Press release
Combined pharmaceutical freeze drying service proves a success in China for GEA Lyophil
It was in November 2010 that GEA Pharma Systems acquired Beijing Sino-German Tianhe Technology in Beijing to create GEA Lyophil (Beijing) Ltd. Since then, the company has quadrupled turnover and enhanced its customer service by blending German quality and Chinese economy to provide a unique combined offering to its pharmaceutical clients.Jinbin Tang, MD, GEA Lyophil (Beijing) Ltd. said that the market had changed in China since the introduction of new requirements for GMP production. This had increased the requirement for high quality pharmaceutical freeze drying lines, especially in combination with ALUS® (Automatic Load and Unload Systems), a technology in which GEA Lyophil in Germany are a recognised world authority.
“The key for us is to make sure we use the facilities and talents of the Chinese and German manufacturing centres fully,” he explained. “We have made freeze drying machines in China for many years however it is GEA Lyophil, Germany that is the true master of ALUS®. By combining both technologies, we have the ability to provide our customers with complete, cost-effective GMP production lines with the quality and security of outcome that would be expected from a German manufacturer.”
Heinrich Meintrup, Managing Director of GEA Lyophil in Germany agreed. “Having this combined option allows us to blend the benefits of German quality with a more cost-effective approach. We have never been willing to play the ‘low cost’ game, it just doesn’t work, but this quality / price performance model makes our offering unique.”
The main markets for GEA Lyophil in China come from the pharmaceutical companies who recognise that they need to use recognised, top-quality equipment to compete on their local market as well as on a world export stage. “Most of our customers are making anti-cancer drugs, antibiotics or expensive biological products where top quality, security of outcome and reliable containment are essential,” said Jinbin Tang. “They consider our lines to represent the image of their companies.”
Since 2010, this approach has allowed GEA Lyophil (Beijing) Ltd. to quadruple its turnover and expand its customer base to include the top-end customers that require leading technology and also provide the economy necessary for those that do not have such critical requirements. Although China is beginning to suffer from less rapid growth than in recent years both Jinbin Tang and Heinrich Meintrup are optimistic about the outlook in China. “We expect another big jump this and next year because of the new GMP regulations,” said Jinbin Tang. “Beyond that we still expect above average growth from the pharmaceutical sector.”
One product that is proving very popular in China is the GEA Lyophil range of price competitive pharmaceutical freeze dryers SMART LYO®: a system that is based on modular units that have been made using proven technology and our excellent China manufacturing skills and techniques. This keeps the cost down without compromising quality, performance or system architecture / flexibility; makes validation and documentation easier; and reduces delivery times.
GEA Pharma Systems unites the technologies of Aeromatic-Fielder™, Buck™, Collette™, Courtoy™, Diessel™, and Lyophil™ to provide advanced one-stop solutions for solid and liquid dosage processing to the global pharmaceutical industry.
All editorial enquiries to:
Steve Jordan
The Words Workshop
Tel: +44 1908 695500
Email: steve@thewordsworkshop.co.uk
www.thewordsworkshop.co.uk
For further business information contact:
Hubert Kluetsch - Director Sales and Marketing
GEA Lyophil GmbH
Kalscheurener Str. 92 50354 Huerth Germany
Tel: +49 (0) 2233/6999-220 Fax: +49 (0) 2233/6999-8220
E-mail: lyophil@gea.com
Web: www.geapharmasystems.com
Jinbin Tang
Managing Director
GEA Lyophil (Beijing) Ltd.
No. 186 Shuangiiafen
Wangsiying
Chaoyang District, Beijing.
Tel: +86 10 87394872
Fax: +86 10 87393755
Email: Jinbin.tang@gea.com
This release was published on openPR.
Permanent link to this press release:
Copy
Please set a link in the press area of your homepage to this press release on openPR. openPR disclaims liability for any content contained in this release.
You can edit or delete your press release Combined pharmaceutical freeze drying service proves a success in China for GEA Lyophil here
News-ID: 231579 • Views: …
More Releases from GEA Pharma Systems
Janssen Pharmaceutica teams up with GEA Pharma Systems to investigate continuous …
Janssen Pharmaceutica, part of the worldwide Janssen Pharmaceutica Group, has initiated a global project with the aim of evaluating technical performance and related business benefits of continuous processing technologies for oral solid dosage forms. In this context, ConsiGma™ continuous processing technology from GEA Pharma Systems has been assessed for tablet manufacture. During an in-depth feasibility study at GEA Pharma Systems’ lab, the team from Janssen has been able to…
GEA Pharma Systems presents European granulation, drying, tableting and fermenta …
GEA Pharma Systems will be exhibiting at CHINA-PHARM 2012 from 24 to 27 September at the China National Convention Center in Beijing. Exhibits on stand number 3017 will include examples of the company’s range of Aeromatic-Fielder™ and Collette™ granulation and drying plant; MODUL™ tablet presses from Courtoy™; and pharmaceutical fermentation systems from GEA Diessel showing state-of-the-art technology for a bioreactor vessel.
On 25 September the company will present a…
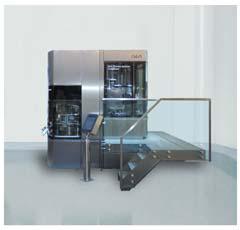
GEA Pharma Systems wins large order for continuous solid dose processing from ma …
GEA Pharma Systems has announced an agreement with a US pharmaceutical company to supply a complete continuous processing line for the production of solid dose drugs. The order is one of the more significant for ConsiGma™ oral solid dosage continuous processing equipment and represents the first phase of a potentially long-term commitment for this customer. Delivery is scheduled for early 2013.
The order is to deliver a continuous solid…
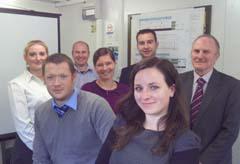
Leading contract manufacturer Penn Pharma in UK has chosen GEA Pharma Systems as …
GEA Pharma Systems has secured a high value order for processing equipment with Penn Pharma based in Tredegar in South Wales. The new equipment will significantly increase the pharmaceutical contract manufacturer’s production capacity and allow it to provide a single source for high containment development and manufacture of highly potent drugs for its international customers.
Penn Pharma believes that the new production plant will give it a leading position…
More Releases for Lyophil
GEA Lyophil: saving time and money … improving yield and quality – at ACHEMA …
GEA Lyophil, GEA’s pharmaceutical freeze drying specialist, will be mixing established technology and cutting edge innovation on the GEA Pharma Systems stand at ACHEMA 2012. All the GEA Lyophil technology has proven its ability to improve yields, enhance quality, save money and time, and help pharmaceutical companies to unleash their product potential.
Nucleation On-Demand Technology
With ControLyo®, GEA Lyophil has added nucleation on-demand technology to its pharmaceutical freeze drying range to…
Liquid and Solid dosage innovation in compression, containment and continuous pr …
GEA Pharma Systems will be demonstrating its solid dosage innovation in the areas of compression, containment and continuous processing at ACHEMA 2012 in Frankfurt from 18-22 June. Exhibits will include the new bi-layer conversion system for the high-volume Performa™ P tablet press; the range of improved Buck® valves including the MC valve and Hicoflex®; the hugely successful and versatile FlexStream™ fluid bed technology; and the revolutionary concept of ConsiGma™…
LYOPLUS® – multipurpose measurement device for pharmaceutical freeze dryers f …
One of the world’s biggest pharmaceutical companies has recently embarked on a long-term evaluation programme for the LYOPLUS® mass spectrometer from GEA Lyophil to provide essential data from within the freeze dryer itself. The company has confirmed a number of benefits of the LYOPLUS® system including: the ability to detect very small silicone oil leaks inside the dryer; the ability to monitor the moisture content within the freeze drying…
GEA Diessel reinforces its strong Japanese presence at Interphex 2011
GEA Diessel further strengthened its market position in the Japanese pharmaceutical market with its attendance at Interphex in Tokyo this July. The show, claimed to be Asia’s biggest pharmaceutical exhibition, allowed GEA Diessel the opportunity of renewing existing relationships while taking new enquiries for its advanced fermentation technology. The GEA staff on the stand reported Interphex 2011 to be equal to previous years with over 1500 companies exhibiting and…
Visitors from around the world attend GEA Lyophil open-house seminars during Int …
Visitors to the Interpack 2011 exhibition in Dϋsseldorf were given the opportunity to attend a series of special in-house seminars presented by pharmaceutical freeze dryer manufacturer GEA Lyophil. The theme of the seminars held on May 13, 14 and 17 was ‘total cost of ownership’ and focused on the reduction of direct and indirect costs in relation to the freeze drying process.
Fifty delegates from 18 countries attended the seminars at…
VAPOVAC™ : new FDA compliant H2O2 sterilisation system for pharmaceutical Lyop …
VAPOVAC™ the latest technology for H2O2 gas sterilisation of pharmaceutical freeze dryers from GEA Lyophil, has recently received a Letter of Non-Objection from the US Food and Drugs Administration (FDA).
The FDA Letter of Non-Objection has now cleared the way for GEA Lyophil to market the VAPOVAC™ system worldwide. The system is ideally suited to pharmaceutical applications that require sterile conditions without the stresses and high power usage associated with…