Press release
A High-Energy Venture between Earth and Sky
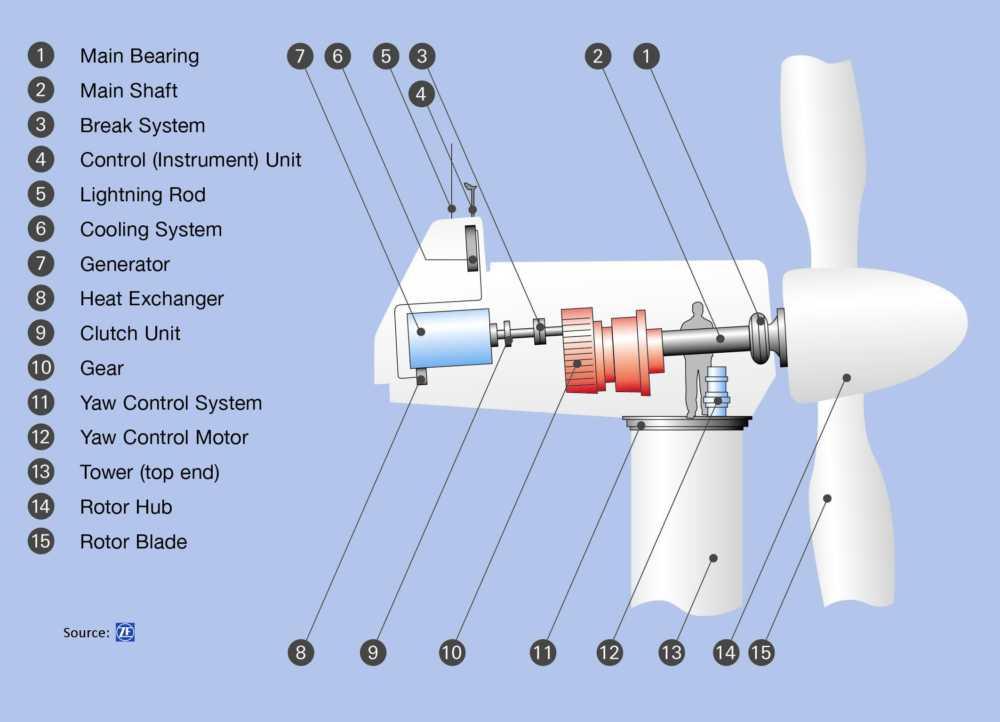
The size alone of wind generator components means greatly increased demands are placed on the heat treatment of steel components.
The very best is the only standard good enough for wind generator technologies. This counts too, for the heat treatment of the huge gears in their transmissions, some as much as two meters in diameter, mounted in turrets 150 meters above the ground.
The windmills' 20-year service life is covered by functional guarantees. The vanes of these giants will spin more than 160,000 hours in that time when the wind is blowing up there between the earth and the sky. Proper heat treatment is what makes this possible.
The technician at the centre of the photo almost disappear between the huge box furnaces they are manufacturing for the US- plant. The furnaces are assembled at Ipsen’s plant in Kleve, Germany, then shipped to the United States for final installation. Their capacity is greater than any other existing furnaces. Automated process control is provided by Ipsen AutoMag systems.
Ipsen is the world’s leading manufacturer of premium heat treatment equipment for steel components. For manufacturing of gearboxes for latest-generation wind generators, Ipsen is contributing highly specialised heat treatment systems to meet the demanding hardness and surface quality requirements for the gear components. At the same time, Ipsen has taken a giant leap in terms of the size of the heat treatment furnaces for wind gears: they can take 15 tonne batches comprising transmission components up to two meters in diameter and still subject them to exacting, automated process control.
The furnaces normally used to treat standard passenger car transmission components have a capacity of roughly 0.3 cubic meters, about the size of a normal home freezer. Those found in the Gainesville plant are practically gigantic – more than an order of magnitude larger.
The Ipsen equipment going into the new plant includes the following components:
- 3 box furnaces (max. 1050°C) with 4.6 cubic metre load volume (1.5 x 1.8 x 1.7 m) set up for charges up to 7 tonnes
- 2 nitriding furnaces (max. 650°C) with 6.3 cubic meter load volume (2 m diameter x 3 m high)
- 1 50 cubic metre Ipsen SuperQuench oil bath for rapid quenching of components in hardening oil with larger drive motors and agitators than the standard model, and optimally routed oil flow.
- 1 gas heated preheating furnace (max. 450°C) to reduce preheating times on the other furnaces – can also be used as a tempering furnace when needed.
- 1 electricly heated tempering furnace (max. 450°C)
- 1 stainless steel component washer
- 2 loaders – specially dimensioned transport- and lift-vehicles able to transport components weighing up to 7 tonnes at up to 1,000°C between furnaces or from furnace to oil bath, largely insulated from the cooling effects of the air in the plant.
The loaders have been optimised not only to insulate the hot components from the cooler surrounding air, but also for optimal transport velocity. Every second counts between furnace and oil bath and the transport times have been precisely defined.
The nitriding furnaces were constructed to fit the largest of the windmill transmission components. Able to take loads up to 15 tonnes, these furnaces can hold several of the massive ring gears at a time. Given that these gears need more than 30 hours in the furnace, with careful planning, the plant can produce 1,000 of these special transmissions per annum.
The three box furnaces are lined with special ceramic insulation rather than the usual fibre insulation, lengthening the service life of the entire furnace construction.
The entire facility has been designed with a 3-shift, six-day, 50 week work-year in mind. The layout as such supports a manufacturing volume of approximately 1,000 units per annum. Ipsen's tried and tested AutoMag control software package will run all aspects of the heat treatment processes. It meticulously documents the treatment of each individual component and guarantees high-quality, reproducible results from the automated manufacturing process no matter the number of components being treated in the furnaces at any given time.
The characteristics that heat treatment gives to components are extremely important in wind generator transmissions – their surface hardness has direct bearing on their durability and therefore their service life. Wind generators are usually built for 20-year of more or less continuous operation. In those 20 years, the blades of a 150-metre high windmill will rotate about 180,000,000 (180 million) times at 13-20 rpm, spinning the electrical generator attached to them at a 1:100 gear ratio about 17,000,000,000 times (17 thousand million times in UK terminology, 17 billion times in US terms).
Transmission components that are expected to cope with this kind of endurance test have to be extremely tough. The necessary durability can only be achieved with specialised heat treatment processes that produce components with exactly defined characteristics.
Today's wind generators produce 2.5 megawatts. The next generation of these giants, capable of producing 3 megawatts, is on its way.
The size alone of wind generator components means greatly increased demands are placed on the heat treatment of steel components. Their ring gears can be two meters in diameter; the matching axle shafts up to three metres long. Ipsen developed heat treatment equipment to meet this challenge – and the custom-tailored processes and software solutions necessary, too.
Even the most compact of a wind generator's transmission gear sets are generally handled with cranes. Though they are only about 30 centimetres across, but weigh over 50 kilograms. These transmissions are built to take the windmill's roughly 0.3 rpm rotation and step it up by a factor of 100 so that the generator is delivering under maximised efficiency.
The focus of development centres around the fact that wind generators need to "run forever" –that is, if possible, maintenance free over a service life of 20 years. Their sheer size multiplies the cost of repair astronomically, as does the difference between a location on- or off-shore ... not to mention the loss of profit if power generation is stopped.
Wind power durability aspects – background information
The organization “New Zealand Windfarms” recently experienced just how unpleasant transmission failures can be in high tech windmills. Mechanical defects in their twin-rotor systems caused losses of 6.3 million New Zealand dollars (ca. 3.4 million euros). The complete breakdown of the affected turbines was caused by enormous wear to transmission components that had undergone faulty heat treatment. The reported cost of the subsequent retrofitting and repairs to their several hundred windmills was 24 million New Zealand dollars (13 million euros).
The broad spectrum of Ipsen furnaces tailor-made for specific heat-treatment requirements can help avoid such mass-failures. Ipsen is specialized in the production of furnaces that can be used to meet the most demanding needs in the heat-treatment of metal components.
The one piece, 50 cubic-metre oil bath chamber. It provides exactly defined quench processes alongside precise process control. It is prepared for automated manufacturing. The Ipsen systems are not only capable of producing and reproducing demanding quality-processes to exacting standards, but also of documenting them just as precisely – if necessary, for each and every individual component of 1000 annually produced special transmissions.
Ipsen's furnaces are conceived and built with automated operation in mind. This allows handling errors to be avoided systematically. All Ipsen equipment can continuously monitor and document all process parameters of the entire heat treatment process. This means quality is not left to chance, it is fully documentable and reproducible.
Ipsen's equipment is characterized by consistently excellent manufacturing quality and low operating and follow-up costs. Dramatic transmissions failures due to faulty heat-treatment like those described above can be avoided. Expensive down time – decisive for wind generators – and consequent earnings losses are out of the picture.
For more than 60 years, Ipsen has specialized in developing and building high-value industrial furnaces and heat-treatment equipment for parts and components. The global market leader has made more contributions to the development of heat treatment than virtually any other company. Ipsen is always striving to develop innovative technologies that make it possible to manufacture better-quality steel. As a systems provider, the Company delivers the latest technology to its customers in a package that includes perfectly synchronized hardware and software. The Company has production sites in Europe, America and Asia and agencies in 34 countries. Its customers are primarily companies in the automotive and aerospace industries, the tool manufacturing industry and the mechanical engineering industry.
Ipsen International GmbH
Flutstraße 78
D-47533 Kleve
Uta Kirschnick
Head of Marketing and Communication
This release was published on openPR.
Permanent link to this press release:
Copy
Please set a link in the press area of your homepage to this press release on openPR. openPR disclaims liability for any content contained in this release.
You can edit or delete your press release A High-Energy Venture between Earth and Sky here
News-ID: 158795 • Views: …
More Releases from Ipsen International GmbH, Germany
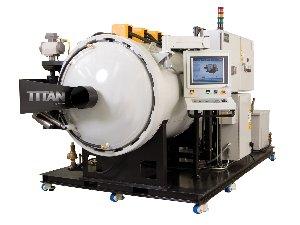
Times are Hard, Hard is Good
Kleve, March 2010 – Some heat treatment furnaces are as big as a townhouse. The new Ipsen Titan furnace, on the other hand, fits in a garage and is especially user-friendly and energy-efficient.
When hardening metals – most often steel – their structure is altered by the application of heat followed by rapid cooling to increase their mechanical durability.
Ipsen, the heat treatment experts from Kleve in Germany, now offer a…
More Releases for Wind
Global Wind Energy Market Insights, Forecast To 2025 | Aegis Wind, Aris Wind, Ar …
Wind energy is the kinetic energy produced by air flow.A form of solar energy conversion.
A variety of factors such as environmental concern, unstable crude, and need of alternative energy source are driving the wind energy market.
Request for discount@ https://www.researchtrades.com/discount/1681622
The Wind Energy market was valued at xx Million US$ in 2018 and is projected to reach xx Million US$ by 2025, at a CAGR of xx% during the forecast period. In…
Wind Energy Market looks to expand its size in Overseas Market | Aegis Wind, Are …
A new market study on Global Wind Energy Market with 100+ market data Tables, Pie Chart & Graphs is released that will provide complete assessment of the Market and covers evolving trends, current scenario analysis and growth factors, and industry validated market data. The research study provides market breakdown by revenue and volume (if applicable) and price history estimates for Global Wind Energy. Some are the key players from the…
Wind Turbine Operations and Maintenance Market | wind turbine maintenance, wind …
Market Research Reports Search Engine (MRRSE) has been serving as an active source to cater intelligent research report to enlighten both readers and investors. This research study titled “Wind Turbine Operations and Maintenance Market “
This research study analyzes the market for wind turbine operation and maintenance (O&M) in terms of revenue (US$ Mn). The wind turbine O&M market has been segmented on the basis of application and geography. The regional…
Global Small and Medium Wind Turbines Market 2018-2025 | Machinery Update : Berg …
Press Release – 20 Dec 2018
Research and Development News --
. .
Latest Update "Global Small and Medium Wind Turbines Market Insights, Forecast to 2025" with Industries Survey | Global Current Growth and Future.
' '
This report presents the worldwide Small and Medium Wind Turbines market size (value, production and consumption), splits the breakdown (data status 2013-2018 and forecast to 2025), by manufacturers, region, type and application.
This study also analyzes the market…
Global Small and Medium Wind Turbines Market 2017 - Bergey Wind Power, Gaia-Wind …
Latest Research Report titled " Global Small and Medium Wind Turbines Market Professional Survey Report 2017 " features Key Market Players, Segments, Applications. Report Presents Global Market Survey, Growth, Challenges and Forecast.
This report studies Small and Medium Wind Turbines in Global market, especially in North America, China, Europe, Southeast Asia, Japan and India, with production, revenue, consumption, import and export in these regions, from 2012 to 2016, and forecast to…
Small and Medium Wind Turbines Market 2017-Bergey Wind Power, Gaia-Wind, United …
Ampair
Evance Wind Turbines
Endurance Wind Power
Polaris America
Windspire Energy
Gaia-Wind
Kestrel Wind Turbines
Urban Green Energy
ElectroVent
MarketReports.biz, recently published a detailed market research study focused on the "Small and Medium Wind Turbines Market" across the global, regional and country level. The report provides 360° analysis of "Small and Medium Wind Turbines Market" from view of manufacturers, regions, product types and end industries. The research report analyses and provides the historical data along with current performance…