Press release
B-Napthol Production Cost Analysis 2025: A Detailed Guide from Capital to Commissioning
Beta-Naphthol (B-Napthol) is an organic aromatic compound derived from naphthalene, commonly used as an intermediate in the production of azo dyes, pigments, antioxidants, and rubber chemicals. It appears as a white to reddish crystalline solid and is known for its chemical reactivity, particularly in coupling reactions with diazonium salts to form vivid dyes. Due to its versatility, B-Naphthol is widely used in the textile, pharmaceutical, agrochemical, and plastic industries.Setting up a B-Naphthol production plant involves sourcing naphthalene, installing sulfonation and alkaline fusion units, along with filtration and drying systems. Moderate investment and strict adherence to environmental norms are essential for a safe and efficient operation.
IMARC Group's report, titled "B-Napthol Production Cost Analysis 2025: Industry Trends, Plant Setup, Machinery, Raw Materials, Investment Opportunities, Cost and Revenue," provides a complete roadmap for setting up a b-napthol production plant. It covers a comprehensive market overview to micro-level information such as unit operations involved, raw material requirements, utility requirements, infrastructure requirements, machinery and technology requirements, manpower requirements, packaging requirements, transportation requirements, etc.
Request for a Sample Report: https://www.imarcgroup.com/b-napthol-manufacturing-plant-project-report/requestsample
B-Napthol Industry Outlook 2025
The B-Naphthol industry is expected to witness steady growth through 2025, driven by its extensive use in the manufacture of azo dyes, pigments, and other specialty chemicals. As global demand rises for colorants in textiles, plastics, inks, and coatings, the need for high-purity intermediates like B-Naphthol is increasing. Additionally, its role in rubber chemicals and agrochemical formulations contributes to its industrial relevance. Environmental regulations and a shift toward sustainable and low-toxicity alternatives may influence production technologies, pushing manufacturers toward cleaner, more efficient processes. Innovation and compliance will remain key drivers of competitiveness in the evolving B-Naphthol market.
Key Insights for setting up a B-Napthol Production Plant
Detailed Process Flow
• Product Overview
• Unit Operations Involved
• Mass Balance and Raw Material Requirements
• Quality Assurance Criteria
• Technical Tests
Estimate Plant Setup Cost Now: https://www.imarcgroup.com/capex-calculator
Project Details, Requirements and Costs Involved:
• Land, Location and Site Development
• Plant Layout
• Machinery Requirements and Costs
• Raw Material Requirements and Costs
• Packaging Requirements and Costs
• Transportation Requirements and Costs
• Utility Requirements and Costs
• Human Resource Requirements and Costs
Capital Expenditure (CapEx) and Operational Expenditure (OpEx) Analysis:
Project Economics:
• Capital Investments
• Operating Costs
• Expenditure Projections
• Revenue Projections
• Taxation and Depreciation
• Profit Projections
• Financial Analysis
Profitability Analysis:
• Total Income
• Total Expenditure
• Gross Profit
• Gross Margin
• Net Profit
• Net Margin
Key Cost Components
• Raw Materials:
The largest cost component, raw materials include naphthalene, sulfuric acid, caustic soda, and other chemical reagents. Naphthalene, derived from coal tar or petroleum, accounts for a significant portion of the input cost due to its price volatility and dependency on crude oil markets.
• Utilities:
Energy consumption is considerable in the production of B-Naphthol, especially for heating, distillation, and drying processes. Costs related to electricity, steam, and water usage represent a notable share of operating expenses.
• Labor Costs:
Manufacturing involves skilled and semi-skilled labor, particularly in maintaining quality control and handling chemical reactions. Labor expenses vary by geographic location and the degree of automation in the production facility.
• Manufacturing Overheads:
This includes maintenance of equipment, depreciation, safety compliance measures, waste treatment systems, and administrative expenses. Regulatory compliance costs, especially related to environmental and chemical safety standards, are increasingly significant.
• Packaging and Storage:
B-Naphthol requires specialized packaging to prevent contamination and ensure safety during transportation. Storage costs may include climate control and inventory handling systems, especially in bulk operations.
• Transportation and Logistics:
The costs of moving raw materials to the production site and finished goods to end-users or distributors contribute significantly to total production costs. This includes freight charges, fuel costs, and logistics management.
• Taxes and Duties:
Import duties on raw materials, local taxes, and compliance fees may impact the final cost structure. These vary by country and trade agreements.
• Research and Development (R&D):
While typically a smaller proportion, R&D investments in process optimization, yield improvement, and environmental compliance can influence the overall cost structure, especially for producers focused on efficiency and sustainability.
Economic Trends Influencing Ferrous B-Napthol Plant Setup Costs 2025
• Volatility in Raw Material Prices:
The cost of key inputs such as naphthalene, caustic soda, and ferrous salts remains sensitive to fluctuations in crude oil prices and global petrochemical supply chains. Any sustained increases in raw material prices will directly elevate capital planning and procurement costs for new plant setups.
• Rising Energy and Utility Costs:
Energy-intensive operations in B-Naphthol production face pressure from escalating electricity and fuel costs. In 2025, the global push toward decarbonization and the introduction of carbon pricing mechanisms in several regions may further increase utility expenses, impacting setup decisions and long-term operational planning.
• Environmental Compliance and Regulatory Costs:
Environmental regulations continue to tighten, especially concerning effluent treatment, hazardous waste disposal, and air emissions. Complying with these standards requires investment in pollution control technologies and sustainable process design, which adds to the capital expenditure for plant setup.
• Geopolitical and Trade Uncertainties:
Ongoing geopolitical tensions, including trade restrictions on chemicals and raw materials, can influence the availability and pricing of essential components. Additionally, shifts in tariff structures or trade policies in key manufacturing regions (such as China and India) may alter the cost-benefit analysis for new plant locations.
• Shift Toward Localized Supply Chains:
As global supply chains become more regionalized in response to logistics disruptions and policy shifts, companies are prioritizing local production to mitigate risk. This may lead to higher setup costs in regions with less established infrastructure but long-term benefits in supply security.
• Financing Costs and Interest Rate Trends:
Global monetary policy in 2025 continues to grapple with inflationary pressures. Elevated interest rates increase the cost of capital for industrial projects, making plant financing more expensive and potentially impacting the feasibility of new setups.
• Technological Advancements and Automation:
Incorporating advanced manufacturing systems, process automation, and digital monitoring tools into plant design can raise upfront investment but offer long-term cost efficiencies. The adoption of Industry 4.0 practices is becoming more prevalent, influencing capital allocation during the setup phase.
• Labor Market Dynamics:
Labor availability and wage trends in target geographies affect construction and commissioning costs. Skilled labor shortages in chemical engineering and industrial operations may drive up labor-related expenditures during the plant setup stage.
Speak to an Analyst for Customized Report:
https://www.imarcgroup.com/request?type=report&id=15355&flag=C
Challenges and Considerations for Investors
• Raw Material Price Volatility:
B-Naphthol production heavily depends on petrochemical derivatives such as naphthalene and sulfuric acid. Fluctuations in crude oil prices and supply chain disruptions can lead to inconsistent input costs, affecting profit margins and financial planning.
• Environmental and Regulatory Compliance:
Strict environmental regulations concerning chemical manufacturing and effluent discharge present significant compliance costs. Investors must consider capital expenditure on pollution control systems and ongoing operational costs associated with meeting national and international safety standards.
• Market Demand Uncertainty:
The demand for B-Naphthol is closely linked to the textile, pigment, and agrochemical sectors. Global economic cycles, changes in consumer preferences, or regulatory bans on certain dyes can impact end-use markets, affecting sales volumes and profitability.
• Technological Obsolescence:
Rapid advancements in green chemistry and process optimization pose risks to traditional production technologies. Investors need to ensure that plant designs incorporate flexible and scalable systems that can adapt to future process innovations and environmental standards.
• High Capital and Operational Costs:
Establishing a B-Naphthol production facility requires significant initial investment in infrastructure, safety systems, and skilled labor. Additionally, ongoing costs related to energy, maintenance, and logistics must be accurately projected and managed for sustained profitability.
• Supply Chain Disruptions:
Dependence on international suppliers for raw materials or equipment can expose investors to geopolitical risks, trade restrictions, and transportation delays. A robust procurement strategy and local sourcing options are critical for risk mitigation.
• Competitive Landscape:
The market includes both large multinational chemical producers and regional players, leading to pricing pressure and the need for product differentiation. Strategic positioning and quality consistency are essential for capturing and maintaining market share.
• Sustainability Expectations:
Increasing stakeholder focus on environmental, social, and governance (ESG) performance places pressure on chemical companies to adopt sustainable practices. Investments in cleaner production technologies and transparent reporting can influence investor perception and access to funding.
• Regulatory Approval Delays:
Obtaining licenses and permits for chemical manufacturing can be time-consuming and subject to bureaucratic hurdles. Delays in regulatory approval can impact project timelines and increase financial risk.
Conclusion
The B-Naphthol industry in 2025 presents promising opportunities supported by rising demand across the dye, pigment, rubber, and agrochemical sectors. However, establishing a production facility involves navigating significant challenges, including raw material volatility, regulatory compliance, and capital-intensive requirements. A thorough understanding of the cost structure, evolving economic trends, and market dynamics is essential for making informed investment decisions. With strategic planning, adoption of advanced technologies, and alignment with environmental standards, stakeholders can position themselves competitively in this growing but complex industrial segment.
Contact Us:
IMARC Group
134 N 4th St. Brooklyn, NY 11249, USA
Email: sales@imarcgroup.com
Tel No:(D) +91 120 433 0800
United States: +1-631-791-1145
About Us:
IMARC Group is a global management consulting firm that helps the world's most ambitious changemakers to create a lasting impact. The company excel in understanding its client's business priorities and delivering tailored solutions that drive meaningful outcomes. We provide a comprehensive suite of market entry and expansion services. Our offerings include thorough market assessment, feasibility studies, company incorporation assistance, factory setup support, regulatory approvals and licensing navigation, branding, marketing and sales strategies, competitive landscape, and benchmarking analyses, pricing and cost research, and procurement research.
This release was published on openPR.
Permanent link to this press release:
Copy
Please set a link in the press area of your homepage to this press release on openPR. openPR disclaims liability for any content contained in this release.
You can edit or delete your press release B-Napthol Production Cost Analysis 2025: A Detailed Guide from Capital to Commissioning here
News-ID: 4093754 • Views: …
More Releases from IMARC Group
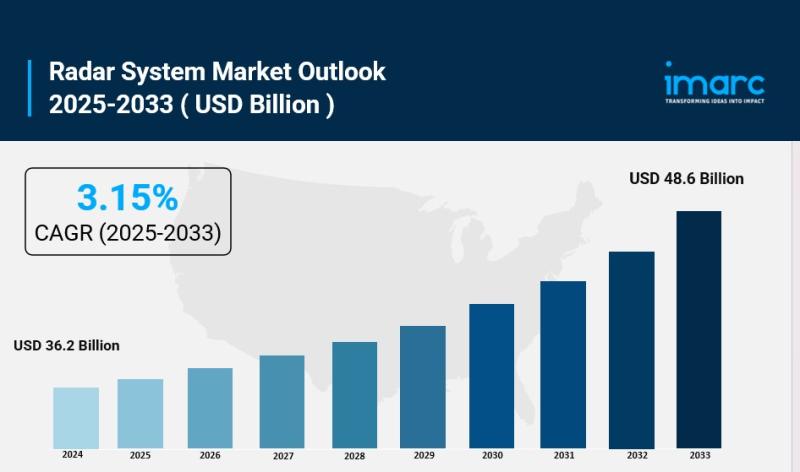
Radar System Market Size, Share, Growth And Forecast Report 2025-2033
Radar System Market Overview:
The radar system market is experiencing strong growth, driven by increasing demand for advanced surveillance, navigation, and safety solutions across defense, aerospace, automotive, and maritime industries. Radar systems are widely used for detecting objects, tracking movements, monitoring weather conditions, and ensuring security in both military and civilian applications. The rise in geopolitical tensions, rapid adoption of autonomous vehicles, and technological advancements such as phased-array, Doppler, and 3D…
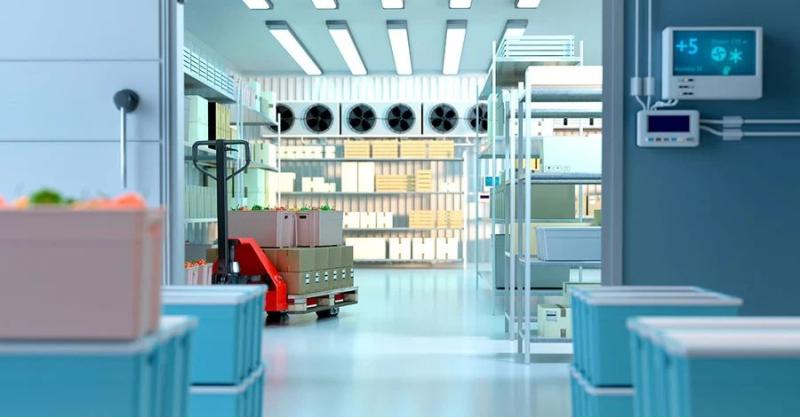
Cold Chain Logistics Market Valuation to Reach USD 932.70 Billion by 2033 - Indu …
Market Overview:
The cold chain logistics market is experiencing remarkable expansion, driven by the growing demand for temperature-sensitive products, rising consumer preference for fresh and frozen foods, and the pharmaceutical industry's need for specialized storage solutions. According to IMARC Group's latest research publication, "Cold Chain Logistics Market: Global Industry Trends, Share, Size, Growth, Opportunity and Forecast 2025-2033", the global cold chain logistics market size reached USD 292.06 Billion in 2024. Looking…
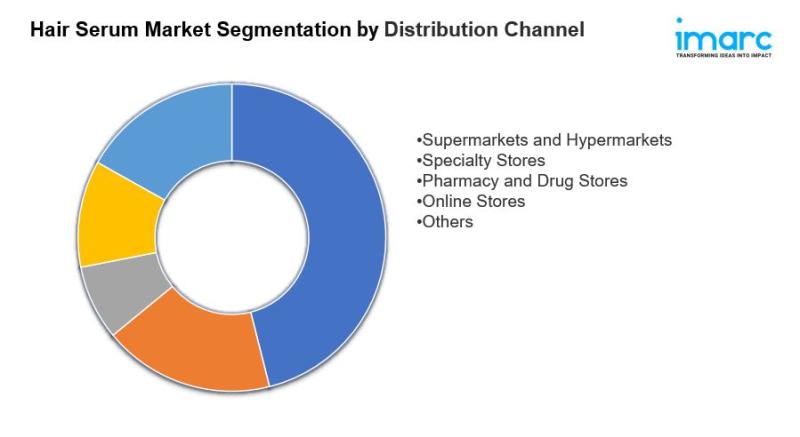
Global Hair Serum Market Size, Share And Trends Report 2025-2033
Hair Serum Market Overview:
The hair serum market is witnessing significant growth, driven by rising consumer awareness of hair care, increasing concerns over hair damage, and growing demand for multifunctional cosmetic products. Hair serums are lightweight, leave-in treatments formulated with active ingredients such as oils, silicones, and vitamins that provide benefits like frizz control, shine enhancement, heat protection, and nourishment. The surge in beauty and personal care spending, the influence of…
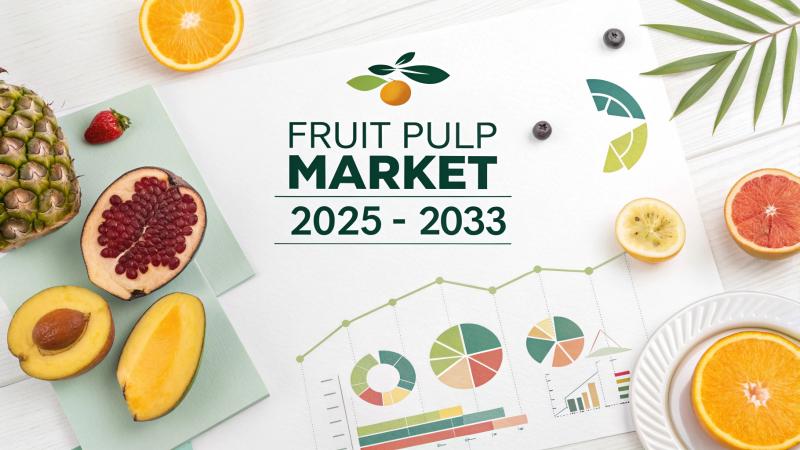
Fruit Pulp Market Valuation to Reach USD 2.11 Billion by 2033 - Industry Expandi …
Market Overview
The fruit pulp market is experiencing robust growth, driven by increasing demand for natural and organic food ingredients, expanding applications in the food and beverage industry, and rising health consciousness among global populations. According to IMARC Group's latest research publication, "Fruit Pulp Market: Global Industry Trends, Share, Size, Growth, Opportunity and Forecast 2025-2033", the global fruit pulp market size reached US$ 1.5 Billion in 2023. Looking forward, IMARC Group…
More Releases for Cost
Egg Powder Manufacturing Plant Setup Cost | Cost Involved, Machinery Cost and In …
IMARC Group's report titled "Egg Powder Manufacturing Plant Project Report 2024: Industry Trends, Plant Setup, Machinery, Raw Materials, Investment Opportunities, Cost and Revenue" provides a comprehensive guide for establishing an egg powder manufacturing plant. The report covers various aspects, ranging from a broad market overview to intricate details like unit operations, raw material and utility requirements, infrastructure necessities, machinery requirements, manpower needs, packaging and transportation requirements, and more.
In addition to…
Glucose Manufacturing Plant Cost Report 2024: Requirements and Cost Involved
IMARC Group's report titled "Glucose Manufacturing Plant Project Report 2024: Industry Trends, Plant Setup, Machinery, Raw Materials, Investment Opportunities, Cost and Revenue" provides a comprehensive guide for establishing a glucose manufacturing plant. The report covers various aspects, ranging from a broad market overview to intricate details like unit operations, raw material and utility requirements, infrastructure necessities, machinery requirements, manpower needs, packaging and transportation requirements, and more.
In addition to the operational…
Fatty Alcohol Production Cost Analysis: Plant Cost, Price Trends, Raw Materials …
Syndicated Analytics' latest report titled "Fatty Alcohol Production Cost Analysis 2023-2028: Capital Investment, Manufacturing Process, Operating Cost, Raw Materials, Industry Trends and Revenue Statistics" includes all the essential aspects that are required to understand and venture into the fatty alcohol industry. This report is based on the latest economic data, and it presents comprehensive and detailed insights regarding the primary process flow, raw material requirements, reactions involved, utility costs, operating costs, capital…
Acetaminophen Production Cost Analysis Report: Manufacturing Process, Raw Materi …
The latest report titled "Acetaminophen Production Cost Report" by Procurement Resource a global procurement research and consulting firm, provides an in-depth cost analysis of the production process of the Acetaminophen. Read More: https://www.procurementresource.com/production-cost-report-store/acetaminophen
Report Features - Details
Product Name - Acetaminophen
Process Included - Acetaminophen Production From Phenol
Segments Covered
Manufacturing Process: Process Flow, Material Flow, Material Balance
Raw Material and Product/s Specifications: Raw Material Consumption, Product and Co-Product Generation, Capital Investment
Land and Site Cost: Offsites/Civil…
Corn Production Cost Analysis Report: Manufacturing Process, Raw Materials Requi …
The latest report titled "Corn Production Cost Report" by Procurement Resource, a global procurement research and consulting firm, provides an in-depth cost analysis of the production process of the Corn. Read More: https://www.procurementresource.com/production-cost-report-store/corn
Report Features - Details
Product Name - Corn Production
Segments Covered
Manufacturing Process: Process Flow, Material Flow, Material Balance
Raw Material and Product/s Specifications: Raw Material Consumption, Product and Co-Product Generation, Capital Investment
Land and Site Cost: Offsites/Civil Works, Equipment Cost, Auxiliary Equipment…
Crude Oil Production Cost Analysis Report: Manufacturing Process, Raw Materials …
The latest report titled "Crude Oil Production Cost Report" by Procurement Resource, a global procurement research and consulting firm, provides an in-depth cost analysis of the production process of the Crude Oil. Read More: https://www.procurementresource.com/production-cost-report-store/crude-oil
Report Features - Details
Product Name - Crude Oil
Segments Covered
Manufacturing Process: Process Flow, Material Flow, Material Balance
Raw Material and Product/s Specifications: Raw Material Consumption, Product and Co-Product Generation, Capital Investment
Land and Site Cost: Offsites/Civil Works, Equipment Cost,…