opted to create the parts using professional 3D printing / Powder Bed Fusion process with composite polymers fibers-reinforced (also known as Selective Laser Sintering) and two materials from the Windform® TOP-LINE range: The polyamide-based composite material Windform XT 2.0 Carbon fiber reinforced for the wipers starter motor cover (component with mainly aesthetic purpose, but also functional, able to contain / support the oscillatory movement of the motor); and the polyamide-based composite material Windform LX 3.0 Glass fiber reinforced for the washer reservoir flap valve (component with mainly functional purpose, and partly aesthetic).
Result
Wipers starter motor cover
It is a rectangular part in Windform XT 2.0 material, a sort of protruding oblique parallelepiped with a puncture for the placement of the wipers arm and a smaller one for the water hose.
The main function of the part is aesthetic, but considering its position (next to the motor) it has to: guarantee electromagnetic compatibility, resist the oscillating movement of the wiper arm and blade, withstand the continuous stress and vibrations caused by the traffic circulation on roads, preserve the electrical unit from external agents. For these reasons, the part needed to be made of a material that would provide stiffness and strength combined with high lightness, ensuring the creation of an accurate, reliable and durable application. Windform® XT 2.0, one of the top-of-the-range materials from the Windform TOP-LINE for its mechanical properties, and representing a perfect choice for functional applications, was therefore chosen.
Wipers washer reservoir flap valve
The component, in Windform LX 3.0, consists of a rectangular structure frame and the flap valve equipped with magnets to access the wipers washer reservoir. Its main purpose is to ensure quick access to the wipers washer reservoir positioned behind, to protect it from external agents and to resist the continuous stress and vibrations caused by the traffic circulation on roads. Furthermore, it also has to be accurate in detail. It therefore needed to be manufactured in a material that guaranteed reliability, good resistance and aesthetic return: Windform LX 3.0 was chosen for its excellent properties and the wide spectrum of use.
After manufacturing the parts, CRP Technology carried out the final tests and delivery.
Then a Local Motors’ supplier installed them on Olli without encountering any mounting and fixing issues.
Afterwards Local Motors conducted on the “modified” Olli some electromagnetism tests in the anechoic chamber. The EMC testing concerned the whole windshield wipers with excellent results. No critical issues were proposed in regard to the 3D printed parts in Windform composites.
crptechnology.com
windform.com
Veronica Negrelli
Press Office Manager
CRP Technology
Via Cesare Della Chiesa, 150/C
41126 Modena
ITALY
CRP Technology (Modena, Italy) has revolutionized the Additive Manufacturing world by introducing its proprietary high performance composite materials Windform®, now used by the most advanced industry sectors for functional prototypes and end use parts. CRP Technology is distinguished by its know-how in Powder Bed Fusion process with composite polymers fibers-reinforced. It offers part production for short- and low-run production, and prototyping services with Windform®. Its specific application fields including but are not limited to: automotive and motorsports, design, aerospace, UAVs, marine, entertainment, defense, and packaging. CRP Technology also sells to OEMs the Windform range of composite materials for professional 3D Printing.
This release was published on openPR.
Permanent link to this press release:
Copy
Please set a link in the press area of your homepage to this press release on openPR. openPR disclaims liability for any content contained in this release.
You can edit or delete your press release Advanced production process and composite materials meet sustainable mobility: shuttle Olli 2.0 uses some Windform parts 3D-printed by CRP Technology here
News-ID: 2503767 • Views: …
More Releases from CRP Technology

CRP Technology Introduces Vapor Smoothing to Boost Surface Quality and Performan …
The Italy-based company specializing in 3D printing services has expanded its suite of production and post-processing capabilities, offering clients a fully integrated process from additive production to final inspection. Vapor smoothing can be applied to stand-alone Windform parts or following manual finishing, further enhancing the already high-performance characteristics of Windform materials.
Modena, Italy, 25 November 2024 - CRP Technology, a leader in advanced 3D printing services, has introduced vapor smoothing into…
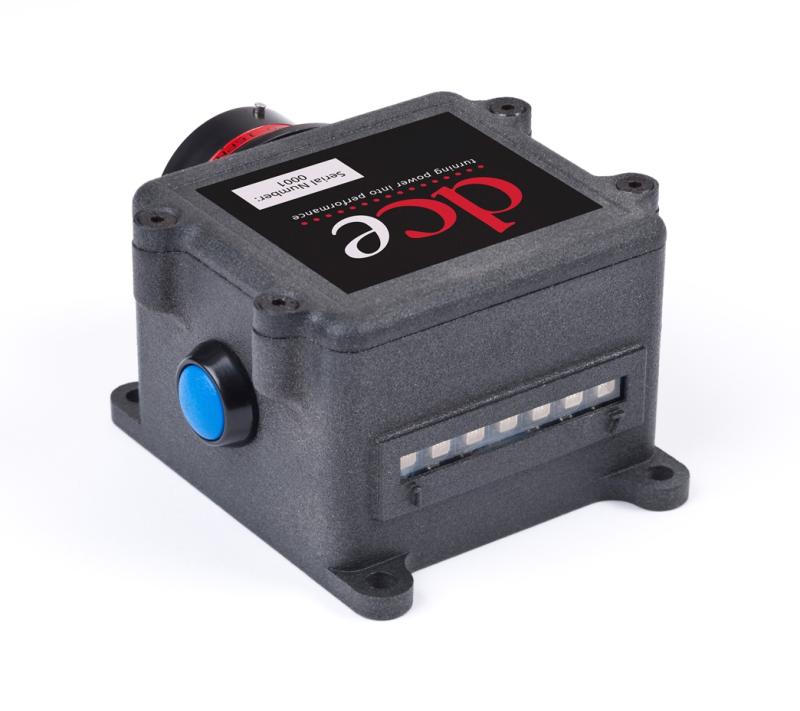
Excellent Electrical Insulation Performance for Windform Composites
3D printing service bureau CRP Technology's Glass fiber reinforced Windform thermoplastic composites were subjected to dielectric constant and dielectric strength tests, and the results were excellent, exhibiting a dielectric constant of approximately 4 and withstanding peak voltages of at least 2.5 kV/mm.
3D printing service bureau CRP Technology is pleased to inform that their Glass fiber reinforced Windform thermoplastic composites for Selective Laser Sintering, have demonstrated outstanding electrical insulation performance as…
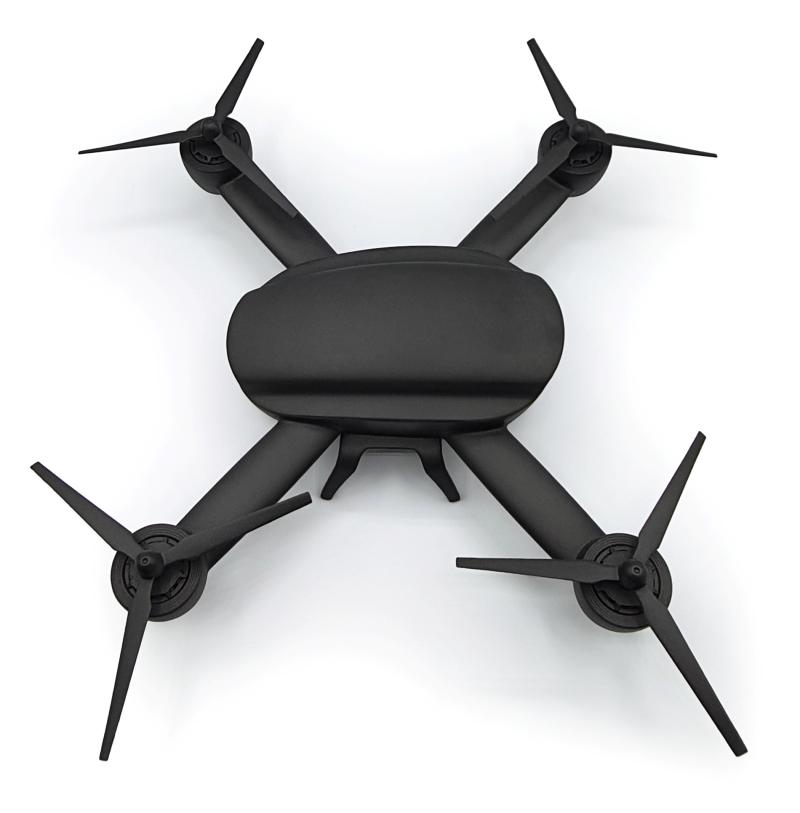
3D Printing Service Bureau CRP Technology Launches Windform SL, the Top-of-the-L …
CRP Technology, a pioneering company in the 3D printing industry and a leading 3D printing service bureau, introduces Windform SL, the twelfth material in the Windform TOP-LINE series, setting new standards in additive manufacturing. Windform SL, a polyamide-based composite reinforced with Carbon fibers, combines exceptional lightweight characteristics with a low density of 0.87 g/cc, making it an ultra-light and rigid material.
In the rapidly evolving field of Additive Manufacturing, the globally…
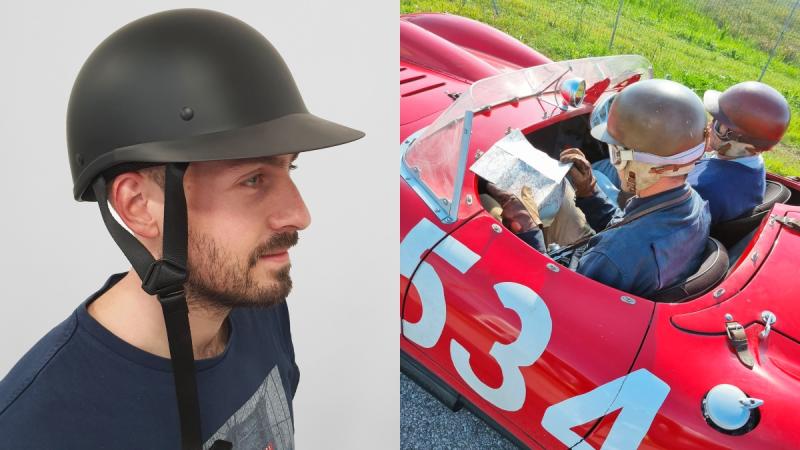
CRP Technology's Role in Industrial 3D Printing for Michael Mann's Film, "Ferrar …
Nestled in the soul of Modena, a city echoing with the thunderous symphony of engines and steeped in the storied tradition of automotive prowess, the eclectic and innovative filmmaker Michael Mann assumed the directorial helm to breathe life into the enthralling saga of Enzo Ferrari, the mastermind behind Ferrari cars.
Drawing inspiration from Brock Yates' seminal 1991 biography, "Enzo Ferrari: The Man and the Machine", Mann's new cinematic masterpiece, "Ferrari"…
More Releases for Windform
Excellent Electrical Insulation Performance for Windform Composites
3D printing service bureau CRP Technology's Glass fiber reinforced Windform thermoplastic composites were subjected to dielectric constant and dielectric strength tests, and the results were excellent, exhibiting a dielectric constant of approximately 4 and withstanding peak voltages of at least 2.5 kV/mm.
3D printing service bureau CRP Technology is pleased to inform that their Glass fiber reinforced Windform thermoplastic composites for Selective Laser Sintering, have demonstrated outstanding electrical insulation performance as…
Windform RS and Windform LX 3.0 officially approved for space flight
Carbon fiber reinforced composite Windform RS and Glass fiber reinforced composite Windform LX 3.0 from CRP Technology's Windform TOP-LINE, passed ESA standard screening outgassing tests in accordance with ESA-TEC-PR-002015 (based on ECSS-Q-ST-70-02C): they are officially approved for the construction of applications to launch into Space.
Franco Cevolini, CEO and Technical Director of CRP Technology, says: "Passing the outgassing tests is a crucial factor for those who supply materials to the…
Windform® RS, the outstanding composite material with amazing mechanical proper …
CRP Technology launches a new polyamide-based Carbon fiber filled composite for production-grade PBF 3D printing: the top-of-the-range Windform® RS. Engineer Franco Cevolini, CEO and CTO, CRP Technology: "In the Additive Manufacturing world Windform® RS is unparalleled. We created a material that combines high tensile strength with high elongation at break and low density: Windform® RS is unique of its kind"
CRP Technology, a leading 3D printing company, announces the…
3D printed satellite deployer in Windform XT 2.0 acclaimed for its mechanical fe …
Recently Alba Orbital’s AlbaPod V2 hyped up for its unique design, lightweight, easily integration into space launch vehicles, maintenance of the demanding quality standards for space. These characteristics have also made possible thanks to the use of AM and Windform XT 2.0 Carbon composite material
The European Space Agency (ESA) dedicated an article on Alba Orbital's cutting edge 3D printed satellite dispenser, AlbaPod V2, manufactured by CRP Technology using laser sintering…
CRP Windform FR2, new cutting-edge composite material for Additive Manufacturing
CRP Technology, the long-standing leading company in the field of advanced technologies and professional 3D printing, launches on the market a flame-retardant glass fiber reinforced material for Selective Laser Sintering
CRP Technology's hi-tech advancement is unstoppable. Less than six months after the launch on the market of Windform FR1, the first carbon fiber-reinforced flame-retardant material for professional 3D printing, CRP Technology is presenting a new composite material from the TOP-LINE family…
CRP Technology launches Windform® P2, thermoplastic glass fiber filled material …
CRP Technology, a leading company in the creation of prototypes and final applications in professional 3D printing, launches Windform® P2 material.
Windform® P2 is a glass fiber reinforced thermoplastic polyamide material with excellent mechanical properties for High Speed Sintering process.
Engineer Franco Cevolini, CRP Technology CTO and VP, states: “Windform® P2 is the second polymer from P-LINE, the new Windform® range of materials for high speed production-grade 3D printing, introduced on the…