Press release
Aluminium Cans Manufacturing Plant Cost Report 2024: Business Plan, Raw Material Requirements, Cost and Revenue
IMARC Group's report titled "Aluminium Cans Manufacturing Plant Project Report 2024: Industry Trends, Plant Setup, Machinery, Raw Materials, Investment Opportunities, Cost and Revenue" provides a comprehensive guide for establishing an aluminium cans manufacturing plant. The report covers various aspects, ranging from a broad market overview to intricate details like unit operations, raw material and utility requirements, infrastructure necessities, machinery requirements, manpower needs, packaging and transportation requirements, and more.In addition to the operational aspects, the report also provides in-depth insights into aluminium cans manufacturing process, project economics, encompassing vital aspects such as capital investments, project funding, operating expenses, income and expenditure projections, fixed and variable costs, direct and indirect expenses, expected ROI, net present value (NPV), profit and loss account, and thorough financial analysis, among other crucial metrics. With this comprehensive roadmap, entrepreneurs and stakeholders can make informed decisions and venture into a successful aluminium cans manufacturing unit.
Request for a Sample Report: https://www.imarcgroup.com/aluminium-cans-manufacturing-plant-project-report/requestsample
Customization Available:
• Plant Location
• Plant Capacity
• Machinery- Automatic/ Semi-automatic/ Manual
• List of Machinery Provider
Aluminium cans are lightweight, durable, and easily recyclable containers that are used to store various beverages, such as sodas, beer, and energy drinks. They consist of a cylindrical body with a pull-tab or stay-on-tab opening mechanism at the top, allowing people to easily open and drink beverages. They help prevent product spoilage and ensure product quality throughout the distribution and storage process. They provide an effective barrier against light and oxygen that can degrade the quality of the product. They are easy to open, transport, and dispose of, making them convenient for individuals. They are used in the packaging of household and industrial products, such as cleaning agents, automotive products, lubricants, and paints. They are also utilized for storing liquid medications, oral sprays, or topical treatments.
At present, the rising demand for beverages, including carbonated soft drinks, beer, energy drinks, and ready-to-drink (RTD) teas and coffees, is catalyzing the demand for convenient, lightweight, and recyclable packaging solutions. This represents one of the key factors propelling the growth of the market. Additionally, the convenience and portability of aluminium cans make them popular among people for on-the-go consumption. This, coupled with the thriving food and beverage (F&B) industry, is strengthening the market growth. In line with this, the growing awareness among the masses about the environmental benefits of aluminium cans, such as high recyclable rate compared to other packaging materials like plastic or glass, is positively influencing the market. Moreover, key players are focusing on innovations in aluminium can design and technology to improve product functionality, enhance branding opportunities, and differentiate products in the market, which is bolstering the growth of the market. Apart from this, the increasing adoption of aluminium cans in cosmetic and personal care products, such as aerosol sprays, deodorants, and hair styling products, is stimulating the market growth. Furthermore, the rising employment of aluminium cans in food packaging like canned soups, vegetables, fruits, and ready-to-eat (RTE) meals, as they provide a lightweight, durable, and protective packaging solution, is supporting the market growth.
Browse Full Report: https://www.imarcgroup.com/aluminium-cans-manufacturing-plant-project-report
Key Insights Covered the Aluminium Cans Plant Report
Market Coverage:
• Market Trends
• Market Breakup by Segment
• Market Breakup by Region
• Price Analysis
• Impact of COVID-19
• Market Forecast
Key Aspects Required for Setting Up Aluminium Cans Plant
Detailed Process Flow:
• Product Overview
• Unit Operations Involved
• Mass Balance and Raw Material Requirements
• Quality Assurance Criteria
• Technical Tests
Project Details, Requirements and Costs Involved:
• Land, Location and Site Development
• Plant Layout
• Machinery Requirements and Costs
• Raw Material Requirements and Costs
• Packaging Requirements and Costs
• Transportation Requirements and Costs
• Utility Requirements and Costs
• Human Resource Requirements and Costs
Project Economics:
• Capital Investments
• Operating Costs
• Expenditure Projections
• Revenue Projections
• Taxation and Depreciation
• Profit Projections
• Financial Analysis
Ask Analyst for Customization: https://www.imarcgroup.com/request?type=report&id=7279&flag=C
Key Questions Answered in This Report:
• How has the aluminium can market performed so far and how will it perform in the coming years?
• What is the market segmentation of the global aluminium can market?
• What is the regional breakup of the global aluminium can market?
• What are the price trends of various feedstocks in the aluminium can industry?
• What is the structure of the aluminium can industry and who are the key players?
• What are the various unit operations involved in an aluminium can manufacturing plant?
• What is the total size of land required for setting up an aluminium can manufacturing plant?
• What is the layout of an aluminium can manufacturing plant?
• What are the machinery requirements for setting up an aluminium can manufacturing plant?
• What are the raw material requirements for setting up an aluminium can manufacturing plant?
• What are the packaging requirements for setting up an aluminium can manufacturing plant?
• What are the transportation requirements for setting up an aluminium can manufacturing plant?
• What are the utility requirements for setting up an aluminium can manufacturing plant?
• What are the human resource requirements for setting up an aluminium can manufacturing plant?
• What are the infrastructure costs for setting up an aluminium can manufacturing plant?
• What are the capital costs for setting up an aluminium can manufacturing plant?
• What are the operating costs for setting up an aluminium can manufacturing plant?
• What should be the pricing mechanism of the final product?
• What will be the income and expenditures for an aluminium can manufacturing plant?
• What is the time required to break even?
• What are the profit projections for setting up an aluminium can manufacturing plant?
• What are the key success and risk factors in the aluminium can industry?
• What are the key regulatory procedures and requirements for setting up an aluminium can manufacturing plant?
• What are the key certifications required for setting up an aluminium can manufacturing plant?
Contact Us:
IMARC Group
134 N 4th St. Brooklyn, NY 11249, USA
Email: sales@imarcgroup.com
Tel No:(D) +91 120 433 0800
United States: +1-631-791-1145 | United Kingdom: +44-753-713-2163
About Us:
IMARC Group is a leading market research company that offers management strategy and market research worldwide. We partner with clients in all sectors and regions to identify their highest-value opportunities, address their most critical challenges, and transform their businesses.
IMARC Group's information products include major market, scientific, economic and technological developments for business leaders in pharmaceutical, industrial, and high technology organizations. Market forecasts and industry analysis for biotechnology, advanced materials, pharmaceuticals, food and beverage, travel and tourism, nanotechnology and novel processing methods are at the top of the company's expertise.
This release was published on openPR.
Permanent link to this press release:
Copy
Please set a link in the press area of your homepage to this press release on openPR. openPR disclaims liability for any content contained in this release.
You can edit or delete your press release Aluminium Cans Manufacturing Plant Cost Report 2024: Business Plan, Raw Material Requirements, Cost and Revenue here
News-ID: 3548108 • Views: …
More Releases from IMARC Group
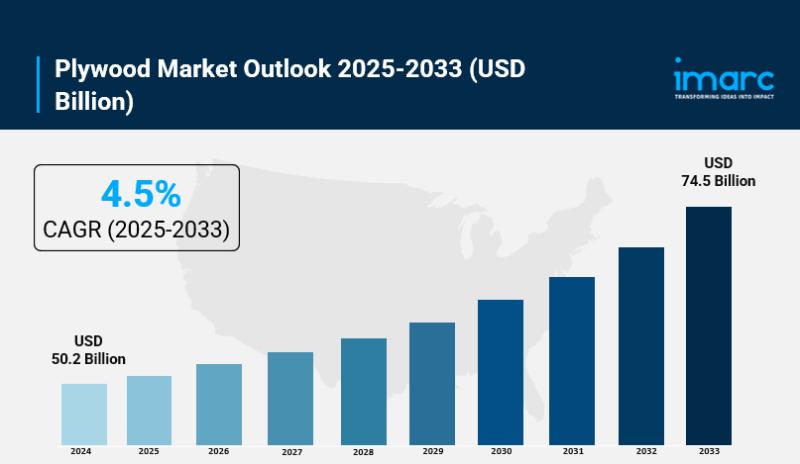
Global Plywood Market Size, Share, Industry Overview, Latest Insights and Foreca …
IMARC Group, a leading market research company, has recently releases a report titled "Plywood Market Size, Share, Trends and Forecast by Residential and Commercial Application, New Construction and Replacement Sector, and Region, 2025-2033." The study provides a detailed analysis of the industry, including the global plywood market size, share, trends, and growth forecast. The report also includes competitor and regional analysis and highlights the latest advancements in the market.
Plywood…
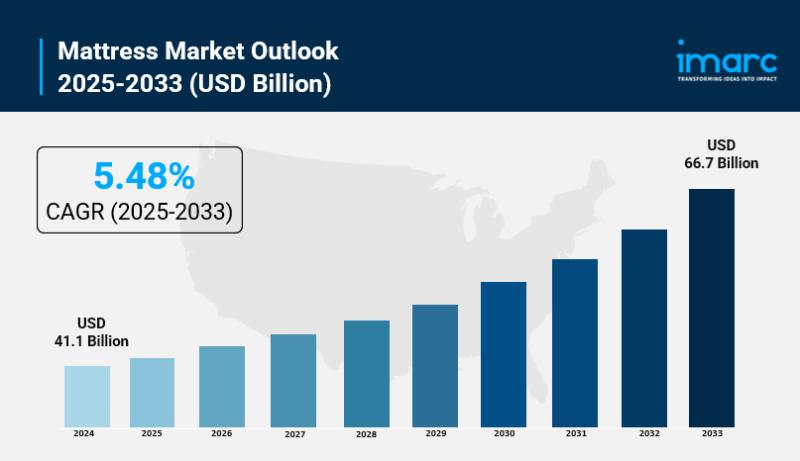
Mattress Market Size, Share, Industry Trends, Growth and Forecast 2025-2033
IMARC Group, a leading market research company, has recently releases a report titled "Mattress Market Report by Product (Innerspring Mattresses, Memory Foam Mattresses, Latex Mattresses, and Others), Distribution Channel (Online Distribution, Offline Distribution), Size (Twin or Single Size, Twin XL Size, Full or Double Size, Queen Size, King Size Mattress, and Others), Application (Domestic, Commercial), and Region 2025-2033." The study provides a detailed analysis of the industry, including the global…
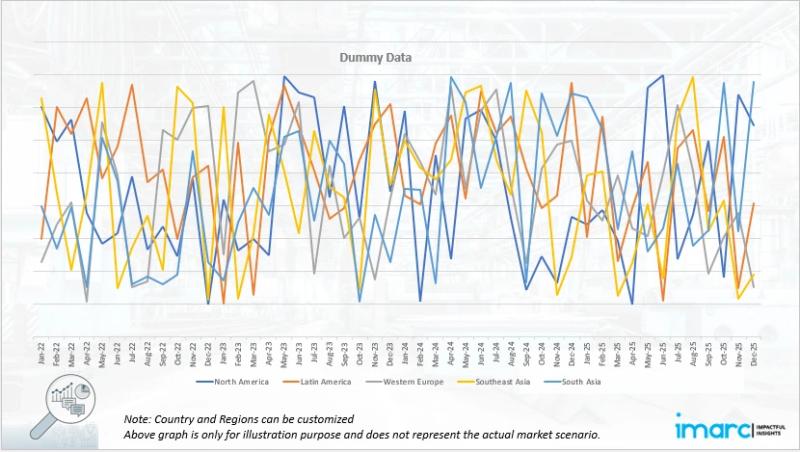
Global Apixaban Prices Q2 2025: Chart, Analysis & Forecast
North America Apixaban Prices Movement Q2:
Apixaban Prices in USA:
In Q2 2025, apixaban prices in the USA reached 44,617 USD/MT in June. Prices rose steadily, supported by consistent demand for cardiovascular therapies, higher API production and compliance costs, and stable healthcare utilization. Generics moderated volatility, yet firm supply chains and sustained consumption maintained a controlled, input cost-driven price increase.
Get the Real-Time Prices Analysis: https://www.imarcgroup.com/apixaban-pricing-report/requestsample
Note: The analysis can be tailored to align…
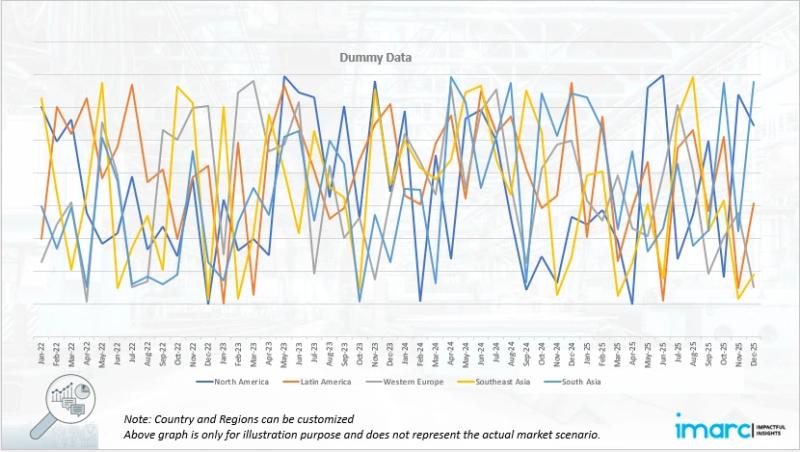
Global Nitrobenzene Prices Q1 2025: Chart, Analysis & Forecast
North America Nitrobenzene Prices Movement Q1:
Nitrobenzene Prices in USA:
In Q1 2025, nitrobenzene prices in the USA reached 1,450 USD/MT in March. Firm demand from aniline and MDI sectors supported prices, while harsh winter weather disrupted production and logistics. Tight benzene availability, caused by refinery fluctuations, added upstream cost pressures, straining supply chains and shaping overall market dynamics.
Get the Real-Time Prices Analysis:
https://www.imarcgroup.com/nitrobenzene-pricing-report/requestsample
Note: The analysis can be tailored to align with…
More Releases for Cost
Egg Powder Manufacturing Plant Setup Cost | Cost Involved, Machinery Cost and In …
IMARC Group's report titled "Egg Powder Manufacturing Plant Project Report 2024: Industry Trends, Plant Setup, Machinery, Raw Materials, Investment Opportunities, Cost and Revenue" provides a comprehensive guide for establishing an egg powder manufacturing plant. The report covers various aspects, ranging from a broad market overview to intricate details like unit operations, raw material and utility requirements, infrastructure necessities, machinery requirements, manpower needs, packaging and transportation requirements, and more.
In addition to…
Glucose Manufacturing Plant Cost Report 2024: Requirements and Cost Involved
IMARC Group's report titled "Glucose Manufacturing Plant Project Report 2024: Industry Trends, Plant Setup, Machinery, Raw Materials, Investment Opportunities, Cost and Revenue" provides a comprehensive guide for establishing a glucose manufacturing plant. The report covers various aspects, ranging from a broad market overview to intricate details like unit operations, raw material and utility requirements, infrastructure necessities, machinery requirements, manpower needs, packaging and transportation requirements, and more.
In addition to the operational…
Fatty Alcohol Production Cost Analysis: Plant Cost, Price Trends, Raw Materials …
Syndicated Analytics' latest report titled "Fatty Alcohol Production Cost Analysis 2023-2028: Capital Investment, Manufacturing Process, Operating Cost, Raw Materials, Industry Trends and Revenue Statistics" includes all the essential aspects that are required to understand and venture into the fatty alcohol industry. This report is based on the latest economic data, and it presents comprehensive and detailed insights regarding the primary process flow, raw material requirements, reactions involved, utility costs, operating costs, capital…
Acetaminophen Production Cost Analysis Report: Manufacturing Process, Raw Materi …
The latest report titled "Acetaminophen Production Cost Report" by Procurement Resource a global procurement research and consulting firm, provides an in-depth cost analysis of the production process of the Acetaminophen. Read More: https://www.procurementresource.com/production-cost-report-store/acetaminophen
Report Features - Details
Product Name - Acetaminophen
Process Included - Acetaminophen Production From Phenol
Segments Covered
Manufacturing Process: Process Flow, Material Flow, Material Balance
Raw Material and Product/s Specifications: Raw Material Consumption, Product and Co-Product Generation, Capital Investment
Land and Site Cost: Offsites/Civil…
Corn Production Cost Analysis Report: Manufacturing Process, Raw Materials Requi …
The latest report titled "Corn Production Cost Report" by Procurement Resource, a global procurement research and consulting firm, provides an in-depth cost analysis of the production process of the Corn. Read More: https://www.procurementresource.com/production-cost-report-store/corn
Report Features - Details
Product Name - Corn Production
Segments Covered
Manufacturing Process: Process Flow, Material Flow, Material Balance
Raw Material and Product/s Specifications: Raw Material Consumption, Product and Co-Product Generation, Capital Investment
Land and Site Cost: Offsites/Civil Works, Equipment Cost, Auxiliary Equipment…
Crude Oil Production Cost Analysis Report: Manufacturing Process, Raw Materials …
The latest report titled "Crude Oil Production Cost Report" by Procurement Resource, a global procurement research and consulting firm, provides an in-depth cost analysis of the production process of the Crude Oil. Read More: https://www.procurementresource.com/production-cost-report-store/crude-oil
Report Features - Details
Product Name - Crude Oil
Segments Covered
Manufacturing Process: Process Flow, Material Flow, Material Balance
Raw Material and Product/s Specifications: Raw Material Consumption, Product and Co-Product Generation, Capital Investment
Land and Site Cost: Offsites/Civil Works, Equipment Cost,…