Press release
Green Ammonia Production Cost Analysis and Setup Requirements in 2025
IntroductionGreen ammonia is a sustainable chemical compound produced by synthesizing hydrogen-generated via electrolysis of water using renewable energy-with nitrogen extracted from the air. Unlike conventional ammonia, which relies on fossil fuels, green ammonia is carbon-free and offers a clean alternative for use in fertilizers, energy storage, and as a zero-emission fuel, especially in shipping and power generation. Its production plays a crucial role in decarbonizing agriculture and heavy industries, contributing to global climate goals.
Setting up a green ammonia production plant involves securing renewable electricity, installing water electrolysis units, air separation systems, and ammonia synthesis loops. Efficient integration, location near renewable sources, and regulatory approvals are key for viability.
IMARC Group's report, titled "Green Ammonia Production Cost Analysis 2025: Industry Trends, Plant Setup, Machinery, Raw Materials, Investment Opportunities, Cost and Revenue," provides a complete roadmap for setting up a green ammonia production plant. It covers a comprehensive market overview to micro-level information such as unit operations involved, raw material requirements, utility requirements, infrastructure requirements, machinery and technology requirements, manpower requirements, packaging requirements, transportation requirements, etc.
Request for a Sample Report: https://www.imarcgroup.com/green-ammonia-manufacturing-plant-project-report/requestsample
Green Ammonia Industry Outlook 2025
The green ammonia industry is on track for explosive growth by 2025, fueled by global decarbonization efforts, declining renewable energy costs, and surging demand across fertilizer, energy storage, and maritime fuel sectors. With projected mid year 2025 market size in the hundreds of millions and CAGRs between ~45 % and 68 %, investments in electrolyzer efficiency and integrated renewables are rapidly making green ammonia more competitive. Regions like Europe, Asia Pacific, and North America lead capacity build out, supported by policies, infrastructure expansion, and offtake agreements-positioning green ammonia as a cornerstone of the clean energy transition.
Buy Now: https://www.imarcgroup.com/checkout?id=28030&method=1911
Key Insights for setting up an Green Ammonia Production Plant
Detailed Process Flow
o Product Overview
o Unit Operations Involved
o Mass Balance and Raw Material Requirements
o Quality Assurance Criteria
o Technical Tests
Project Details, Requirements and Costs Involved:
o Land, Location and Site Development
o Plant Layout
o Machinery Requirements and Costs
o Raw Material Requirements and Costs
o Packaging Requirements and Costs
o Transportation Requirements and Costs
o Utility Requirements and Costs
o Human Resource Requirements and Costs
Capital Expenditure (CapEx) and Operational Expenditure (OpEx) Analysis:
Project Economics:
o Capital Investments
o Operating Costs
o Expenditure Projections
o Revenue Projections
o Taxation and Depreciation
o Profit Projections
o Financial Analysis
Profitability Analysis:
o Total Income
o Total Expenditure
o Gross Profit
o Gross Margin
o Net Profit
o Net Margin
Key Cost Components
• Raw Materials: Costs for feedstocks like glucose, ammonia, enzymes, and microbial strains used in fermentation or synthesis.
• Machinery & Equipment: Fermenters, bioreactors, centrifuges, filtration units, dryers, and packaging systems.
• Land & Infrastructure: Cost of acquiring land, constructing production buildings, utilities setup (water, electricity, steam).
• Labor & Staffing: Hiring skilled workers, scientists, and plant operators for production and quality control.
• Licensing & Compliance: Expenses for regulatory approvals, environmental clearances, and safety certifications.
• R&D and Technology: Investment in process optimization, strain improvement, and product innovation.
Economic Trends Influencing Green Ammonia Plant Setup Costs 2025
• Declining Renewable Energy Costs: The falling prices of solar and wind power are reducing the operational costs of electrolyzers, making green ammonia production more economically viable.
• Electrolyzer Cost Reduction: Technological advancements and mass production of electrolyzers (e.g., PEM, alkaline) are significantly lowering capital expenditure for hydrogen generation-one of the core components of green ammonia plants.
• Government Incentives and Subsidies: Many countries are offering tax credits, grants, and green hydrogen/ammonia production incentives, helping offset initial setup costs and encouraging private investments.
• Supply Chain Volatility: Global inflation, logistical disruptions, and shortages in components (like semiconductors, steel, or compressors) may temporarily inflate construction and equipment costs.
• Carbon Pricing and Emissions Regulations: Rising carbon taxes and stricter emissions standards make green ammonia more competitive against fossil-based alternatives, shifting investment toward low-carbon infrastructure.
• Economies of Scale: Larger green ammonia projects are achieving lower per-unit setup costs through integrated facilities and bulk procurement strategies, pushing the industry toward scaled deployment.
• Interest Rates and Financing Climate: Higher interest rates or tight credit markets can impact financing options and increase borrowing costs for new plant development.
• Localized Infrastructure Development: Regions investing in renewable power grids, hydrogen hubs, and export terminals are seeing lower green ammonia setup costs due to improved logistics and resource availability.
Speak to an Analyst for Customized Report:
https://www.imarcgroup.com/request?type=report&id=28030&flag=C
Challenges and Considerations for Investors
• High Capital Costs: Setting up green ammonia plants requires significant investment in renewable energy infrastructure, electrolyzers, air separation units, and ammonia synthesis technologies.
• Technology Maturity: Electrolyzer and green ammonia synthesis technologies are still evolving, which may pose risks related to efficiency, reliability, and scalability.
• Energy Intensity: The production process demands a large and consistent supply of renewable electricity, requiring proximity to solar, wind, or hydro resources and robust energy storage solutions.
• Infrastructure and Logistics: Transporting and storing ammonia safely requires specialized infrastructure, which may not yet be available in many regions.
• Market Uncertainty: While demand is projected to rise, green ammonia still competes with cheaper, fossil-based alternatives in fertilizer and fuel markets, affecting pricing and adoption rates.
• Regulatory Landscape: Varying government policies, certification standards, and evolving international regulations can affect project feasibility and market access.
• Supply Chain Constraints: Limited availability of electrolyzers, skilled labor, and critical materials like rare earth metals may delay project timelines and increase setup costs.
• Long Payback Periods: Due to high upfront investment and uncertain market maturity, investors may face longer timelines to achieve returns, making financial planning crucial.
Conclusion
Green ammonia represents a pivotal solution in the transition toward a low-carbon future, offering sustainable alternatives in agriculture, energy storage, and transportation. While the industry is rapidly advancing with strong policy support and falling renewable energy costs, investors must carefully weigh challenges such as high capital requirements, technological uncertainties, and infrastructure needs. Strategic planning, technological partnerships, and alignment with regulatory frameworks will be key to successful project execution. For those positioned early and wisely, green ammonia plant investments offer long-term potential in shaping the global clean energy landscape.
About Us:
IMARC Group is a global management consulting firm that helps the world's most ambitious changemakers to create a lasting impact. The company excel in understanding its client's business priorities and delivering tailored solutions that drive meaningful outcomes. We provide a comprehensive suite of market entry and expansion services. Our offerings include thorough market assessment, feasibility studies, company incorporation assistance, factory setup support, regulatory approvals and licensing navigation, branding, marketing and sales strategies, competitive landscape, and benchmarking analyses, pricing and cost research, and procurement research.
Contact Us:
IMARC Group
134 N 4th St. Brooklyn, NY 11249, USA
Email: sales@imarcgroup.com
Tel No:(D) +91 120 433 0800
United States: +1-631-791-1145
This release was published on openPR.
Permanent link to this press release:
Copy
Please set a link in the press area of your homepage to this press release on openPR. openPR disclaims liability for any content contained in this release.
You can edit or delete your press release Green Ammonia Production Cost Analysis and Setup Requirements in 2025 here
News-ID: 4092401 • Views: …
More Releases from IMARC Group
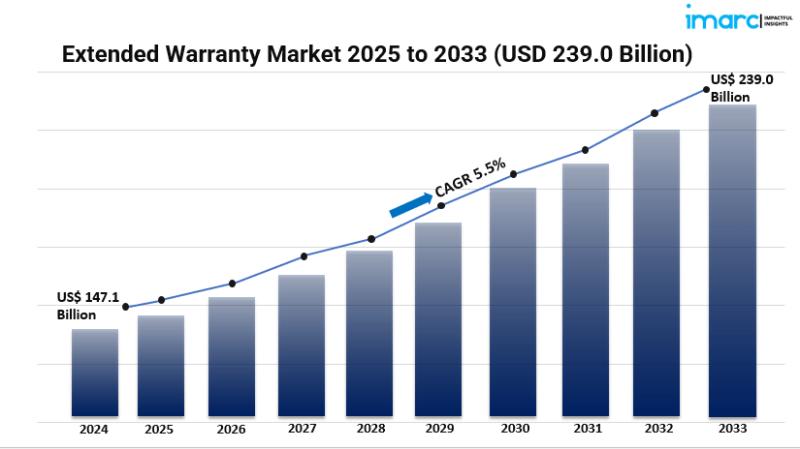
Extended Warranty Market 2025: Manufacturers, Retailers & Fleet Operators
The global extended warranty market reached a valuation of USD 147.1 billion in 2024 and is projected to expand to USD 239.0 billion by 2033, growing at a CAGR of 5.5% during 2025-2033. This growth is driven by increasing consumer demand for financial protection against unexpected product failures, rising sales of high-value items, and the growing complexity of consumer electronics, appliances, and vehicles. Additionally, the integration of digital technologies and…
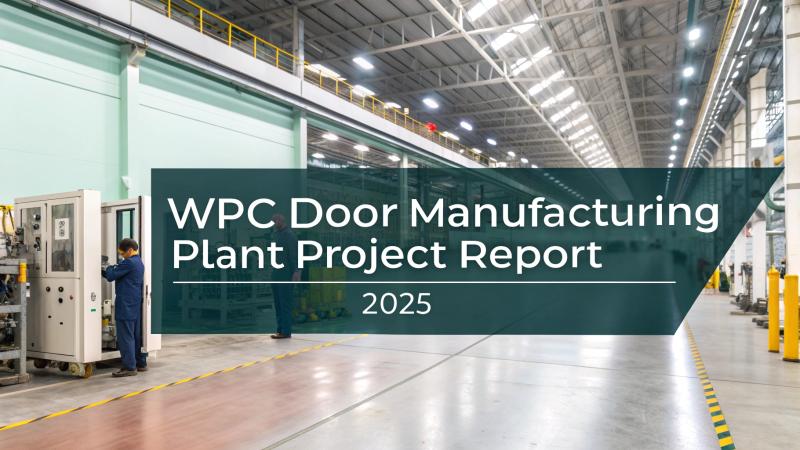
WPC Door Manufacturing Plant Setup 2025: Detailed Project Report, Requirements a …
WPC (Wood Plastic Composite) doors are advanced, eco-friendly alternatives to traditional wooden doors, made from a blend of wood fibers and thermoplastic resins. They offer durability, moisture resistance, termite resistance, and low maintenance, making them suitable for residential, commercial, and institutional applications. Their versatility in design and finishing has increased their popularity in modern construction.
Establishing a WPC door plant requires sourcing raw materials such as wood fiber and polymer resins,…
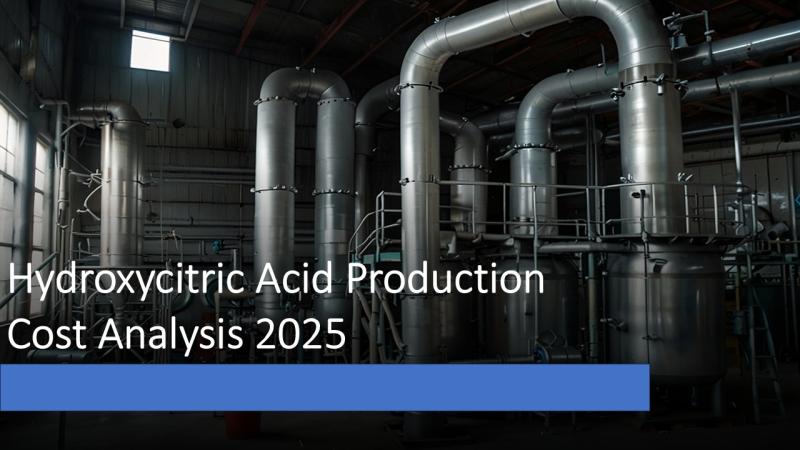
Hydroxycitric Acid Plant Cost 2025: Business Plan, Machinery Details and Industr …
Setting up a hydroxycitric acid production facility necessitates a detailed market analysis alongside granular insights into various operational aspects, including unit processes, raw material procurement, utility provisions, infrastructure setup, machinery and technology specifications, workforce planning, logistics, and financial considerations.
IMARC Group's report titled "Hydroxycitric Acid Production Cost Analysis Report 2025: Industry Trends, Plant Setup, Machinery, Raw Materials, Investment Opportunities, Cost and Revenue" offers a comprehensive guide for establishing a hydroxycitric acid…
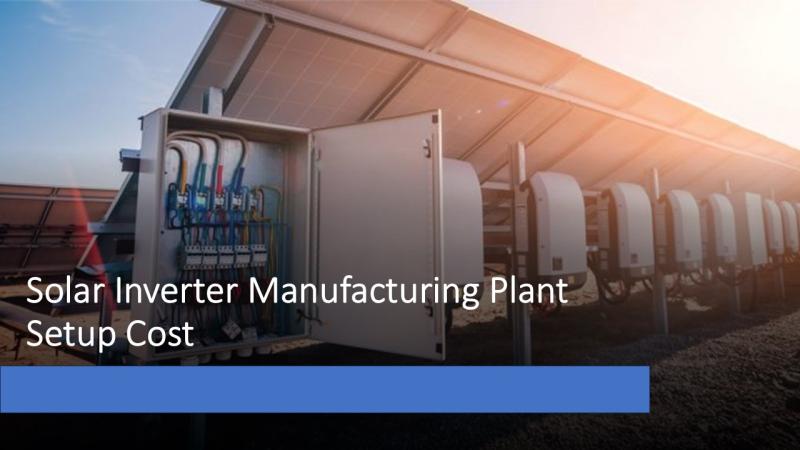
Solar Inverter Manufacturing Plant Cost 2025: Feasibility and Profitability Road …
Setting up a solar inverter manufacturing facility necessitates a detailed market analysis alongside granular insights into various operational aspects, including unit processes, raw material procurement, utility provisions, infrastructure setup, machinery and technology specifications, workforce planning, logistics, and financial considerations.
IMARC Group's report titled "Solar Inverter Manufacturing Plant Project Report 2025: Industry Trends, Plant Setup, Machinery, Raw Materials, Investment Opportunities, Cost and Revenue" offers a comprehensive guide for establishing a solar inverter…
More Releases for Cost
Egg Powder Manufacturing Plant Setup Cost | Cost Involved, Machinery Cost and In …
IMARC Group's report titled "Egg Powder Manufacturing Plant Project Report 2024: Industry Trends, Plant Setup, Machinery, Raw Materials, Investment Opportunities, Cost and Revenue" provides a comprehensive guide for establishing an egg powder manufacturing plant. The report covers various aspects, ranging from a broad market overview to intricate details like unit operations, raw material and utility requirements, infrastructure necessities, machinery requirements, manpower needs, packaging and transportation requirements, and more.
In addition to…
Glucose Manufacturing Plant Cost Report 2024: Requirements and Cost Involved
IMARC Group's report titled "Glucose Manufacturing Plant Project Report 2024: Industry Trends, Plant Setup, Machinery, Raw Materials, Investment Opportunities, Cost and Revenue" provides a comprehensive guide for establishing a glucose manufacturing plant. The report covers various aspects, ranging from a broad market overview to intricate details like unit operations, raw material and utility requirements, infrastructure necessities, machinery requirements, manpower needs, packaging and transportation requirements, and more.
In addition to the operational…
Fatty Alcohol Production Cost Analysis: Plant Cost, Price Trends, Raw Materials …
Syndicated Analytics' latest report titled "Fatty Alcohol Production Cost Analysis 2023-2028: Capital Investment, Manufacturing Process, Operating Cost, Raw Materials, Industry Trends and Revenue Statistics" includes all the essential aspects that are required to understand and venture into the fatty alcohol industry. This report is based on the latest economic data, and it presents comprehensive and detailed insights regarding the primary process flow, raw material requirements, reactions involved, utility costs, operating costs, capital…
Acetaminophen Production Cost Analysis Report: Manufacturing Process, Raw Materi …
The latest report titled "Acetaminophen Production Cost Report" by Procurement Resource a global procurement research and consulting firm, provides an in-depth cost analysis of the production process of the Acetaminophen. Read More: https://www.procurementresource.com/production-cost-report-store/acetaminophen
Report Features - Details
Product Name - Acetaminophen
Process Included - Acetaminophen Production From Phenol
Segments Covered
Manufacturing Process: Process Flow, Material Flow, Material Balance
Raw Material and Product/s Specifications: Raw Material Consumption, Product and Co-Product Generation, Capital Investment
Land and Site Cost: Offsites/Civil…
Corn Production Cost Analysis Report: Manufacturing Process, Raw Materials Requi …
The latest report titled "Corn Production Cost Report" by Procurement Resource, a global procurement research and consulting firm, provides an in-depth cost analysis of the production process of the Corn. Read More: https://www.procurementresource.com/production-cost-report-store/corn
Report Features - Details
Product Name - Corn Production
Segments Covered
Manufacturing Process: Process Flow, Material Flow, Material Balance
Raw Material and Product/s Specifications: Raw Material Consumption, Product and Co-Product Generation, Capital Investment
Land and Site Cost: Offsites/Civil Works, Equipment Cost, Auxiliary Equipment…
Crude Oil Production Cost Analysis Report: Manufacturing Process, Raw Materials …
The latest report titled "Crude Oil Production Cost Report" by Procurement Resource, a global procurement research and consulting firm, provides an in-depth cost analysis of the production process of the Crude Oil. Read More: https://www.procurementresource.com/production-cost-report-store/crude-oil
Report Features - Details
Product Name - Crude Oil
Segments Covered
Manufacturing Process: Process Flow, Material Flow, Material Balance
Raw Material and Product/s Specifications: Raw Material Consumption, Product and Co-Product Generation, Capital Investment
Land and Site Cost: Offsites/Civil Works, Equipment Cost,…